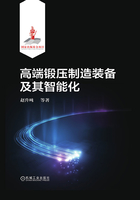
1.2 锻压装备在国民经济、社会发展和科学发展中所起的作用
锻压装备制造的零件具备高生产率、高性能和精确性的优势,在国民经济、社会发展和科学发展中起着举足轻重的作用。
1.2.1 新材料产业发展的需要
新材料涉及领域广泛,一般指新出现的具有优异性能和特殊功能的材料,或是传统材料改进后性能明显提高和产生新功能的材料,其范围随着经济发展、科技进步、产业升级不断发生变化。我国新材料产业“十二五”发展规划中将“高端金属结构材料”作为一个重要的发展领域。主要包括高品质特殊钢、新型轻合金材料等。这些材料大多需要用锻压设备加工来实现对原材料性能的显著改善,如高品质特殊钢中的耐高温、耐高压、耐腐蚀电站用钢、节镍型高性能不锈钢、高标准轴承钢、齿轮钢、模具、高强度紧固件用特种钢。新型合金材料中以轻质、高强、大规格、耐高温、耐腐蚀、耐疲劳的高性能铝合金、镁合金和钛合金为代表,主要应用于航空航天、高速铁路、汽车零部件、轨道列车等领域。
1.2.2 高端制造业的要求
高端装备制造业是以高新技术为引领,处于价值链高端和产业链核心环节,决定着整个产业链综合竞争力的战略性新兴产业,是现代产业体系的脊梁,是推动我国工业转型升级的引擎。在调整产业结构的背景下,高端装备制造业被认为是七大新兴产业中资金最密集、产业链最完备、见效最快的产业之一。高端装备主要包括传统产业转型升级和战略性新兴产业发展所需的高技术、高附加值装备。《国务院关于加快培育和发展战略性新兴产业的决定》明确的重点领域和方向包括航空装备、卫星及应用、轨道交通装备、海洋工程装备等。
目前航空、航天、兵器等国防工业的零部件都朝着大型化、整体化、精密化的方向发展,例如俄罗斯的安-22运输机机身采用750MN模锻水压机生产的投影面积达3.5m2的B95合金大型隔框整体模锻件共20个,共减少了800个零件,减轻飞机机体质量1000kg,减少机械加工工时15%~20%。再如某飞机的主要承力框,在原设计中采用分体锻造、整体焊接的结构,使用和试验结果表明,焊缝处疲劳寿命比母体约低30%,因此飞机设计目标寿命较低,仅2000飞行小时。由于承力框采用三部分焊接制造工艺,包含多个焊缝,焊接工序多、焊缝质量控制难度大,一个整框零件的生产周期长达6~7个月,成为制约飞机生产进度的瓶颈,中国第二重型机械集团有限公司(简称二重)万航模锻有限公司在2006年进行了大型钛框的锻件设计、研制和生产,并首次在国内成功研制出整体钛合金框模锻件。其中整框模锻件产品的加工周期由原来的6~7个月减少至3个月,机械加工工时节约45%。这些零件中很多为难变形材料诸如钛合金、高温合金,其变形抗力大、组织性能要求高,锻压时的工艺控制困难。特别随着现代航空装备对高性能、高减重、长寿命、高可靠性及低成本制造技术等需求的不断提高,现代飞机和发动机进一步向结构整体化、零件大型化的方向发展。大型模锻件的应用水平已成为先进飞机的标志之一。
美国波音747~787、A320~380客机的钛合金起落架,F-16战斗机钛合金机身隔框,D-10飞机的后支承环,915发动机机座,苏27~33战斗机钛合金大型结构件,GT25000舰用燃气轮机直径1.2m涡轮盘等都是在上述大型模锻水压机上模锻成形的。当今世界上航空制造业强国都拥有4.5万t以上的重型模锻液压机。美国拥有两台4.5万t模锻液压机,俄罗斯拥有两台7.5万t模锻液压机,法国拥有一台6.5万t模锻液压机。空中客车公司生产的A380客机起落架的成形,就是在俄罗斯7.5万t压力机上完成的。美国第四代战斗机F-22机身采用了4个长约4m、投影面积达5m2以上的TC4钛合金整体式隔框模锻件,大型钛合金模锻件的采用,大幅度提高了飞机结构效益水平,并且实现了高性能军机的制造。模锻件的大型化和整体化是航空锻压技术的发展方向,是实现飞机主承力结构整体化的重要条件。大型航空模锻件的制造离不开大型锻压设备,近年来中国相继成功研发了用于航空大飞机的400MN、800MN大型航空模锻液压机生产线、用于兵器炮管制造的360MN立式管材热挤压生产线、用于固体导弹发动机筒体旋压的100t立式数控强力旋压机,满足了中国国防工业的急需。用于航空航天以及卫星的零部件使用的材料多为轻质、耐高温、难变形合金,航空发动机涡轮盘需要挤压机开坯才能满足其性能要求,美国在350MN立式钢挤压机上为其开坯;美国将125MN卧式挤压机(德国在二战期间为制造军用飞机所需的大型铝合金及镁合金挤压材料而建造的大型挤压机)改造为145MN正反向双动挤压机,也用于大型飞机的铝合金、镁合金材料挤压,可生产长为32m、单位质量为134kg/m、宽为1016mm的型材。
船舶工业是为水上交通、海洋开发及国防建设提供技术装备的现代综合性产业,是军民结合的战略性产业。进一步发展壮大船舶工业,是提升我国综合国力的必然要求。海洋工程装备是人类在开发、利用和保护海洋活动中使用的各类装备的总称,是海洋经济发展的前提和基础,处于海洋产业价值链的核心环节。海洋工程装备制造业是战略性新兴产业的重要组成部分,也是高端装备制造业的重要方向,具有知识技术密集、物资资源消耗少、成长潜力大、综合效益好等特点,是发展海洋经济的先导性产业。船舶及海洋工程同样也离不开挤压机,如舰艇、船舶、汽艇等的船身结构件和甲板;潜艇潜望镜用大口径厚壁超长管;舰船用耐压、耐腐蚀不锈管;石油运输管等均需用挤压产品。
发展“技术先进、安全可靠、经济适用、节能环保”的轨道交通装备,是提升交通运输效率的保证,是实现资源节约和环境友好的有效途径,对国民经济和社会发展有较强的带动作用。随着我国轨道交通特别是高铁的高速发展,轨道交通装备业对节能、环保、安全性、可靠性的需求进一步增强,高速列车以及地铁车厢的覆盖件、集装箱和厢式货车大都采用挤压型材。
1.2.3 新能源产业要求
《国民经济和社会发展十二五规划纲要》指出:“新能源产业重点发展新一代核能、太阳能热利用和光伏光热发电、风电技术装备、智能电网、生物质能。开发利用、支持新能源产业发展,为在“十二五”时期继续促进能源发展方式转变,加快资源节约型和环境友好型国家建设,确保能源与经济、社会、环境的协调发展具有重要意义。”挤压机是新能源产业不可或缺的关键设备之一,如中国重型机械研究院的40MN锆管挤压机专为核电挤压核原料容器用高管而建设,500MN立式钢管挤压机采用镦挤技术为核电站生产主管道而建设。
新能源汽车是新能源产业的重要分支之一,节能与新能源汽车已成为国际汽车产业的发展方向,而轻量化则是实现新能源汽车的重要环节。铝合金材料以其质量轻、强度刚度高成为汽车轻量化的最佳使用材料。日本本田NSX全车用铝材达到31.3%。据杜克公司(Duker)调查,2009年有67款汽车(欧洲49款、日本18款)的铝合金用量达到182kg/辆。欧洲小汽车用铝量2010年不足100kg/辆,2012年已达到140kg/辆,预计2020年将增至200kg/辆;福特提出要在2020年前实现铝合金和钢在车身上的用量大致相等的目标;我国也提出单车用铝量目标2020年为190kg/辆,2030年达到350kg/辆。这些铝材大部分使用的是挤压产品,如保险杠、车窗、座椅等,复合板箱式车和冷藏式箱式车,其前顶轨、侧顶轨、前底轨等产品均为铝合金挤压型材。
1.2.4 汽车、铁路及船舶工业
2009年中国汽车产销量分别达1379.10万辆和1364.48万辆,至此中国成为世界汽车产销第一的国家。随着我国汽车工业一直保持快速发展的步伐,汽车中70%以上的零部件是依靠板料制作的,在汽车制造的冲压、焊装、涂装、总装四大工艺中,板料、模具、设备是覆盖件生产必不可少的三大硬件或三大要素。冲压是第一道工艺,相应的冲压设备也是四大工艺中投资最大、技术水平要求最高的,对汽车制造规模与质量保障极为重要。
目前中国的铁路装备制造业已带给世界更多、更快、更先进的高铁工程。中国铁路制造业制造的机车、车辆、钢轨、道岔、通信信号设备、大型施工机械,基本满足了中国铁路建设和发展的需要。目前中国的飞机、汽车制造装备还主要依赖进口,中国的铁路运输所采用的技术装备基本是由中国制造的。因为对铁路运输装备中零部件的力学性能要求高,因此超过一半以上的零部件是依靠锻压工艺制作的。这些零部件的制造,锻压设备是关键保障设备。例如西安轨道交通装备有限责任公司与天津市天锻压力机有限公司签订并实施了拉深滑块公称压力为85MN、压边滑块公称力40MN的铁路罐体封头制造用双动厚板拉深液压机,确保了大型罐体的国产化。
目前汽车、铁路等行业所需要的大型锻件,特别是重载汽车的曲轴大型锻件,采用锤锻的方式来生产,或只能采用铸件来代替锻件的方式。重型曲轴热模锻生产线的研制能大规模提高生产效率,降低锻件毛坯的锻造成本,提高锻件的锻造性能,满足汽车、铁路、造船等方面的发展需要。
国内从20世纪70年代开始制造热模锻压力机,同时开展锻造的自动化连线工作。目前,大量使用锤锻、摩擦压力机等的锻造厂都在更新设备,采用技术更优的热模锻压力机。热模锻自动生产线在锻造行业占据的份额越来越大,热模锻自动生产线设计也就越来越重要。目前,国外仅有两条160MN热模锻生产线,全球能够设计、制造的只有两家公司,都是外国公司,国内在该领域是空白的。随着我国汽车、铁路、造船等重要领域技术装备的快速发展,对大型锻件需求越来越旺盛,对大型热模锻生产线需求巨大。国内80MN以上的大型热模锻生产线的制造,均由二重设计、完成,该公司已经具备生产研发重型曲轴热模锻生产线的能力。根据国内外锻造行业的发展趋势,大型热模锻生产线的需求量巨大,有着广阔的市场前景。
二重制造的125MN热模锻压力机生产线,为我国的汽车和铁路的发展起到了良好的保障作用,现在世界上已有两台160MN热模锻压力机。我国目前拟研制重型曲轴热模锻生产线:配置ϕ1000辊锻机、160MN热模锻压力机、16MN切边机、2.5MN扭转机、20MN校正机,6400kW中频加热炉以及后续热处理工艺设备,这些设备在国内都是全新的,需要根据该生产线的要求进行新的设计,重型曲轴热模锻生产线的研制同时也带动了国内设备的制造业水平。
1.2.5 电器与家电工业
早在1996年,我国主要家电产品的产量已进入世界前列,如电冰箱、电视机、洗衣机、电熨斗、电风扇、电饭锅产量已居世界首位。电器与家电设备中的绝大多数零部件的加工,通常是采用冲压工艺分别成形出几个工件后,再采用焊接的方法制成的。巨大的产量迫使高速压力机的滑块每分钟的行程次数已高达4000次。国内目前已研发出1500次/min、125MN的大型高速压力机。例如利用三滚轮旋压机床来生产薄壁不锈钢锅、铝锅等普通锅或高压锅类产品。用这种方法生产出来的零件不但具有良好的内外表面质量,且能节省多达50%的材料。采用变薄旋压的方法可以生产一般家庭、餐馆或医院常用的不锈钢器皿,例如碗、大口杯、桶、过滤器、水壶、量具、调味瓶等。采用普通旋压的方法可以生产铝壶、点心盒、勺、平底锅、真空保温容器等用品。对某些经过冲压或变薄旋压成形后的工件有时还需要进行缩颈旋压成形,例如茶壶、咖啡壶、糖罐、花瓶等。而这些锻压工艺的实施,锻压设备是必不可少的关键的设备。
1.2.6 电力工业
中国对电力的需求量极大,从而迫使我们要加大发电设备的制造步伐。目前传统的发电机、汽轮机、锅炉三大动力设备的成套总产量已达到全球的2/3。如此大的电力市场要求国内装备制造业不断进取、创新。例如中国一重集团有限公司(简称一重)1.50万t、二重1.6万t、上海重型机器厂有限公司(简称上重)1.65万t、中信重工机械股份有限公司(简称洛矿)1.85万t的大型自由锻液压机相继投入使用,满足了电力装备大型自由锻件锻造的迫切要求。