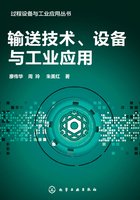
2.4 流体在管内的流动阻力
上节讨论伯努利方程时,方程的各项只有能量损失项还没有述及,所举例题中的hf,其数值多为已知。流体流动时存在阻力并引起能量的消耗,其有关理论和计算将在本节介绍。
流体在管内流动为什么会产生阻力并消耗一部分能量呢?产生阻力的原因有两类:外部的和内部的。粗糙的管壁对流体的阻力、阀门或弯头等管件对流体的阻力、流道截面突然扩大或缩小使流体产生很多旋涡和涡流而消耗能量,以上诸因素都是产生阻力消耗能量的外部原因,而流体本身存在黏性则是产生阻力的内部原因。
2.4.1 牛顿黏性定律与黏度
(1)牛顿黏性定律
流体在圆管内流动时,对管壁有附着作用,壁面黏附一层静止的流体。在流体内部,由于存在着分子间的引力,附在壁上静止的流体层对其相邻的一层流体有一与流动方向相反的拉力,使后者流速减慢。如果把管内流动的流体看成是无数层极薄的一个套一个的圆筒层,那么,距管壁愈近的流体层所受拉力愈大,流速也会愈小;愈靠近管中心的流体层,所受拉力愈小,流速也就愈大。如图2-13所示,任何相邻的两层流体流速都不同,速度较慢的流体层由于分子间引力的作用,对较快速度的流层产生阻碍作用而形成阻力,所有各层流体间的阻力之和即为流体流动时所产生的阻力,称作流体的内摩擦力。流体流动时的内摩擦力是导致产生流动阻力的内部原因,也是根本原因。流体要流动就必须克服内摩擦力,而流体本身的一部分机械能就要转换成热能而被消耗掉。

图2-13 流体在圆管内分层流动示意图
流体流动产生内摩擦力的特性称黏性,故称内摩擦力为黏性力。衡量流体黏性大小的物理量称黏度。
为确定液体黏度的大小及影响因素,可做如下实验。如图2-14所示,在静止的液体中平行放置两块距离很近、面积为A的平板,对上板施一水平恒力F,使上板以恒速u做水平方向的运动。此时,两板间的液体可看成无数个平行的薄层,并以不同的速度运动,附于下板的液层速度为零,附于上板的液层速度为u,其间各液体层的速度自上而下依次减小。当改变不同物理量的数值时,可发现对一定的液体来说,黏性力F与两液层的速度差Δu成正比;与两层间的垂直距离ΔZ成反比,与两层间的接触面积A成正比。即:

图2-14 黏性力的推导
引入一比例系数μ,上式可改写为等式:
黏性力的方向与板运动方向相反。
单位接触面积上的黏性力为剪应力τ,单位为N/m2,则
(2-35)
若取ΔZ为微分距离dZ,Δu相应为du,这样就可适用于垂直方向的速率变化为非直线关系的场合了。流体在圆管内的流动就属于这种情况,此时式(2-35)为:
(2-36)
式中 ——速度梯度,反映了速度在垂直方向的变化率。
μ——比例常数。
实验证明,μ值仅随流体性质的不同而受化,在速度相同的情况下,μ值愈大则黏性力愈大,故可用μ来度量流体的黏性,并称μ为黏性系数或动力黏度,简称黏度。
式(2-36)反映的规律称牛顿黏性定律,服从牛顿黏性定律的流体称牛顿型流体。气体与多数液体均属此类流体。不服从牛顿黏性定律的流体称非牛顿型流体,一些高分子溶液、胶体溶液、浓发酵液和泥浆则属此类流体,此时式(2-36)中的μ不为常数。
(2)流体的黏度
将式(2-36)改写为:
可看出当时,黏度μ在数值上等于单位面积上的黏性力(即剪应力),由此可测出不同流体的μ值。
黏度是流体的物理性质之一,一般由实验测定。温度是影响μ值大小的主要因素,当温度升高时,液体的黏度减小,气体的黏度增大。压力变化时,液体的黏度基本不变,气体的黏度变化也很小,一般工程计算可忽略不计。
黏度的单位可由牛顿黏性定律导出,在国际单位制中,黏度的单位为:
在物理单位制中,黏度的单位为g/(s·cm)=P[泊],而cP[厘泊](1cP=0.01P)目前在一些场合仍在使用,它与法定计量单位的换算关系是:
1Pa·s=1N·s/m2=10P=1000cP
流体的黏性还可以用黏度μ与密度的比值来表示,称运动黏度,以符号ν表示,即:
(2-37)
运动黏度的单位,在SI中为m2/s;在物理单位制中为cm2/s,称斯[托克斯],以St表示,也可用厘斯(cSt)表示。其间的换算关系为:
1St=100cSt=10-4m2/s
混合物的黏度一般用实验方法测定,如缺乏实验条件时,可用经验公式进行估算。对常压气体混合物的黏度可用式(2-38)估算:
(2-38)
式中 μm——常压气体混合物的黏度,Pa·s;
yi——混合气中i组分的摩尔分数;
μi——混合气中i组分的黏度,Pa·s;
Mi——混合气中i组分的分子量。
对分子不缔合的液体混合物的黏度,可用式(2-39)计算:
(2-39)
式中 μm——液体混合物的黏度,Pa·s;
xi——混合液中i组分的摩尔分数;
μi——一混合液中i组分的黏度,Pa·s。
2.4.2 流体的流动类型
(1)雷诺(Reynold)实验
前面谈及流体阻力产生原因时,曾说与流动状态有关。要进一步分析流体的流动状态,需先介绍一个著名的实验,即雷诺实验。
水箱内装有为保持水位恒定的溢流装置,箱底接出一水平玻璃管,管上装有一调节流量的阀门;水箱上方有一盛有色液体的小瓶,瓶与一细管相连并通至水平玻璃管的入口中心处,如图2-15所示。

图2-15 流动类型实验装置
1—水箱;2—水平玻璃管
当开启调节阀控制水流量较小时,有色液体在玻璃管内沿轴线方向形成一条轮廓清晰的细直线流。当调节阀门逐渐开大时,直线流动的有色液体流线受到扰动,呈现波浪式细流。再继续开大阀门使流量变得更大时,波浪式细流受到更大的扰动,进而与水完全混合。
通过观察和分析,可以把流体在管道中的流动状态分为两种类型。
其一是流速不大时,有色液流呈直线状,说明管内流体的各个质点始终沿管轴方向做直线运动,管内流体如一层层同轴圆筒,互不相混,这种流动状态称为层流(滞流)。
其二是流速较大时,有色液体呈混乱状,说明管内流体各个质点速度的大小和方向不断发生变化,彼此碰撞互相混合,完全打破了原来分层流动的秩序,这种流动状态称为湍流(紊流)。
(2)雷诺数
如采用不同的管径和黏度的流体分别做雷诺试验,可发现导致流动状态变化的影响因素,除流速外还有管内径d、流体黏度μ和密度ρ等物理量。奥斯本·雷诺通过研究发现,由以上四个因素组成的复合数群是判断流型的依据。这个数群被称为雷诺数,以Re表示,即:
(2-40)
雷诺数的单位可以从式(2-40)定义导出:
进一步运算,上式中的所有单位可全部消去,也就是说,雷诺数是个无因次数群,即在计算雷诺数时,不论采用哪一种单位制,只要各物理量的单位制是统一的,就都会消去,算出的Re数值也一定相等。
实验证明,当流体在立管中流动时:
Re≤2100时,流体的流动状态为层流。
Re≥4000时,流体的流动状态为湍流。
2100<Re<4000时,流体的流动状态为不稳定的过渡流。过渡流的流体质点运动状态不定,可能是层流,也可能是湍流。
在工程计算中,为方便可靠计,常将雷诺数Re>3000的状态按湍流情况考虑。
【例2-14】 某流体在直管中流动,已知管内径d=50mm,流速为u=2m/s,操作条件下的黏度μ=1×10-3N·s/m2,密度ρ=998kg/m3,求Re值并判断流型。
解
因为Re>3000,所以流体呈湍流状态。
(3)当量直径与水力半径
流体在圆管中的流动,Re数中的d是圆管的直径。若流道截面形状不是圆形的,如套管冷却器中的环隙或通风管的长方形通道,则此时Re数中的d就要用当量直径de来代替,Re的计算公式也就变成:
当量直径是由水力半径的4倍来计算的,即:
de=4R水 (2-41)
水力半径R水是指液体通过流道的自由截面积A(与流动方向垂直)与被液体所浸润的周边长度C之比,即:
(2-42)
对内径为d的圆形通道,其当量直径即为内径,即:
对边长为a和b的矩形截面通道,则:
对外管内径为Di、内管外径为do的环状通道,则:
应予说明,de只是用来代替d作经实验证明误差允许的某些计算的,不可将de随意使用,如不能用de作为通道截面积的计算依据等。
(4)在圆管中两种状态下的流体流速分布
流体在圆管中任一截面不同位置上的质点流速是不同的,靠管中心处流速最大,越靠近管壁其流速愈小,附管壁流体流速为零。从流量和截面积算得的流速以及Re数中的u,都是指管道截面各点的平均流速。流体呈不同流动状态时,流速的分布情况不同。
①层流时的流速分布 流体呈层流状态时,用实验方法可测得在圆管径向上的不同位置的质点流速,并作出曲线,得到一抛物线形状的层流速度曲线,如图2-16(a)所示。此时流体内各质点的平均流速u为导管中心线上的最大流速umax的1/2,即:
u均=0.5umax (2-43)

图2-16 速度分布曲线
②湍流时的流速分布 用同样的实验方法,可作出流体在湍流状态下,管道截面不同位置上各质点的流速分布曲线,如图2-16(b)所示。与层流的速度曲线相比,在导管中心线处湍流速度变化不大,这是因为流体呈湍流状态时,流体质点运动激烈,运动方向杂乱无章,靠中心的质点不再像层流那样总是沿导管中心运动,而是在径向上与处在其他位置的质点混合,导致中心处的速度降低,而接近中心处的速度升高,故曲线变化相对较平缓。根据实验测定,湍流时导管截面处流体平均流速与中心线上流体最大流速的关系为:
u均=0.8umax (2-44)
无论是层流还是湍流,流体在管壁处的速度均等于零。接近管壁处的速度也很小,此处的Re值也会很小。显而易见,流体呈湍流状态时,靠近管壁处仍会有一层流体呈层流状态,这层流体称为层流内层或层流边界层。
以上讨论的速度分布曲线只适用于圆管内的稳定流动,如流道截面不是圆形,或流体流动方向、流速发生变化而未达到稳定,则以上规律不适用。
2.4.3 流体的流动阻力
流体静止时无流动阻力,流体以一定速度流动时才产生阻力。显然,流动阻力的大小与流速有直接关系。实验证明,流动阻力产生的能量损失与动能有如下关系:
(2-45)
式中 ξ——阻力系数。
该式为计算流体流动所产生的流动阻力损失的通式,针对不同情况,求出相应的阻力系数,即求得相应的流动阻力。
前面谈及流体流动时的阻力大小与流体本身的性质、流动状态、壁面情况和管道结构等因素有关,根据以上影响阻力的因素,可以将流动阻力分为直管阻力和局部阻力两种形式。直管阻力是指流体在直管流动中,由于流体内部的摩擦以及流体与管壁的摩擦而引起的阻力;局部阻力是由于流体流经管路中的一些管件和管截面突然扩大或缩小,造成旋涡和涡流所引起的阻力。
2.4.3.1 流体在圆形直管中流动时的流动阻力
由实验和理论计算,均可证明流体在直管中流动时的流动阻力除随动能的增加而增加外,还与直管的长度l成正比,与管内径d成反比。所以,直管中的流动阻力可由式(2-46)计算:
(2-46)
若用压力降表示管路流动阻力,则有:
(2-46a)
式中 λ——摩擦系数,无因次。
λ值的变化随流动类型的不同而遵循不同的规律,同时管壁的粗糙度对λ也有影响。
比较式(2-45)和式(2-46)可知,在直管中流动阻力的摩擦系数λ与通式中的阻力系数ξ有如下关系:
(2-47)
(1)流体呈层流时的摩擦系数
流体呈层流时,摩擦系数与粗糙度无关。这是因为层流的流体,在接近管壁处有一层近乎静止的流体膜,它掩盖了管壁的粗糙表面,此时的λ只是雷诺数Re的函数。通过理论计算和实验证明,λ和Re存在如下关系:
(2-48)
(2)流体呈湍流时的摩擦系数
流体呈湍流时,由于流体质点运动形式复杂,管壁粗糙度对λ值有很大影响,因此λ的计算公式不能从理论上推导出来,只能通过实验结合理论分析,导出经验公式。
①管壁粗糙度 工业上常用管材可分为光滑管和粗糙管两种,如玻璃管、无缝钢管、铅管和塑料管等为光滑管;而钢管、铸铁管和水泥管等为粗糙管。
管壁粗糙程度用绝对粗糙度ε表示,是指直管壁面凸出部分的平均高度。表2-1列出了几种管材的ε值。
表2-1 一些管材的ε值

对于具有相同ε值但直径d小的导管,ε对λ的影响较大;反之,对于直径大的导管,ε对λ的影响较小。因此用两者之比即ε/d来表示粗糙度对摩擦系数的影响更为准确方便,将ε/d称为管壁的相对粗糙度。
②摩擦系数与雷诺数、相对粗糙度的关系曲线 前已述及,λ值的大小与流型和管壁粗糙度有关,为求得λ值,经大量实验和理论分析,作出了λ值与判断流型的Re值和相对粗糙度ε/d三者之间的函数关系曲线,如图2-17所示。

图2-17 摩擦系数与雷诺数、相对粗糙度的函数图
此图称为莫狄(Moody)摩擦系数图
利用图2-17,在算出Re后,根据ε/d 的大小,可查得摩擦系数λ,再由λ、管长l、管径d和动能,按式(2-46)可求得流体在直管段流动的流动阻力。
2.4.3.2 流体在非圆形直管中流动时的流动阻力
流体在非圆形直管中流动时,其阻力计算已由实验证明也可用圆管的式(2-46)计算,只是λ的计算要做如下修正:
①流体呈湍流时,以当量直径de代替阻力计算式中的相对粗糙度和Re数中的d,其产生的误差是工程计算所允许的。
②流体呈层流时,用当量直径求出Re后,按式(2-49)计算λ,即:
(2-49)
式中 A——与截面有关的系数,其值可由表2-2查出。
表2-2 一些非圆形直管的当量直径de与常数A

【例2-15】 计算20℃的水以1m/s的速度通过长100m、ϕ60mm×3.5mm钢管的流动阻力。
解 已知 d=60-3.5×2=53(mm) ρ=1000kg/m3
u=1m/s l=100m
μ=1×10-3Pa·s ε=0.20mm
所以;
在图2-17中右边纵坐标上,找出0.004的一条线与横坐标Re为53000的一条线相交的交点,此点对应的左侧纵坐标摩擦系数λ=0.03,则流动阻力为:
2.4.3.3 局部阻力
流体在管路中流动时,由于流经各种管件、阀门或在流道面积突然扩大或缩小时,会导致流体质点碰撞加剧,或产生旋涡和涡流而引起能量损失,这些产生在局部位置上的流动阻力称为局部阻力。计算局部阻力的方法可采取当量长度法和阻力系数法。
(1)当量长度法
将流体流过局部位置所产生的局部阻力折合成流体通过相同直径、长度为Le的直管所产生的阻力,再按照直管阻力计算公式(2-46)求出局部阻力的方法称为当量长度法。折合直管长度Le称为当量长度。将管道中若干个局部阻力的当量长度加起来,则可用式(2-50)计算出此管道中全部局部阻力产生的流动阻力,即:
(2-50)
将所有局部阻力与直管阻力加起来即为总流动阻力,即:
(2-51)
各种局部阻力的Le值可由表2-3和图2-18查得。
表2-3 各种管件、阀门及流量计等以管径计的当量长度

注:1in=2.54cm。

图2-18 管件与阀门的当量长度共线图
(2)阻力系数法
将流体通过的各局部阻力引起的流动阻力损失表示为动能的倍数ξ,由实验求得ξ值,即可算出压头损失。
(2-52)
式中 ξ——局部阻力系数。常用的局部阻力系数ξ如表2-4和表2-5所示。
表2-4 导管突然扩大与突然缩小时的ξ值

表2-5 管件和阀件的ξ值

【例2-16】 液体由反应罐经长20m、ϕ114mm×4mm的圆管流入储罐,管系中有一个全开的闸阀和两个90°弯头,设流速为1m/s,流体黏度为1cP,密度为1000kg/m3,求总流动阻力。
解 已知 ρ=1000 kg/m3 μ=1×10-3Pa·s
d=114-2×4=106(mm) u=1m/s
所以:
查表得:
由图2-17中查得:
λ=0.031
①用阻力系数法计算 查表2-4、表2-5得:
由反应罐进入管道口处的阻力系数为:
ξ1=0.5 (S2/S1取0.01)
两个90°弯头的阻力系数为:
ξ2=2×0.75=1.5
一个全开闸阀的阻力系数为:
ξ3=0.17
由管出口流入储罐处的阻力系数为:
ξ4=1(S1/S2取0)
由此可以计算出总压头损失为:
②用当量长度法计算 查表2-3得:
由反应罐入导管的当量长度为:
两个标准90°弯头的当量长度为:
一个闸阀(全开)的当量长度为:
由管路进入储罐的当量长度为:
查得ξ4=1代替,则压头损失为:
两种方法的结果略有差异,这是因为表2-3~表2-5和图2-16的数据来源不同。一般来说,采用当量长度法计算管路阻力较方便,而用阻力系数法计算相对较准确。在工程计算中,则需根据哪种方法的数据能得到来决定采用哪种方法来计算。有时也采用两种方法综合计算。
2.4.4 管路计算
管路系统按其结构可分为简单管路和复杂管路。简单管路指由同一管径组成的管路,流体通过简单管路的流速不变。在计算简单管路的流动阻力时,可直接用阻力公式计算。复杂管路则指由不同管径的管子组成的串联管路和由简单管路组成的并联管路或分支管路,这里仅讨论最基本的简单管路的计算。
过程工业中常遇到的管路计算问题有以下三种类型。
(1)已知管径d、管长l和流量Vs,求能量消耗和外加能量
这类问题的计算步骤如下:
①由流量Vs和管径d求出流速。
②算出Re和相对粗糙度,查出摩擦系数λ,由已知的
求出∑hf。
③将∑hf代入伯努利方程求出ws。
(2)已知管径d、管路总长l+∑Le及能量损失∑hf,求流量Vs
这类问题是给出管路和驱动流体的动力来源的情况,求可能达到的最大流量。解决这类问题的关键在于:速度u为所求量,要解出u必须知道d,要求λ需先知道Re,要算Re又需先知道u。为解决这一难题,就要采用试差法。试差法解题的步骤是:在λ和u两个未知量中,任选一个为试差对象,在合理的范围之内假设一个数值,算出另一个未知量,再由此量反算出试差对象,看其计算值与假设值是否相符,如不符,则对试差对象赋一新的假设值,重复以上计算过程,直至相符或误差在允许范围内。
【例2-17】 20℃的水从距地面高15m的水塔经长度为98.1m(含局部阻力当量长度)的ϕ57mm×3.5mm钢管流至地面上的冷却器,冷却器内压力为0.5atm(表压)。求此管路的最大输水量。
解 选水塔与冷却器液面分别为1—1截面和2—2截面,在其间列伯努利方程:
Z1-Z2=15
u1-u2=0
p1=0,p2=0.5atm(表压)=5.07×104Pa(表压)
查得20℃水的密度为ρ=998.2 kg/m3。
由此可计算该管路的阻力损失为:
根据管路阻力当量管长的表达式,有:
据此即可求得管路的流速为:
选λ为试差对象。经验表明,黏度小的流体在大直径管道流动中多数处于湍流状态,且Re值往往在图2-17右方平行线区。由题意,无缝钢管取ε=0.2mm,,再根据图2-17,假设λ=0.028,则:
水在20℃时的黏度:
水在20℃时的密度:
ρ=1000kg/m3
由此可计算出流体的Re值:
由Re=93500和,查图2-17得λ=0.03,与假设值不符,故重新设λ=0.03,则:
由Re=90500和,查图2-17得λ=0.0295,在误差允许范围之内,u=1.81m/s可视为正确值,管道中的流量则为:
(3)已知流量和管路情况,求管径
求这类问题同样不能直接求解,因为要求管径d需先知道λ,要求λ需知道Re,要求Re需知道d,故解决这类问题仍要采用试差法。
【例2-18】 某厂进水干管水压为247kPa(表压),现需安装一水平支管进车间,支管计算长度(含l和∑Le)为1000m,水温25℃,车间要求供水量为50m3/h,水压为147.2kPa(表压),试选水管的规格。
解 选水管为基准水平面,到车间的水管进、出口分别为1—1截面和2—2截面,在其间列伯努利方程:
已知:Z2=0 Z1=0
u1=u2 He=0
p1=247kPa p2=147.2 kPa
ρ=1000 kg/m3
查出:
μ=0.8933×10-3N·s/m2
代入伯努利方程得:
由管路阻力计算式:
已知:
Vs=50m3/h
则管内流速为:
又已知:
l+∑Le=100m
将∑Hf、l+∑Le和u代入阻力计算式得:
λ=628d5
假设:λ=0.02
由上式可得:
查图2-17得λ=0.02,此值与假设值的误差较小,工程计算是允许的,故d=0.126m视为正确。查有关手册,可选用5in规格的水管,其内径为131mm,即可满足流量要求。
2.4.5 管道直径的确定
流体流经的管道截面形状一般是圆形的。若管道的内径为d,其截面积,则可将式(2-19)写成:
即:
(2-53)
输送流体的管道内径,就是根据流量和流速按照式(2-53)计算出来的。式中的流量一般是由生产任务决定的,而流速是由设计人员选定的。若流速选得太大,则管径虽可减小,但流体流过管道的阻力会增加,动力消耗也就会加大,经常性操作费用也会提高。
反之,若流速选得太小,动力消耗引起的操作费用减少了,但为满足流量所需的管径则需增大,管路的一次性基建投资就会提高。因此,在管路设计时要综合考虑操作费用和基建费用这两个相互矛盾的因素,选一个合适的流速值,使两项费用之和为最小,这就是过程最佳化的最简单实例。
图2-19表示了选用不同管径时基建费用、操作费用以及总费用的变化情况,总费用曲线最低点附近(图中阴影部分)是比较经济的,选用适宜的管径d适应在阴影区内。

图2-19 适宜管径的确定阴影区为最低总费用区
上述计算对于较大型的工程设计是完全必要的。对于小型工程设计,由于计算繁琐,耗费时间、精力较大,不一定要这样做。比较方便的是采用经验的适宜流速来计算相应的管径,各种流体的常用流速范围见表2-6。
表2-6 流体在管中流动常用流速范围

【例2-19】 通过某水管的输水量为30m3/h,试选水管的适宜管径。
解 已知:
Vs=30m3/h=0.0083m3/s
从表2-6中选u=1.8m/s,由式(2-53)可得:
从手册查得相近的管子规格为ϕ89mm×4mm,将此管的内径d=89-4×2=81(mm)=0.081(m)再代入式(2-53),可求得管内的实际流速为: