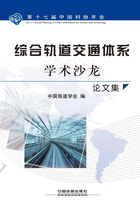
从焊接变形控制浅谈铝合金车体的焊缝质量控制
胡冬生
(广东南车轨道交通车辆有限公司,广东江门 529100)
摘 要:随着我国城镇化持续推进,铝合金轨道交通车辆需求量越来越大,因而其安全和稳定性等方面备受关注。焊接是高铁或动车组铝合金车体制造的基础,焊接质量直接决定了铝合金车体结构的优劣。但焊接过程中的热应力和相变应力等往往导致制品变形,继而诱发错边、未熔合和裂纹等焊缝质量缺陷产生。这就造成了铝合金车体焊接制造过程中存在诸多难题。本文通过分析既定焊接条件下的焊接变形与焊缝质量之间的关系与特点,探究铝合金车体焊接变形控制与焊缝质量控制的可行性。
关键字:机械制造工艺与设备;铝合金车体焊接;焊接变形控制;焊缝质量控制
抵御污染和节约能源再次将公众视野聚焦于交通方式,而轨道交通能够大大改善交通拥堵和降低雾霾,在社会效益和经济成本两方面均具有一定优势[1]。焊接作为金属材料重要的连接方式之一,由于其具有用料少,少机加工或无机加工的净近成形等优点而被广泛地应用于高铁和动车组等装备制造领域[2]。国内现行的铝合金轨道车辆大多采用传统熔化焊焊接技术制造而成。然而,经过传统焊接技术焊接后的铝合金车体结构必定存在不同程度的焊接变形[3]。焊接变形不仅会造成铝合金车体的几何形状和形位公差精度偏差,而且往往诱发焊缝缺陷产生而导致焊缝质量下降。这不但对车体焊接结构的稳定性和使用寿命不利,而且给人们的生命财产埋下安全隐患。铝合金车体焊接质量是高铁和动车组能否安全、平稳运行的关键因素之一。因此开展铝合金车体焊接变形控制和焊缝质量控制研究工作显得尤为迫切,并具有重要意义。
多数焊缝缺陷是由焊接变形衍生而来的,即两者存在着密切联系[4-8]。然而已报道的论述分别集中在铝合金车体焊接变形或者焊缝质量控制两方面[9,10],关于铝合金车体焊接变形与焊缝质量之间的关系与影响论述较少。因此本文通过分析既定焊接条件下的焊接变形与焊缝质量之间的关系与特点,探究铝合金车体焊接变形控制与焊缝质量控制的可行性,以此为铝合金车体焊接生产提供借鉴和参考。
1 焊接变形与焊缝质量的关系
铝合金焊接变形不仅导致制品形状结构的改变,同时也会诱发焊缝热裂纹等缺欠产生[5,6,11]。图1为焊接厚度方向的错边变形和焊缝欠缺,可以看到焊接变形是焊缝产生欠缺原因的重要因素之一。厚度方向的收缩导致焊道间隙增大而使熔融态金属不足,并且焊接电弧未能将向上翘曲的坡口熔合共同造成图1现象。
图2为铝合金车体地板型材插对接局部变形,该变形出现在机器人自动焊中最后一道焊缝施焊过程。从中可以看到收缩变形已经造成了组对间隙增大,原本定位作用的段焊缝被完全拉裂。这是多道拼接焊缝横向收缩应力叠加所造成的。焊接变形不但造成焊缝质量遭到破坏,而且导致返工、制造周期延长和成本增加。由于组合焊道状况改变,导致变化后的焊道与原来设置的模板不匹配而不能识别,这将导致焊接机器人自动停车。为排除异常必须将段焊缝完全清除,否则会造成该部位存在根部未焊透或未熔合的质量安全隐患。焊接变形会引起焊道金属需求量增加,而在行的自动焊焊接参数未来得及修正,这最终导致焊缝易出现未填满。焊接变形所造成的薄板翘曲会导致坡口边缘存在咬边等缺陷。
作者简介:胡冬生,男,助理工程师,主要从事车体焊接工作。

图1 焊接变形与焊缝欠缺的关系

图2 铝合金车体地板型材插对接局部变形
在瞬时局部高温的条件下,熔化焊焊接过程中的焊缝及其周边母材始终存在着应力和应变[13]。并且焊接热源一直处于移动当中,焊缝及其附近金属的应力-应变场梯度变化剧烈。焊缝及母材金属的膨胀或收缩存在不同步和不平衡,局部应变累积或多处应变叠加而最终导致焊接变形[3,10]。但焊接变形往往存在翘曲和局部坡口直线度偏差而导致错边,未熔合和裂纹等焊缝缺欠出现[3,5,6,10-12]。因此焊接变形和焊缝质量应该同时得到控制和改善。
2 焊缝质量控制方法
焊缝缺欠往往随着焊接变形而出现,甚至在焊接变形控制的过程中产生[3,5,6,14],因此从焊接变形与焊缝欠缺的关联中入手进行焊缝质量控制是可行的和必要的。从焊接变形控制角度加强焊缝质量控制的方法总体上有焊缝位置安排、接头形式设计等设计角度,焊接顺序等焊接工艺角度和焊后矫正变形避免引入新的焊缝缺陷角度等方面进行焊接质量控制。
2.1 恰当的焊缝和接头设计
在焊缝位置安排方面,尽量将焊缝中心线与焊接构件结构截面中性轴重合或者对称分布。这利于降低焊接变形和焊接过程的膨胀、收缩应力或残余应力与重力的叠加程度,达到降低焊接过程中焊缝的裂纹倾向性。焊道坡口角度和焊接接头组合形式对焊接变形和焊缝质量控制具有一定影响。王大志[15]在薄板与厚板T型角接变形控制与焊缝质量控制的研究表明:大长焊缝焊接宜采用单边V型、K型或双边U型坡口,并且坡口角度尽量小以减少焊缝截面积;焊接顺序上采用分层分段对称跳焊和分散填焊,分层焊接时注意将接头错开,避免缺陷过度集中;同时依据材料厚度确定焊接电学参数和焊接速度范围,能够在焊透的前提下,获得无裂纹和表面大气孔的焊缝。
2.2 适宜的焊接装备工装选用
焊接变形和焊缝开裂等焊缝缺欠绝大多数是焊接热量输入过大所造成的,因此选用低热量输入的焊接设备能够从源头上遏制焊接变形和改善焊缝质量。近来发展的CMT焊接、搅拌摩擦焊接、超声波焊接和激光-MIG焊等复合焊接设备逐步在铝合金或铝合金车体焊接得到应用。通过翻转、移动来改变焊接位置或取得良好的焊接可达性也是一种减少焊接变形与改善焊缝质量的有效方式。通过柔性工装可以将地板、车顶和侧墙等铝合金车体大部件在焊接过程得到灵活翻转。在夹紧状态下翻转,可以有效避免应力松弛而产生焊接变形和焊缝局部开裂,同时确保良好的二次焊接条件。
2.3 合理的焊接工艺
在既定的焊接材料、型材结构和焊接设备条件下,铝合金车体焊接变形控制和焊缝质量的优劣严重依赖于焊接工艺设计的合理性,因此铝合金焊接工艺设计意义重大。通过外侧分段退焊,内壁分段跳焊,将每段焊缝控制在400mm以下达到了避免焊缝收缩拉应力叠加而减少焊缝区域变形;优化焊接电流和焊接速度的匹配性工艺试验,在熔透性、熔合性良好的前提下尽量提高焊接速度,这些措施同时达到了焊接变形控制和焊缝质量控制[16]。加强焊接型材组对和装配精度,通过减少接头的贴合间隙,限制焊接熔融金属的填充量也是一种有效途径。通过柔性固定工装,千斤顶和手扳葫芦压紧、顶紧和下拉,同时配合长短F卡具能够有效减少铝合金车体型材对接、搭接和角接的横向、厚度方向的间隙,从而减少调修幅度,最终达到改善焊缝质量的目标[16-19]。然而,合理的车体结构设计、适宜的母材和焊丝匹配和焊前准备工序也对焊缝质量造成不良影响,优质的焊缝需要焊接“六要素”的完美匹配[20]。针对大厚度铝合金焊接可以采用低温预热,正反两面焊接减少未焊透、未熔合及变形产生几率[6,16]。而厚度差异大的车体结构焊接时,往往在焊枪角度方面进行调整,一般要求焊枪朝向厚板侧。焊接工艺设计需要根据待焊接部件结构、尺寸和焊缝尺寸设计要求,同时结合现有的工装卡具设备,并根据焊工技能熟练程度进行确定。即焊接工艺设计需要“因地制宜”,充分利用好已有条件,积极创造有利条件,最终达到良好的焊接变形和焊缝质量控制。
2.4 合适的焊后矫形
当上述措施未能将焊接变形控制在设计要求内,即要采用焊后调修。常用的调修方式有火焰加热调修法以及最近出现的随焊碾压和冲击碾压法、随焊电磁冲击法等等[15,21]。然而火焰调修的加热温度需要严格控制避免过高而造成焊缝开裂或组织过烧,并且施加压力不能过大,避免压裂等等。
2.5 严密的焊缝质量检验
焊缝质量检验能够及早发现焊缝缺欠,并利于及时进行修复,最终达到杜绝焊缝质量安全隐患,因此焊缝检验非常必要,是焊缝质量控制有效措施之一。常见的铝合金车体焊缝无损检验方法有外观检测、渗透检测、射线探伤和相对较新的超声波检测,此外还有破坏性的拉伸、弯曲等力学性能检测方法[22]。在生产中,往往采用施焊者的自我检查,班组相互检查,质量安全技术人员的周检或抽检多重焊缝质量检查,以确保车辆安全。
3 结论
焊缝质量控制系铝合金车体焊接制造重要组成部分,但目前对铝合金车体焊接变形与焊缝质量控制的论述较少[3],而国内不断增加的动车组迫切需要精确、有效的理论指导。通过上述分析可以开展以下工作:
(1)根据铝合金材料属性与车体功能结构设计适宜的接头形式与数量的焊缝,以减少应力集中的源头来控制焊接变形,尽可能减少焊缝宽度与深度的比值,限制焊缝裂纹等缺陷产生;
(2)通过适宜的焊接设备工装和焊接工艺设计来限制焊接变形幅度,并改善焊缝质量;
(3)用恰当调修工艺控制焊接变形和避免焊缝质量遭到破坏;
(4)通过严密的焊缝检验程序筛查焊接变形及焊缝缺欠,杜绝不合格品流入下一道工序。
参考文献
[1]Maria Carmen Falvoa,Regina Lamedicaa,Richard Bartoni,et al.Energy management in metro-transit systems:An innovative proposal toward an integrated and sustainable urban mobility system including plug-in electric vehicles[J].Electric Power Systems Research,2011,81(12):2127-2138.
[2]王元良,陈辉.高速列车铝合金车体的焊接技术[M].成都:西南交通大学,2012:6-8.
[3]胡冬生,尹志春,杨明睿,等.铝合金车体焊接变形及其控制方法初探[J].广东科技,2014,23(20):161-164.
[4]Cheng C M.Butt-welding residual stress of heat treatable aluminum alloys[J].Journal of Material Science Technology,2007,23(2):217-222.
[5]张建勋,巩水利,李晓延,等.轻金属焊接学术前沿及其研究领域[J].Welding&Jioning,2008(12):5-10.
[6]韩晓辉.高速列车铝合金车体焊接缺陷分析及工艺研究[J].焊接技术,2009,38(3):31-35.
[7]Xu Guoxiang,Wu Chuangsong,Ma Xuezhou,et al.Numerical analysis of welding residual stress and distortion in laser+GMAW hybrid welding of aluminum alloy T-joint[J].Acta Metallurgica Sinica:English Letters,2013,26(3):352-360.
[8]汪洪峰,左敦稳,戴晟,等.7022铝合金FSJ拼连板材残余应力和变形分析[J].材料工程,2013(7):79-84.
[9]薛健,刘囝.我国高速列车铝合金车体焊接变形方法研究现状[J].热加工工艺,2012,41(17):188-190.
[10]元恒新.焊接材料及工艺对铝合金焊接性能的影响[D].重庆:重庆大学,2006:3-4.
[11]宫博.铝及铝合金中常见的焊接裂纹及其防止措施[J].轻金属,2012(9):66-70.
[12]李亚江.焊接缺陷分析与对策[M].北京:化学工业出版社,2011:116-154.
[13]吴传松,陆皓,魏艳红.焊接多物理场耦合数值模拟的研究进展与发展动向[J].焊接,2012(1):10-22.
[14]王炎金,丁国华.铝合金车体制造关键技术研究[J].焊接,2007(7):12-17.
[15]王大志.大型方箱焊接构件保证焊缝质量控制焊接变形的工艺分析[J].焊接技术,1991(3):29-32.
[16]王润,田新莉,唐衡郴,等.动车组头车铝合金车体焊接质量控制[J].焊接技术,2013,42(12):71-73.
[17]李会,王天,候振国,等.铝合金薄壁型材搭接角焊缝焊接缺陷及变形研究[J].焊接技术,2013,42(3):45-47.
[18]马治国.200EMU铝合金车体侧墙焊接变形的控制[J].四机科技,2007(2):1-4.
[19]胡文浩,刘春宁,王广英.高速动车组铝合金车体长大型材关键焊接技术研究[J].焊接技术,2013,42(5):31-36.
[20]李名望.铝合金车体焊接裂纹修复工艺[J].焊接技术,2011,40(7):57-59.
[21]李刚卿,邢立伟,郑浩敏,等.高速列车制造焊接技术应用展望[J].焊接,2011(5):14-19.
[22]刘志平,刘春宁,王立夫.高速列车铝合金车体的焊缝检验[J].焊接技术,2008,37(1):49-52.