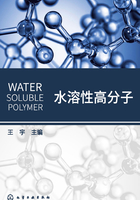
第3章 丙烯酰胺及其共聚物
中文名:丙烯酰胺
英文名:acrylamide,AM
中文名:聚丙烯酰胺
英文名:poly-acrylamide
3.1 丙烯酰胺概述
丙烯酰胺(AM)是一种非常重要的有机化工原料,在工业生产方面的用途非常广泛。在工业方面,丙烯酰胺的应用主要是生产聚丙烯酰胺,或者是其衍生物的共聚物或均聚物。聚丙烯酰胺能够用作增强剂、增稠剂等,同时在石油开采、造纸、水处理、纺织印染等和经济相关的领域中也有非常广泛的应用。
聚丙烯酰胺是一类重要的水溶性高分子聚合物,源于分子结构上的特性,聚丙烯酰胺具有特殊的物理化学性质,易通过接枝或交联得到支链或网状结构的多种改性物,广泛应用于国民经济的各个行业,享有“百业助剂”之称。随着我国工业化迅速发展,聚丙烯酰胺应用范围不断扩大,需求量也不断增加。
3.2 丙烯酰胺产品理化性质
丙烯酰胺(AM)是一种水溶性单体,纯品为白色结晶固体,熔点84~86℃,易溶于水、甲醇、乙醇、丙酮,稍溶于乙酸乙酯、氯仿,微溶于苯,在酸碱环境中可水解成丙烯酸。
丙烯酰胺单体结构中的不对称性CC使其在适宜的条件下很容易发生聚合反应,同时分子内活泼的—CONH2结构又可以发生水解、羟甲基化、Mannich加成、磺甲基化、霍夫曼降解及交联等反应而生成不同的衍生物。
丙烯酰胺及其主要衍生物具有中等毒性。丙烯酰胺与N-羟甲基丙烯酰胺为神经毒剂。丙烯酰胺蒸气吸入或经皮肤吸收以及消化道吸收可引起中毒,在体内有蓄积作用,主要危害中枢神经系统,对眼、皮肤和黏膜有强烈刺激作用,空气中的容许浓度为0.3mg/m3。丙烯酰胺急性中毒十分罕见,密切大量接触可出现亚急性中毒,中毒者表现为嗜睡、小脑功能障碍以及感觉运动型多发性周围神经病。长期低浓度接触可引起慢性中毒,中毒者出现头痛、头晕、疲劳、嗜睡、手指刺痛、麻木感,还可伴有两手掌发红、脱屑,手掌、足心多汗,进一步发展可出现四肢无力、肌肉疼痛以及小脑功能障碍等。
丙烯酰胺慢性毒性作用最引人关注的是它的致癌性。丙烯酰胺具有致突变作用,可引起哺乳动物体细胞和生殖细胞的基因突变和染色体异常。动物实验研究发现,丙烯酰胺可致大鼠多种器官肿瘤,如乳腺、甲状腺、睾丸、肾上腺、中枢神经、口腔、子宫、脑下垂体肿瘤等。但目前还没有充足的人群流行病学证据表明,食物摄入丙烯酰胺与人类某种肿瘤的发生有明显相关性。国际癌症研究机构(IARC)对其致癌性进行了评价,将丙烯酰胺列为2类致癌物(2A),即人类可能致癌物。其主要依据为,丙烯酰胺在动物和人体均可代谢转化为致癌活性代谢产物环氧丙酰胺。各种丙烯酰胺类物质毒性数据见表3-1。
表3-1 各种丙烯酰胺类物质毒性数据

在工业使用上,每天可允许的丙烯酰胺最大暴露量为0.05mg/kg体重,约合临界值0.3g/m3,如果皮肤接触还需低于此值。一般居民每天可允许的最大暴露量不超过0.0005mg/kg体重。
丙烯酰胺侵入途径是经皮肤、黏膜吸收,呼吸道吸入、摄入,与眼和皮肤接触,侵害部位是中枢神经系统、周围神经皮肤和眼。
丙烯酰胺对人体健康的影响,取决于接触丙烯酰胺的浓度、剂量、时间的长短、防护措施的有无及其效果。美国环境保护局根据实验资料提出,丙烯酰胺在很低浓度时是一种明显的神经性毒物。对人来说,神经中毒的主要症候与末梢神经受累有关系,在很大程度上与中枢神经系统受累有关系。据报道,其他最常见的症候和症状是在皮肤、手和脚出现病症。初次暴露后起病迟缓,作用是可逆的,尽管未必总是这样。
丙烯酰胺中毒在临床上常分为亚急性和慢性两种类型。
急救措施:如触及眼和皮肤,立即用大量水冲洗;如有人大量吸入,立即移离现场至新鲜空气处,必要时,进行人工呼吸;如被吞服,必须辅以大量水,诱吐,洗胃;但不省人事者,不宜进行催吐,应立即送医院救治。
防护措施:生产过程中加强预防措施,设备应密闭,加强厂房通风,控制浓度在容许限度之下。操作人员应穿防护工作服,以防止皮肤反复或长时间接触;戴防护眼镜,以防止眼睛的接触。工作服如被溅及或受污染,应每天更换。可渗透的工作服如被弄湿或受到污染,立即脱去。生产现场应装备安全信号指示器。
丙烯酰胺的安全使用,最重要的在于注意防护直接接触,特别是在倒空包装桶及包装袋时特别注意。卸货处须装设通风设施,使用防毒面具及防护衣,以保护工作人员。实验室内使用者须戴氯丁橡胶手套以及在通风橱内操作。固体丙烯酰胺加热或氧化剂接触能产生猛烈聚合而爆炸。
固体丙烯酰胺通常使用带有塑料内衬的纸袋包装,储存处须保持清洁、干燥。温度一般保持在10~25℃,不能超过50℃。
50%丙烯酰胺水溶液须在15.5~38℃储存,温度不得超过50℃。超过50℃,聚合风险加大,但温度也不能过低,50%丙烯酰胺在14.5℃以下就会从溶液中结晶析出。单体中可以加入25~30mg/kg铜离子作为阻聚剂,也可以加入20~200mg/kg对羟基苯甲醚作阻聚剂。氧气也是丙烯酰胺的阻聚剂,在罐区储存时,可以定期通入空气避免聚合发生。
3.3 丙烯酰胺国内外发展史
3.3.1 丙烯腈原料与98%硫酸水解反应后用氨中和制得丙烯酰胺
丙烯酰胺生产技术最早于1954年由美国氰胺公司首先开发。当时采用硫酸水解法生产丙烯酰胺。即在90~100℃条件下,丙烯腈(AN)与98%硫酸进行水解反应,生成硫酸丙烯酰胺,然后用氨气中和反应产物,在40~50℃析出硫酸铵,分离硫酸铵后,将反应物冷却形成丙烯酰胺结晶,经分离、干燥得到结晶单体。
3.3.2 丙烯腈原料与水以骨架铜为催化剂转化合成丙烯酰胺
20世纪70年代,美国陶氏公司和日本三井东亚化学株式会社相继开发出以骨架铜为催化剂的AN催化水合AM工艺,俗称催化水合法。根据工艺过程的不同又可以分为固定床催化水合法和悬浮床催化水合法。
铜催化水合法采用丙烯腈在铜基催化剂存在下经水合反应来制备丙烯酰胺,所述方法包括使反应体系中合成在一个分子中具有活性亚甲基基团和酸性基团的化合物或其盐,然后使该含有丙烯酰胺的溶液与弱碱性或中度碱性的阴离子交换树脂接触。在上述水合反应中,杂质的生成得到抑制,而催化剂活性却不受任何影响,所得丙烯酰胺可用来制造分子量高并且水溶性好的絮凝剂。
美国陶氏化学公司采用Cu-Cr催化剂,固定床催化水合法。该法首先采用氮气吹出7%丙烯腈溶液中的氧气,而后进入三级反应系统,丙烯腈催化水合法合成丙烯酰胺,经过滤、真空蒸发、活性炭、离子交换处理,获得成品。该法具有催化剂易活化再生的特点,丙烯腈的转化率为99.8%~99.9%,系统全封闭。
日本三井东亚公司和三菱化学公司采用Cu-Ni催化剂,悬浮床催化水合法。该法以去离子水与丙烯腈以2∶1的质量比,在悬浮的 Raney Cu催化剂存在下于120℃的单级上流反应器中反应,停留时间25h,获得含22%丙烯酰胺和17%丙烯腈的水溶液。经真空蒸馏回收丙烯腈,并把丙烯酰胺浓缩到30%。将此溶液用活性炭处理除去低聚物和共聚物后,再经离子交换处理,最后浓缩至50%的产品。该催化法可连续再生,连续补充,反应稳定,但工艺流程长、设备结构复杂。
1995年我国大庆油田化学助剂厂引进日本三菱化学株式会社的悬浮床连续化工业技术,建成生产能力5万吨/年的丙烯酰胺装置。其产品质量和规模可以满足生产较高分子量聚丙烯酰胺的要求。
3.3.3 原料丙烯腈与水以微生物腈水合酶为催化剂制得丙烯酰胺
1985年日本日东化学公司采用生化法实现丙烯酰胺工业化生产,并建成生产4000t/a丙烯酰胺装置,此后,日本京都大学发现Pseudomonas Chlarordphis B23和Rhodococcus Rhodochrous J-1菌种,对现有装置又进行大规模改造,于1991年其生产能力扩大到15000t/年。
我国上海生物农药化工研究中心由国家工程院院士沈寅初主持“七五”、“八五”国家科技攻关项目“微生物法生产丙烯酰胺”,建立了我国第一套利用生物技术生产大宗化工原料的工业化装置,开创了生物催化在化工行业中应用的先河,该技术获得上海市科技进步一等奖、“八五”攻关优秀成果A奖、国家科技进步二等奖和杜邦科技创新奖;2002年,微生物法生产丙烯酰胺万吨级工业化技术开发获得昊华奖。
沈寅初院士20世纪80年代末率领研究中心团队在山东泰山视察生物植被时发现一株植物,带回到上海生物农药化工研究中心成功提取菌株并发现了腈水合酶的诺卡氏菌,也筛选出菌株总酶活力达到2000多万的国际水平。1993年微生物法丙烯酰胺水溶液技术转让到浙江桐庐农药厂,年产500t。1994年上海农药化工研究中心将该项技术转让到江苏南天集团股份有限公司如皋化肥厂和江西农科化工有限公司,装置年产仅仅为500t的水溶液。江西农科化工1995年底成功地将产能在原有的基础上增到1000t丙烯酰胺晶体,1998年与江苏南天集团股份有限公司合作并成功控股,产能逐步增长到100000t。
俄罗斯也曾开发出AN催化法生产AM的工业方法,并建成24000t/a的工业装置,该工艺使用Rhodococcus-SPM8菌种,该菌种含有高活性和高热稳定性的腈水合酶。
随后,德固萨公司、SNF公司等也推出了生化法生产丙烯酰胺的技术,并向外输出技术产品。德固萨公司在俄罗斯Perm拥有年产数千吨的生物氧化法生产丙烯酰胺装置,产品用于水处理。法国SNF FLoerger公司是世界领先的聚丙烯酰胺生产商,在印度扩增水溶液聚丙烯酰胺能力,在法国、美国和中国的新建装置于2002年投产。该公司采用的生物催化技术在中国泰兴的20000t丙烯酰胺装置于2003年投产,在美国Andrezicux的两套聚丙烯酰胺生产线已生产。SNF公司也在中国扩增聚丙烯酰胺产能。泰兴两条聚丙烯酰胺粉末新生产线项目20000t/a已于2003年年底完成,从而使聚丙烯酰胺能力翻番,达到40000t/a。
日本三井化学公司参股50%的韩国Yongsam三井化学公司(YMC)在韩国釜山建设的5000t/a生化法丙烯酰胺(AM)生产装置于2003年投入转运。YMC公司的聚丙烯酰胺总产量将增至12000t/a。三井化学公司的新装置投产后,在三个国家的聚丙烯酰胺总产量将增至55000t/a。新装置采用的生化法由三井化学公司用基因重组技术开发的一种酶催化剂生产工艺,与其他方法相比,新方法简单,投资费用低,具有极强的竞争力。
亚洲丙烯酰胺需求量为200000t。亚洲领先的丙烯酰胺生产商是Dia-Nitrix公司,该公司于2001年由三菱化学公司和三菱合成纤维公司合并而成,生产丙烯酰胺能力为65000t/a。2001年生产聚丙烯酰胺达到480000t。
3.4 丙烯酰胺制造方法
丙烯酰胺的常规化学生产法有硫酸水合法和铜催化水合法两种,前者工艺过程复杂,后者因反应中会发生加成反应而还有少量加成反应物。现在用微生物法腈水合酶菌催化丙烯腈生产丙烯酰胺,其产品纯度高,选择性好。目前世界上聚丙烯酰胺都是由丙烯腈出发制取的,其过程包括3个步骤;合成丙烯腈,合成丙烯酰胺,聚丙烯酰胺单体聚合。
3.4.1 化学法——硫酸水合法
美国氰胺公司最早采用等摩尔比的丙烯腈和水,在有硫酸并于80~100℃的条件下进行水合,先生成丙烯酰胺硫酸盐,然后再与氨(或烧碱、生石灰)中和,结晶分离出丙烯酰胺产品和副产品硫酸铵。该法优点是易制得结晶单体。
硫酸法是间歇操作,流程复杂,过程中耗用酸、碱,腐蚀设备,生产成本高,且产品纯度低,容易产生副反应,主要生成β-羟基丙烯腈,在反应过程中进一步产生β-氰乙基丙烯酸酯,后者是一种低分子量的水不溶物,它的存在影响了丙烯酰胺的性能。
3.4.2 化学法——骨架铜催化水合法
美、日两国先后开发了利用骨架铜作催化剂,丙烯腈与水直接反应生成丙烯酰胺的工艺,美国陶氏化学公司和日本三井东亚化学公司率先实现了工业化生产。
催化水合法与硫酸水合法相比,其产品纯度高,基本无三废,易实现工业化,2010年以前世界上主要采用催化水合法生成丙烯酰胺。采用的骨架铜催化剂有Cu-Cr合金、Cu-Ni合金及Cu-Al-Zn合金等。反应器采用悬浮床和固定床。以美国陶氏化学公司为代表的固定床连续催化工艺,采用Cu-Cr催化剂,我国现用Cu-Al-Zn骨架铜催化剂固定床连贯催化工艺。
从20世纪60年代起,含铜催化剂的研制开发曾经十分活跃,至今仍有不少新的制备方法及应用,据文献报道,已被开发的常用类型有如下几种。
①还原铜,用氢气、一氧化碳、肼、碱或碱土金属的硼酸酐或甲醛等作为还原剂,还原氧化铜、氢氧化铜或铜盐而得。
②雷尼铜,用雷尼合金(含铜、铝、锌或锰的合金)浸提而得。
③热解金属铜,由甲酸铜或草酸铜等有机铜经高温热解而得,它们往往含有铬、钼或其他载体。
南非萨索尔公司和催化蒸馏技术公司(CDTech)联合开发了从丙烯腈生产丙烯酰胺的一步法工艺,年生产5000t的工业化装置已于2002年投产。化学上虽涉及丙烯腈和氧化铜催化剂作用下的水解反应,但应采用催化蒸馏方法进行,可产生35%~50%丙烯酰胺的水溶液,而无副产品。相对比较,标准化的固定床工艺采用三个反应器段,生成约20%丙烯酰胺的溶液和4%未反应丙烯腈,需净化、浓缩成50%丙烯酰胺才能送往市场,同时生成不需要的聚丙烯酰胺和丙烯酸。在CDTech工艺中,将丙烯腈和水加入催化蒸馏塔器顶部,并下降到反应区(位于塔中部包覆催化剂的专用填料);硫酸泵送至塔器底部以控制pH值和抑制在重沸器中的聚合;由于停留时间短,可避免生成副产品。较重的丙烯酰胺一旦生产就下降,并从塔底移去;未反应的物料在塔器上部循环直至转化。新工艺的投资费用为固定床装置的一半左右,操作费用也低大约25%。
3.4.3 生物法——腈水合酶催化转化法
生化法即生物酶催化水合法,采用生物酶作催化剂,应用细胞固定技术,使丙烯腈水溶液通过含固定酶的生物反应器生产丙烯酰胺,生物酶催化剂是继骨架铜氧化剂后的第三代技术,具有高选择性、高清洁性和高收率的特点,并且丙烯腈反应完全,无副产品,反应条件温和,能耗低,三废少等。
生化法制取丙烯酰胺,将丙烯腈、原料水和固定化生物氧化剂调配成水合溶液,催化反应分离出废催化剂就可得到丙烯酰胺产品。其特点是在常温常压下反应,设备简单,操作安全;单程转化率极高,无须分离回收未反应的丙烯腈;酶的特异性能使选择性极高,无副反应。采用J-1菌种时,反应温度为5~15℃,pH值为7~8,反应区丙烯腈浓度为1%~2%。丙烯腈转化率为99.99%,丙烯酰胺选择性为99.98%,反应器出口丙烯酰胺浓度接近50%;失活的酶催化剂排出系统外。
3.5 丙烯酰胺市场前景
丙烯酰胺(AM)是一种用途广泛的重要精细有机化工原料,以它为单体合成的聚丙烯酰胺作为驱油剂、助滤剂、增稠剂、絮凝剂等,广泛应用于石油、造纸、采矿、洗煤、冶金、水处理、制糖、环保、建材、涂料、食品等领域。在三次采油方面,注入1t聚丙烯酰胺可驱出约150t原油;在造纸上,采用聚丙烯酰胺每吨纸可节约20元。我国是世界上的贫水国家之一。随着水资源的日益紧张以及环境污染的日益严重,水处理问题越来越受到人们的重视。在美国、西欧丙烯酰胺应用于水处理的比例高达50%以上,而我国仅为2%,其发展前景十分广阔。目前,全世界每年通过NHase生产的丙烯酰胺超过30万吨。更重要的是,它环境污染小、成本低,符合绿色化工的发展理念,有着其他化学方法无法替代的优越性,从而促进了精细化工产品的研制和开发。
截至2016年国内规模化生产丙烯酰胺/聚丙烯酰胺企业达到22家,据不完全统计产能已经达到96万吨/年,其中油田用聚丙烯酰胺29.3万吨/年,占聚丙烯酰胺总产能的30.5%;水处理用聚丙烯酰胺13.2万吨/年,占聚丙烯酰胺总产能的13.8%;造纸用聚丙烯酰胺5.1万吨/年,占聚丙烯酰胺总产能的5.3%;采矿用聚丙烯酰胺2.1万吨/年,占聚丙烯酰胺总产能的4.1%;其他用聚丙烯酰胺2.1万吨/年,占聚丙烯酰胺总产能的2.2%;出口聚丙烯酰胺2.9万吨/年,占聚丙烯酰胺总产能的3%;阴离子聚合物用聚丙烯酰胺41.9万吨/年,占聚丙烯酰胺总产能的43.7%;阳离子聚合物用聚丙烯酰胺11.4万吨/年,占聚丙烯酰胺产能的11.8%;非离子聚合物用丙烯酰胺2.1万吨/年,占聚丙烯酰胺总产能的4.2%;两性离子用聚丙烯酰胺0.3万吨/年,占聚丙烯酰胺总产能的0.3%。
国内20世纪60~70年代引入化学法生产丙烯酰胺,到90年代中期转变为微生物法丙烯酰胺,80年代总产能约5万吨,近20多年随着微生物法丙烯酰胺技术的革新和进步,年产能发展到96万吨,每年均10%的增长率,目前化学法丙烯酰胺仅有少数的2~3家单位。具体详见表3-2。
表3-2 2014年国内丙烯酰胺及其聚合物生产量 单位:kt

3.6 聚丙烯酰胺概述
聚丙烯酰胺(poly-acrylamide)是丙烯酰胺的均聚物或与其他单体的共聚物,以及这些均聚物、共聚物衍生物的统称。以往工业上把丙烯酰胺含量高于50%的AM单体聚合物泛称为聚丙烯酰胺,现在很多含有少量丙烯酰胺组分的共聚物,但用在类似行业的产品也笼统称为聚丙烯酰胺。
聚丙烯酰胺是一种线型水溶性高分子,分子量可以达到千万数量级,是水溶性高分子化合物中应用最广泛的品种之一。根据其水溶液的不同特性,广泛应用于水处理、造纸、石油、煤炭、矿冶、地质、轻纺、建筑等工业部门。
聚丙烯酰胺工业从20世纪50年代开始发展[1~3],到20世纪80年代初,美国陶氏化学已经有万吨级规模的生产线。随着产品用途的日趋广泛,聚丙烯酰胺品种和产量也逐步增加,在美国、日本、欧洲都有大规模生产,到21世纪初,全球聚丙烯酰胺产品销量已达到70万吨。中国近年来聚丙烯酰胺行业发展很快,产能不断扩大,品种逐渐增多。到2015年,全国规模化的聚丙烯酰胺产能已经超过30万吨[4]。
3.7 聚丙烯酰胺产品理化性质
3.7.1 固体聚丙烯酰胺的物理性质
聚丙烯酰胺很难单独作为材料使用,固体聚丙烯酰胺的应用主要取决于其在水溶液中的行为,因而对固体聚丙烯酰胺的物理性质研究较少。此外,固体聚丙烯酰胺吸水能力很强,容易从空气中吸收水分,干燥比较困难,且聚丙烯酰胺在深度干燥时也容易发生交联等化学反应,导致固体聚丙烯酰胺性质发生变化。聚丙烯酰胺应该是透明玻璃状坚硬、易碎的固体,用冷冻干燥方法得到的固体聚合物则是白色棉絮状非结晶固体。而市售聚丙烯酰胺由于其干燥研磨的加工工艺呈现为白色粉粒状态。通常含水5%~12%。
由于聚丙烯酰胺分子链上含有酰胺基,有些还有离子基团,故其显著特点是亲水性高,比其他大多数水溶性高分子的亲水性高得多。它易吸收水分和保留水分,使其在干燥时具有强烈的水分保留性,又具有强烈的吸水性,且吸水率随衍生物的离子性增加而增加。
聚丙烯酰胺能以各种百分比溶于水,但当浓度高于70%时更宜认为是水溶于聚合物。分子量似乎不影响水的溶解性,但是高分子量聚合物在浓度超过10%时会形成凝胶状结构。据悉这是由于分子间形成氢键。聚丙烯酰胺不溶于大多数有机溶液,如甲醇、乙醇、丙酮、乙醚、脂肪烃和芳香烃。有少数极性有机溶剂除外,如乙酸、丙烯酸、氯乙酸、乙二醇、甘油、熔融尿素和甲酰胺。但这些有机溶剂的溶解性有限,往往需要加热,无多大应用价值。
聚丙烯酰胺可以通过用甲醇或丙酮从水溶液沉析出来的方法纯化。干的聚丙烯酰胺可用含20%~30%水的甲醇或丙酮洗涤去掉杂质。
水是聚丙烯酰胺的最好溶剂。使用过程中应重视聚丙烯酰胺的溶解,与产品形式、分子结构、溶解方法、搅拌、温度及pH值等有关。粉状产品若能防止结团比胶体产品易溶,乳液产品溶解性较好,市场上也能够看到溶解时间在1~2min的速溶型分散液产品以及乳液产品。提高溶液温度能促进溶解,但一般不宜超过50℃,以防止降解及产生其他反应。粉粒产品在制造时适量添加一些无机盐(如硫酸钠)、尿素和表面活性剂等,能减弱聚丙烯酰胺分子间的缔合,防止结团,有助于溶解。
聚丙烯酰胺与其他聚电解质相比,具有较高的热稳定性。但在干燥加热到100℃以上时,由于形成亚胺常引起交联。高温下长时间加热,则会引起高分子降解。在无氧情况下加热聚合物到210℃时,因脱水而轻微失重。继续加热到210~300℃时引起酰胺基分解生成氨气和水。335℃时开始进入二级分解区,约370℃时分解速率达到最大值。产生二级分解区是由于聚合物主链及酰胺分解,生成腈。温度升至500℃时形成黑色干片状粉末,样品质量不再变化,但仅为原样质量的30%~40%。
3.7.2 水溶液聚丙烯酰胺的性质
聚丙烯酰胺能以任何比例与水互溶。外推法得到的聚丙烯酰胺-水体系的θ温度约为-40℃[5]。极低浓度的纯聚丙烯酰胺溶液中,分子链表现为单个无缔合的高分子线团。当聚合物分子量约为106、浓度为6×10-4g/mL时,高分子线团开始互相渗透,对溶液的光散射效果产生影响,浓度稍高时发生机械缠绕,对溶液黏度产生影响。当溶液浓度较低时,聚合物溶液可以视为网状结构,由链间的氢键和机械缠绕作为网络节点;在浓度较高时,溶液中大量链-链接触点使溶液黏度迅速升高并成为凝胶状。
大多数有机溶剂是聚丙烯酰胺的非溶剂,但聚丙烯酰胺水溶液中可以容纳相当量的极性溶剂。例如甲酰胺、联胺、乙二醇和吗啉。41%体积的甲醇水溶液是聚丙烯酰胺的θ溶剂。聚丙烯酰胺水溶液中加入某些物质对溶解有促进作用,例如6mol/L的尿素溶液中,尿素可以破坏聚丙烯酰胺的氢键,在尿素溶液中,聚丙烯酰胺有更快的溶解速度;聚丙烯酰胺水溶液中含有异丙醇,则会防止水溶液在储存过程中出现黏度变化。
聚丙烯酰胺水溶液对很多电解质有良好的相容性。例如氯化铵、硫酸铜、氢氧化钾、碳酸钠、硼酸钠、硝酸钠、磷酸钠、硫酸钠、氯化锌、硼酸、磷酸等都可以与聚丙烯酰胺水溶液共存,不会发生相分离。聚丙烯酰胺均聚物水溶液中加入电解质,对溶液的黏度会有影响。加入氯化钠会提高溶液的特性黏数,加入氯化钙时对特性黏数的影响更为明显。
阴离子聚丙烯酰胺(APAM)水溶液黏度受APAM本身结构以及水溶液中电解质特性影响较为复杂,与聚合物的浓度、分子量、阴离子度、羧基含量以及水溶液pH、电解质种类有关。当聚合物含有羧基时,加入一价的无机盐会使聚合物线团收缩,溶液黏度降低。在测定溶液性质时,通常会加入少量一价无机盐,屏蔽电荷影响,降低溶液黏度。加入二价盐类,例如CaCl2、BaCl2、MgCl2时,低离子度的聚合物水溶液,黏度会随无机盐加入量逐渐降低,达到最小值以后再回升;高离子度的聚合物水溶液中,黏度将随无机盐的加入量急剧下降。在加入三价无机盐时,阴离子聚丙烯酰胺中羧基通常与高价金属形成交联结构,形成凝胶。凝胶性质与形成条件取决于温度、pH、聚合物中羧基含量、金属离子以及聚合物的浓度以及聚合物的分子量因素。
聚丙烯酰胺通常以水溶液形式使用,聚丙烯酰胺水溶液的黏度受到聚合物本身性质、溶液的浓度、温度、pH、剪切速度影响。
(1)聚合物的分子量 在一定温度下,黏度随聚合物分子量的增高而增高,且黏度随分子量的增高存在突变点。在较低分子量范围内,黏度随分子量增加缓慢,超过突变点后,黏度随分子量增加的变化速率显著加快。不同浓度下聚丙烯酰胺溶液都存在这个突变点,即当分子量达到某一数值后,溶液黏度随分子量增大急剧增大,并且突变点的分子量随溶液浓度的提高而降低。通常用分子缠结概念来解释这个现象,即突变点分子量是溶液在该浓度下,聚合物分子线团实现物理缠结的临界点。由于缠结的发生,导致高分子分子链线团之间发生相对运动,分子间摩擦导致黏度发生突变。
(2)聚合物的离子度 聚丙烯酰胺在水溶液中成线团结构,侧链上离子基团通过分子链之间的静电排斥力导致分子链舒展,使溶液中分子线团均方回转半径增大,分子链作用力增强,表观黏度增大。无论是阴离子聚丙烯酰胺还是阳离子聚丙烯酰胺,相同链长时,离子度越高,水溶液黏度越高,见图3-1。

图3-1 聚丙烯酰胺水溶液黏度与离子度关系
(3)水溶液浓度 聚丙烯酰胺水溶液黏度和浓度近似成对数关系,如图3-2所示。

图3-2 聚丙烯酰胺黏度与水溶液浓度关系
对于高分子量聚丙烯酰胺来说,在很低浓度下聚合物溶液即有很高的黏度,即使百分之几的浓度,其水溶液已经相当黏稠,浓度达到5%以上,溶液就会失去流动状态形成胶块状。
聚合物水溶液的黏度随浓度增加而增加,同时在水溶液从浓度极低开始增加浓度时也存在一个突变点,即在浓度达到某一临界点时,黏度急剧增加,这同样是由于溶液中分子缠结起到分子线团运动时空间阻碍的影响。
(4)水溶液电导率与pH 电导率和pH对聚丙烯酰胺水溶液性质影响较大,并且与聚丙烯酰胺的离子性有关。
电解质溶液中,侧链基团在溶液中吸附异种电荷,导致表观离子度降低,水溶液黏度随之降低。非离子聚丙烯酰胺则受电导率影响不大。如图3-3所示,阴离子和阳离子聚丙烯酰胺水溶液黏度受电导率影响很大,在电导率10000μS/cm以内黏度就快速随电导率增大而降低,而非离子产品则不然,非离子产品受电导率影响不大,甚至在很高电导率时表现出随电导率升高黏度提高。

图3-3 聚丙烯酰胺黏度与水溶液电导率关系
pH对聚丙烯酰胺水溶液黏度影响比较复杂。阳离子聚丙烯酰胺通常为丙烯酰胺与(甲基)丙烯酰氧基乙基三甲基氯化铵(DAC或DMC)的共聚物,分子结构中季铵盐基团通过丙烯酸酯基团连接在主链上,酯基在碱性条件下极易水解,常温下,数小时内即发生水解导致溶液黏度降低。
无论何种离子性的聚丙烯酰胺中,丙烯酰胺的酰胺基团均容易发生水解,在低pH(pH<4)通过生成酰亚胺交联性水解,高pH(pH>8)条件下发生碱性水解[6]。
阴离子聚丙烯酰胺在酸性条件下,侧链中的羧酸根基团会被H+中和成为酸式结构,羧酸在溶液中不电离,分子间斥力降低,溶液黏度也会降低。高pH对阴离子聚丙烯酰胺的黏度影响则不大。
(5)剪切速度 聚丙烯酰胺(PAM)水溶液为假塑性流体,其黏度随剪切速率增大而下降。在很低的剪切速率下,黏度与剪切速率无关;当剪切速率增大到临界值以上时,随剪切速率增大,黏度明显下降,即剪切变稀现象,见图3-4。

图3-4 聚丙烯酰胺黏度与剪切速率关系
这种现象也可以用高分子链的缠结的概念来解释。当剪切速率增大时,缠结被部分破坏,缠结点的数目因此有所降低,因而导致黏度下降。
(6)稳定性 聚丙烯酰胺水溶液的稳定性已经能够满足许多应用方面的要求,但会受到物理应力和化学反应作用,或因为细微的链构象重排而使溶液黏度随时间、温度有所变化。像其他水溶性高分子化合物一样,在陈放过程中,黏度越来越小。
曾提出许多机理来阐述初期与分子链断裂无关的黏度损失,其中最合理的解释是:黏度下降是由于链构象的变化导致流体力学体积逐渐变小。新配制溶解的聚合物含有硬芯,这些硬芯结构是由分子内氢键束缚构成环结构和螺旋结构的刚性链段,是稳定的。但由于熵增作用,使氢键缓慢解离和再形成,使大分子变得柔顺,线团变小,流体力学体积和黏度也变小。
在较差的现场条件下,溶液稳定性问题较为复杂。由于溶液可能长时间暴露在高温、有氧条件下,黏度损失严重。一般认为,聚丙烯酰胺黏度损失与聚合物链的氧化断裂有重要关系,并且氧与还原剂以及微量铁、铜盐的组合会促进氧化反应。这种氧化还原对有时来自于聚合时的引发剂残留,或者来自从管道或容器渗透出来的杂质。使用稳定剂例如N,N'-二甲基二硫代氨基甲酸、2-巯基苯并咪唑和苯酚联用可以适当抑制氧化断链。
其他因素包括剪切、光、超声波和加热都可使聚合物降解。特别是分子量很高的聚合物,其分子量和黏度都会在高剪切应力的搅拌条件下降低。
(7)絮凝作用 聚丙烯酰胺分子链很长,它的酰胺基团可以与许多物质亲和、吸附或形成氢键。使得它容易在被吸附的粒子间形成架桥,生成絮团,导致固形物颗粒尺寸增大,沉降速率增快。聚丙烯酰胺的絮凝作用常被用作固-液分离。
3.7.3 聚丙烯酰胺的化学性质
广义的聚丙烯酰胺包括丙烯酰胺的均聚物和共聚物,其共聚单体主要为(甲基)丙烯酰氧乙基三甲基氯化铵和丙烯酸盐类。聚丙烯酰胺链节中主要包括酰胺基、酯基、羧酸根和季铵盐四个官能团。通过这些基团的化学反应,可以获得多种衍生物。
3.7.3.1 水解反应
聚丙烯酰胺可以通过它的酰胺基水解而转化为含有羧基的聚合物,形成类似丙烯酰胺-丙烯酸钠共聚物结构。在早期的阴离子聚丙烯酰胺生产过程中,多使用此方法,按照此方法生产出来的聚丙烯酰胺通常叫作部分水解聚丙烯酰胺(HPAM)。
在水解法生产聚丙烯酰胺时,常利用这个反应,将均聚物用氢氧化钠或碳酸钠水解,最终获得离子度30%以下的阴离子型聚丙烯酰胺。水解反应可以在聚合前的丙烯酰胺溶液中加入碱,也可以在聚合后的胶块中加入碱,经过水解机进行水解。水解法生产阴离子型聚丙烯酰胺(尤其是使用胶块进行水解时)由于碱优先与胶块表面的酰胺基团反应,同时也由于高分子反应的屏蔽效应,难以获得均匀的或者高阴离子度的产品,在生产70%离子度以上的阴离子聚丙烯酰胺时,仍需要用丙烯酰胺与丙烯酸钠进行共聚和。
在中性条件下和弱酸性条件下,丙烯酰胺水解速率较慢,酸性较强时,酰胺基团通过转化为亚酰胺结构导致产品不溶于水。
3.7.3.2 羟甲基化反应
聚丙烯酰胺和甲醛反应生成羟甲基化聚丙烯酰胺,该反应称为羟甲基化反应。聚丙烯酰胺的羟甲基化反应在酸性和碱性条件下都可以进行。碱性条件下反应速率较快,酸性条件下由于甲醛容易形成多聚甲醛导致反应速度要慢很多。
聚丙烯酰胺进行羟甲基化反应时,先将pH调节到10左右,加入甲醛后在30℃下搅拌2h,再调节回中性,即可完成羟甲基化反应。但聚丙烯酰胺经过羟甲基化反应容易形成交联结构。
3.7.3.3 磺甲基化反应
聚丙烯酰胺与NaHSO3和甲醛在碱性条件下反应可以生成阴离子类型的衍生物——磺甲基化的聚丙烯酰胺,这个反应可以将NaHSO3与甲醛一起加入,也可以在羟甲基化的聚丙烯酰胺中加入NaHSO3来完成磺甲基化。
磺甲基化反应要求在碱性(pH=10~13)介质中、50~70℃条件下完成。
3.7.3.4 胺甲基化反应
聚丙烯酰胺和二甲胺、甲醛一同反应可以生成二甲氨基N-甲基丙烯酰胺聚合物。该反应又称为曼尼奇(Mannich)反应:
例如:按聚丙烯酰胺、甲醛、二甲胺摩尔比为1∶1∶1.05的比例先将甲醛、二甲胺预先混合加入到35℃的聚丙烯酰胺溶液中保温3h。曼尼奇反应可以在聚丙烯酰胺分子侧链中引入叔胺官能团,使用时经酸化形成阳离子,可以提高产品的絮凝能力。
3.7.3.5 霍夫曼降解反应
聚丙烯酰胺和次氯酸钠在碱性条件下反应可以得到具有阳离子性的聚乙烯胺。该反应称为霍夫曼(Hofmann)降解反应。反应式如下。
该反应需要将聚丙烯酰胺稀溶液在搅拌下加到含有NaOH和NaClO的溶液中,在室温下保持1h,然后中和到中性,得到聚乙烯胺。由于此时溶液中盐浓度很高,生成的聚合物容易形成沉淀或胶状,容易从溶液中分离出来。胺化度可以达到30%~60%。
3.7.4 聚丙烯酰胺的毒性
聚丙烯酰胺本身基本无毒,因为它在进入人体后,绝大部分在短期内排出体外,很少被消化道吸收。多数商品也不刺激皮肤,只有某些水解体是低毒或无毒的。聚丙烯酰胺的毒性来自残留的丙烯酰胺单体和生产过程中夹带的有毒物质。丙烯酰胺为神经性致毒剂,对神经系统有损伤作用,中毒后表现出机体无力、运动失调等症状。因此美国卫生局规定,当残留单体量超过0.5%(质量分数)时,就应该在聚丙烯酰胺的产品包装上打上“毒性”标志。聚丙烯酰胺工业产品中残留丙烯酰胺含量各国卫生部门均有规定,一般为0.5%~0.05%。如应用于水的一般生化处理时,丙烯酰胺含量在0.2%以下,用于直接饮用水处理时,须在0.05%以下。国标健康卫生组织1985年出版的丙烯酰胺标准指出:聚丙烯酰胺中AM残留量控制在0.05%以下并且控制用量时,处理后水中AM含量将低于0.25μg/L,符合大多数国家的饮用水标准。排放水中AM含量应在1~50μg/L,因此目前欧美主要国家一般规定,饮用水处理及食品工业用聚丙烯酰胺中残留AM的含量应在0.05%以下,并应控制聚丙烯酰胺的用量。各国对用作饮用水处理的聚丙烯酰胺质量要求见表3-3。
表3-3 各国对聚丙烯酰胺用作饮用水净化助剂许可状况[7]

某些阳离子型聚丙烯酰胺情况就要复杂得多,这是因为阳离子聚丙烯酰胺中引入的氨基等基团,其毒性往往数十至数百倍地高于阴离子型、非离子型聚丙烯酰胺。各种丙烯酰胺共聚物毒性应单独考虑。干燥的阳离子聚合物毒性很低,其经口(对鼠)和经皮肤(对兔)的半致死剂量(LD50)分别大于5.0g/kg体重和2.0g/kg体重。而非离子、阴离子和阳离子乳液聚合物的经口(对鼠)和经皮肤(对兔)的半致死剂量(LD50)都大于10.0g/kg体重。对兔进行的初步刺激研究表明,干燥的非离子和阳离子聚合物不刺激皮肤,对眼睛的刺激也极小。干燥的阴离子聚丙烯酰胺对实验动物的眼睛和皮肤无刺激性。
3.8 聚丙烯酰胺国内外发展史
聚丙烯酰胺在1893年由实验室制得。1952年美国氢氨公司首先进行了聚丙烯酰胺工业生产研究,两年后即正式投入大规模工业生产,也就是在1954年首先在美国实现了商业化生产,初期的品种仅是单一的非离子型聚丙烯酰胺,不久开发了碱性水解的阴离子型聚丙烯酰胺和阳离子型聚丙烯酰胺。聚丙烯酰胺优良的水溶性、增稠性、絮凝性能和化学反应活性显示出了巨大的市场潜力和广阔的应用前景。丙烯酰胺单体由丙烯腈经硫酸催化水合制取。20世纪70年代初美国和日本开发了丙烯腈铜催化水合法,1985年在日本又有丙烯腈生物酶催化水合法问世。20世纪80年代初,美国陶氏化学公司(Dow Chemical Co.)已有万吨级生产线。一些具有特殊性能的衍生物也已实现工业化生产。
我国聚丙烯酰胺产品的开发始于20世纪50年代末期。1962年上海珊瑚化工厂建成我国第一套聚丙烯酰胺生产装置,生产水溶胶产品,用于矿产品处理和石油钻采工业。随后又开发出了辐射聚合法、反相乳液聚合法和水溶液聚合法生产聚丙烯酰胺干粉。由于在油气田开采和三次采油中的大量应用,以及在污水处理、造纸等方面用量的增加,我国聚丙烯酰胺的生产能力不断增加。自1994年自主开发的生物酶法制丙烯酰胺生产线的建成,以及1995年引进法国SNF公司5万吨/年聚丙烯酰胺生产装置后,我国的聚丙烯酰胺的产量和质量有了更大的提升。
我国已是全球最大的聚丙烯酰胺生产国,销售量占全球销售量的40%。从2006年开始,销售量是美国的2倍,是日本的4倍。
3.9 聚丙烯酰胺的制造方法
工业上聚丙烯酰胺及其衍生物是丙烯酰胺单体通过自由基聚合获得的[8~12]。依据聚合时单体的分散状态可以分为本体聚合、溶液聚合、悬浮聚合和乳液聚合。丙烯酰胺聚合在除本体聚合以外的聚合方法均有实施。聚丙烯酰胺及基本聚合过程如下:
3.9.1 丙烯酰胺的自由基聚合
自由基聚合反应全过程一般由链引发、链增长和链终止三个基元反应组成,聚合过程中还会发生链转移反应。丙烯酰胺的均聚合或共聚合符合高分子聚合的一般规律,各基元反应如下。
3.9.1.1 链引发
通过引发剂形成自由基,引发单体开始聚合。链引发阶段包括两步反应,第一步由引发剂分解形成引发剂自由基,并与单体反应形成单体自由基。
自由基的形成可以有多种引发方式,包括高能辐射引发、偶氮化合物或过氧化物分解引发、氧化还原引发、光引发剂在紫外线作用下引发。各种引发方式都可以形成自由基,自由基与单体反应形成单体自由基,单体自由基形成以后,聚合反应过程与引发剂关系不大,但某些引发方式会产生引发剂片段,对聚合过程的链终止和转移会有一定影响。例如某些特殊的引发剂分解后,其中部分片段由于空间位阻作用无法实现链引发,但可以参与链终止,终止后的分子链结构在聚合相同条件下可以再次引发。通过这种特性可以实现丙烯酰胺的活性聚合,得到特殊结构聚合物。
3.9.1.2 链增长
单体自由基与其他单体进行加聚反应,使聚合物链段增加,这个过程称为链增长。丙烯酰胺单体聚合活性很高,很容易进行链增长反应,也容易获得较长分子链。链增长是聚合物分子量提高的重要阶段,聚合物的聚合度由链增长速度与链终止速度共同决定,统计上讲,聚合度的大小等于链增长速度与链终止速度的比值。提高链增长速度可以用提高单体浓度的方式实现,通过减少引发剂使用或利用界面扩散方式可以有效降低链终止速度。
3.9.1.3 链终止
在聚合过程中活性中心为自由基,自由基寿命很短,聚合过程伴随有链终止反应,链终止包括单基终止或双基终止,自由基与自由基相碰撞容易发生双基终止。链终止和链增长是竞争反应,其类型和速度与分子链结构以及体系中自由基浓度有关。要获得足够高分子量的产品,需要保持体系中的低自由基浓度。
3.9.1.4 链转移
链转移反应是聚合过程中常见的副反应,自由基在遇到其他物质时将自由基传递到其他物质上,形成一个高分子链和一个新的自由基,新的自由基可以继续引发聚合实现链增长。动力学上,链转移反应并没有导致自由基数量变化,链转移反应聚合速度不变,但聚合物分子量将受到很大影响。多种物质都可以参与链转移反应,链转移反应通常意味着一个大分子链增长的停止和另一个大分子链的开始,但当链转移发生在聚合链上时,即向大分子链转移,会在聚合物链上形成一个支化点,支化点的出现对聚丙烯酰胺的使用会带来影响,支化点过多还会引起聚合物链交联。
3.9.2 丙烯酰胺聚合体系
根据聚丙烯酰胺合成时共聚单体的类型,聚丙烯酰胺可以分为阳离子型、非离子型和阴离子型以及两性型。非离子型聚丙烯酰胺通过丙烯酰胺单体直接均聚得到;阳离子型聚丙烯酰胺和阴离子型以及两性聚丙烯酰胺则可以由丙烯酰胺单体和阳离子/阴离子单体共聚得到或者由丙烯酰胺均聚物通过化学反应改性得到。由于丙烯酰胺为固体且难以熔融,难以进行本体聚合。各种聚丙烯酰胺均可以通过本体聚合以外的其他聚合体系生产,并得到不同形态的产品类型[13~17]。
3.9.2.1 水溶液聚合
聚丙烯酰胺的水溶液聚合是丙烯酰胺和共聚单体在水溶液中直接聚合获得的。这个体系是丙烯酰胺聚合的最简单体系。将单体在水中溶解形成溶液,除氧后加入适当的引发剂,聚合后即获得聚丙烯酰胺水溶液产品。由于聚丙烯酰胺通常具有很高的分子量,导致溶液黏度很高,在聚合物浓度达到5%以上时,就容易由于过黏而形成胶块状产品。由于含量过低,难以形成经济价值,因此聚丙烯酰胺水溶液产品类型实际应用意义不大。
当聚丙烯酰胺溶液浓度在5%~35%时,往往聚合后形成胶块状。胶块状产品不能长期存放,溶解也相对困难,并没有作为常规商品形式大量使用,通常需要将胶块状产品干燥后制备成颗粒状使用。在一些自产自用的条件下可以使用胶粒状产品,节省干燥环节,降低生产成本。大规模生产时,通常将胶块状产品首先通过搅笼或螺杆,将胶块剪切成数毫米大小的胶粒,胶粒干燥后进行研磨粉碎,粉碎后的聚丙烯酰胺形成粉粒状产品。胶块加工过程需要蒸发掉大量水分,成本较高,同时胶块的加工过程中也会导致部分分子链断裂使产品分子量降低,但粉粒状产品便于储存、运输,使用时在数十分钟内可以重新溶解成溶液使用。
丙烯酰胺与其他单体聚合的动力学取决于温度、介质的pH、所用溶剂的性质以及聚合体系中其他组分的存在等因素[18~20]。
丙烯酰胺水溶液聚合时,反应速率Rp与单体、引发剂浓度有关:
聚合速率通常正比于引发剂浓度的平方根,正比于单体浓度的1.2~1.5次幂。关于pH、温度对丙烯酰胺聚合速率的影响见表3-4。
表3-4 水溶液中AM的聚合参数

3.9.2.2 反相乳液聚合
丙烯酰胺双键密度较高,聚合放热量大,在聚合时温度上升明显。而且水溶液聚合时会形成胶块,体系散热困难。因此不少科学家研究丙烯酰胺在乳液状态的聚合方式。与常规的乳液聚合类似,聚丙烯酰胺可以通过乳液聚合方式获得。在适当的油和表面活性剂存在时,将水相逐渐滴加入油相中,并辅助搅拌或高速剪切乳化,能够获得性能良好的油包水乳液,即反相乳液。反相乳液状态下进行的聚丙烯酰胺聚合可以获得反相乳液产品。
在反相乳液配制时,需使用非离子型表面活性剂,由于非离子型表面活性剂形成的液滴无法利用电荷排斥实现乳液稳定,反相乳液主要依靠表面活性剂的空间位阻实现乳液的稳定。同时由于连续相油的密度比水相密度低,使得聚丙烯酰胺反相乳液容易出现分层。
反相乳液聚合的机理目前还没有统一的说法。有说法认为反相乳液反应机理与正相乳液相同,聚合过程存在乳胶粒和单体液滴。聚合过程中伴随单体液滴的减少和乳胶粒的增长。但更多的说法认为反相乳液中不存在单体液滴,聚合前期通过高速剪切乳化以后,形成粒径大致均匀的乳胶粒,反应均发生在乳胶粒内部,整个乳液聚合过程相当于无数个细小的水溶液聚合。笔者认为这两种机理同时存在,在不同的配比和乳化液情况下存在不同的机理。在中低阳离子聚丙烯酰胺反相乳液聚合过程中,未观察到体系的明显变化。但在高阳离子度配比时,聚合前乳化液为乳白色,伴随聚合过程进行,乳液颜色越来越透明,最后白色消失,形成半透明细乳液状态,可能是由于单体液滴消失导致乳液外观发生变化。
由于聚丙烯酰胺的特殊性质,反相乳液聚丙烯酰胺最突出的特点在于可以合成微交联结构产品。聚丙烯酰胺的其他聚合方式,单体在连续相中,若存在少量多官能团单体,聚合物链会形成严重的交联和缠绕结构,最终使得产品难以溶解,无法使用。但反相乳液体系中,可以合成微交联结构产品,这种交联结构不会引起产品溶解问题。同时微交联的聚丙烯酰胺在作为絮凝剂使用时,可以增加絮团间的吸附点以及更密集的缠绕结构,使得絮团抗剪切能力增强,在污泥的离心脱水或高压脱水时有异常优异的表现。
3.9.2.3 反相悬浮聚合
反相悬浮聚合是介于反相乳液聚合和水溶液聚合之间的聚合状态。反相悬浮聚合时,不加入表面活性剂。聚合体系用搅拌方式使水滴在有机溶剂中分散成微米级尺寸液滴,配合分散剂或少量乳化剂,使液滴在合适的搅拌条件下保持液滴尺寸。聚合时每个液滴里按照独立的水溶液聚合机理进行。
反相悬浮聚合结束后,可以通过过滤的方式除去大多数有机溶剂,剩余产品经简单干燥可以获得直径0.5~1mm球形颗粒。反相悬浮方法生产的聚丙烯酰胺产品无细粉存在,产品溶解速度比常规固体聚丙烯酰胺更快。但由于反相悬浮法本身工艺技术复杂、对设备要求高、有机溶剂分离成本高等缺陷,现在已经逐步退出市场。
3.9.2.4 分散聚合
丙烯酰胺单体与聚丙烯酰胺的溶解性质不同。利用这种不同可以在适当的条件下,使聚合物在聚合反应过程中从聚合体系内沉淀出来,但聚合物的密度与反应液密度相近,沉淀出的聚合物无法沉降,稳定分散在体系内,形成分散液。这种聚合方式称为分散聚合,分散聚合获得在水溶液中的分散液产品,俗称水包水乳液。
研究发现,聚丙烯酰胺在某些聚合物或无机盐的水溶液中会降低溶解度。例如在聚乙二醇水溶液、蛋白质水溶液、聚电解质水溶液或者是氯化钠、硫酸铵水溶液中,聚丙烯酰胺的溶解度受到较大影响,当使用丙烯酰胺在这些溶液中聚合时,生成的聚合物会发生沉淀并最终形成分散液产品。分散液产品的分子量主要由分散剂的性质决定。这种分散聚合产品中,是尺寸约数十微米的聚丙烯酰胺颗粒分散在其他聚合物溶液中,当水分散液产品在水中溶解时,连续相的聚合物或无机盐迅速在水中稀释,稀释后连续相失去对聚丙烯酰胺微粒的沉淀作用,可以在水中迅速溶解。这也是水分散液形态聚丙烯酰胺的突出优势。
3.10 聚丙烯酰胺产品分析方法
具体方法参照GB/T 17514—2008、GB/T 31246—2014。
3.11 聚丙烯酰胺产品包装与储运
聚丙烯酰胺根据产品形态有胶体状、干粉状、乳液状等,主要以干粉状和乳液状储存。干粉状产品装在内衬聚乙烯塑料的编织袋或复合纸袋中,一般每包净重25kg,也可以直接使用大编织袋包装,每包500~750kg。乳液产品通常储存在1000kg聚乙烯IBC桶内,或使用25kg塑料桶包装。
每批产品应附有质量检验报告单,每个包装件上应有清晰、牢固的产品标志,并注明下列内容:名称及型号,品级,净重,生产厂名,批号及生产日期,标准号,防热、防晒图示标志。粉粒产品还应有防潮图示标志。
在通常的储存条件下,固体聚丙烯酰胺具有很好的稳定性,保质期为1年。乳液产品一般在3~6个月。
产品在储存、制备和输送时,最好选用不锈钢或耐腐蚀的塑料材料,避免与铁、铜类金属接触。
3.12 聚丙烯酰胺的应用
聚丙烯酰胺分子链的显著特点决定了聚丙烯酰胺在多个领域有特殊应用。聚丙烯酰胺亲水性很强,本身强度不高,不能作为结构材料使用,多用作辅助助剂类用途。聚丙烯酰胺特殊结构主要表现为:①主链为憎水碳链,侧基为强亲水基团;②分子量超高;③侧基可以带有电荷。聚丙烯酰胺的这些特殊分子链结构,使得它可以广泛应用于各个行业。例如聚丙烯酰胺作为分散稳定剂;在油气田工业中用作钻井、采油助剂;在水处理行业中作为絮凝剂;在造纸工业中用作助留助滤剂;在矿物冶炼、纺织、建材和农业中的应用等。
3.12.1 聚丙烯酰胺作为分散剂的应用
在胶体分散体系中投加高分子分散剂,使分散粒子得以稳定,在很多实际应用领域中愈显突出。聚丙烯酰胺产品主链为碳链结构,带有明显憎水特性,而侧基则含有大量亲水性的酰胺基,使得分子链本身具有很强的两亲性能,可以起到分散作用。丙烯酰胺聚合物的应用领域大部分与分散体系的稳定有关。
分散体系的稳定实际上是其某些性质,例如浓度、粒径、密度等,主要指粒径的稳定。对于稳定性的描述,通常用热力学和动力学两方面进行研究。
(1)热力学稳定 通常分散体系在热力学上是不稳定的,在分散体系中存在两相间的界面性质差异,热力学上有使表面积减小的趋势,导致分散相会逐渐团聚以减小表面积。因此,从热力学角度,若增加分散相的稳定性,则需要减少两相界面中比表面能。
(2)动力学稳定 尽管在很多分散体系中,热力学上是不稳定的,但在动力学上有可能使分散体系足够稳定。
(3-1)
式中,为x方向的平均位移;t为时间;η为连续相的黏度;r为颗粒半径;R为气体常数;T为热力学温度;NA为阿伏伽德罗常数。
(3-2)
式中,r为颗粒半径;η为分散介质的黏度;ν为粒子沉降速度;Δρ为两相密度差;g为重力加速度。
由于在分散体系中,分散相颗粒会受到布朗运动影响,当体系布朗运动单位时间位移小于粒子沉降速率时,颗粒迟早会全部沉淀,即热力学上不稳定,若布朗运动单位时间位移远远大于粒子沉降速率时,分散体系则可以长期稳定存在。布朗运动有助于提高分散体系的稳定性,但温度过高时,会增加颗粒的碰撞次数,加速颗粒聚集,也不利于分散体系稳定。动力学角度讲,提高分散体系稳定性的方法是降低体系的温度和增大介质的黏度。
颗粒的布朗运动单位时间位移以及颗粒沉降速度都与颗粒半径有关,颗粒半径越小,布朗运动位移越大,沉降速度越慢,体系越稳定。在分散体系中,颗粒之间有强烈的碰撞聚集倾向,一旦碰撞导致颗粒半径变大,稳定性将随之消失。如何有效避免颗粒碰撞导致的聚集现象,是分散体系稳定的关键。加入适当的聚丙烯酰胺,尤其是侧链带有电荷的聚丙烯酰胺是避免颗粒聚集的有效办法。
聚丙烯酰胺在分散体系中可以通过空间位阻和静电稳定双重作用对颗粒进行稳定。高分子容易在颗粒表面吸附形成保护层,此时高分子的亲水侧链伸向水中,高分子吸附层的厚度提供颗粒之间的间隙,减小了颗粒间范德华力,增大了颗粒聚集的势能,提高稳定性。
高分子可以以三种形式在颗粒表面形成吸附,分别为单点吸附、圈吸附和平面多点吸附(见图3-5)。单点吸附是高分子链一端与颗粒表面形成吸附点。分子量越高,吸附量越大,空间位阻越大。通常高分子在颗粒表面的吸附以圈吸附为主,高分子链多点与颗粒表面形成吸附,吸附量与分子量关系不大。若聚合物以无规线团方式吸附,则吸附量与分子量平方根成正比。实验发现具有较低分子量的聚合物更容易优先与颗粒表面形成吸附。因此在高分子聚丙烯酰胺作为分散剂使用时,聚丙烯酰胺的分子量和分子量分布尤为重要,过低的分子量吸附后空间位阻不够,难以形成有效分散;过高的分子量容易导致颗粒的絮凝。性能优良的分散剂需要有较低的分子量分布系数。

图3-5 聚丙烯酰胺在物质表面的吸附类型
很多聚丙烯酰胺分散剂是带有电荷的高分子链,分子侧基往往带有阳离子或阴离子电荷。带电荷的分子链吸附在颗粒表面后,不仅提供空间位阻作用,还利用静电作用增加颗粒间排斥力,提高颗粒稳定性。
根据双电层理论,当颗粒表面吸附了高分子分散剂后,分散剂侧基的电荷将形成颗粒表面的电荷保护层,保护层的电动势称为ξ电位,ξ电位越高,颗粒在碰撞时受到的排斥力越大,分散体系越稳定。物质表面电荷分布及ξ电位见图3-6。
图3-6 物质表面电荷分布及ξ电位
分散剂分子量是分散体系稳定作用的重要因素。一般来说,分子量越高,高分子在颗粒表面上形成的吸附层就越厚,稳定效果也越好。许多高分子还存在一个临界分子量,低于此分子量的高分子无保护作用。通常作为无机微粒分散剂使用的聚合物分子量水平在2000~5000。
3.12.2 聚丙烯酰胺在油气田工业中的应用
油气田开采过程复杂,包括钻井、固井、完井、修井、压裂、酸化、注水、堵水调泡、采油驱油、采出液处理等过程,使用的化学品种类繁多,聚丙烯酰胺可以广泛用于石油开采的各作业过程。特别是在钻井、堵水调泡和驱油领域。中国的石油工业是聚丙烯酰胺的最大应用领域,30%~40%的聚丙烯酰胺用于石油工业。
3.12.2.1 在钻井中的应用
在油气田工业中,井是所有工序的基础,钻井质量是油气开采的关键因素。在钻井过程中,需要用液态泥浆给钻头冷却和润滑,并将岩石屑带出油井。以前使用清水作为钻井液,由于清水分散作用较弱,钻井液黏度低,易分层,钻井液不稳定。后来将聚丙烯酰胺应用于钻井液处理,大大改善了钻井环境,提高钻井速度。现在聚丙烯酰胺已经在钻井中的降滤失、絮凝、页岩抑制、堵漏等方面起重要作用。
(1)降滤失剂 在钻井过程中,泥浆中的水分会向地层中渗透。钻井液渗入地层后,会引起黏土膨胀垮塌,井壁不稳定,同时水损失后导致滤饼增厚、井壁减小等问题。滤失量过大,给钻井工作带来很大危害,甚至可能导致井报废。
(3-3)
式中,Vf/A为单位面积滤失量,m3/m2;K为滤饼的渗透率,μm2;ΔP为滤饼两侧压差,Pa;Cc为滤饼中固相的体积分数, %;Cm为泥浆中固相的体积分数, %;t为渗滤时间,s;μ为滤液的黏度,Pa·s。
滤失本质上讲是钻井液水分的渗透流失,单位面积上的滤失量与井内外压差、滤液黏度等因素有关。其中决定因素是滤液的黏度和滤饼的性质。
聚丙烯酰胺作为降滤失剂在钻井液中主要起到护胶、水化膜增厚、增稠、堵孔的作用,通过这些作用降低水分滤失的速度。
(2)护胶作用 在钻井液中,聚丙烯酰胺起到一部分分散剂作用。分散剂使得细小的黏土颗粒表面更加稳定,难以团聚形成大颗粒,当分散的细小黏土颗粒形成足够浓度后,可以在井壁形成薄而致密的滤饼,从而提高水分通过滤饼的阻力,降低滤失量。
(3)水化膜增厚 根据吸附理论,分散好的黏土颗粒表面会形成一定厚度的吸附层,吸附层的增加可以使黏土颗粒水化膜增厚,降低滤饼中固相的体积分数,根据式(3-3)可知,单位面积滤失量会降低。
(4)增黏作用 聚丙烯酰胺的加入可以提高钻井液黏度,根据式(3-3),滤失量与滤液黏度的平方根成正比,聚丙烯酰胺的加入可以降低滤失量。
聚合物钻井液处理最早使用的是水解聚丙烯腈,选择分子量在10万~20万的聚丙烯腈或聚丙烯酰胺,经碱水解成盐,分子链中的腈基和酰胺基有利于聚合物在黏土颗粒上的吸附,羧基起水化作用,提高黏度并且增加水化膜厚度。现在根据不同现场特性逐步开发出多种性能更加优良的多元共聚物。例如磺化聚丙烯酰胺[21]、耐温抗盐共聚物[22,23]、阳离子型共聚物系列等[22]。
(5)页岩抑制剂 在钻井过程中以及油井使用过程中,来自下钻过程钻头的碰撞、钻井液冲刷、地层压力和应力的释放、松散地层的坍塌和变形等影响,会导致井壁改变形态,这种现象称为井壁不稳。
钻井液中的聚丙烯酰胺通过吸附作用和堵孔作用,保护钻井液中的溶胶颗粒,可有效减少滤液的渗透,防止黏土水化膨胀。常用的聚合物类页岩抑制剂主要有聚丙烯酰胺、水解聚丙烯酰胺和磺化聚丙烯酰胺。它们吸附在黏土颗粒表面后,形成纵横交错的分子膜,增强井壁上页岩的强度。此外水化基团的水化作用能形成可压缩性泥饼,阻止水向地层渗透,防止黏土水化膨胀。分子链含有阴、阳离子的两性聚丙烯酰胺具有很强的抗盐、抗钙、耐高温及降滤失能力,抑制性强,防塌效果好。
(6)堵漏剂 在地层中往往存在钻井液漏失情况,通常钻井液漏失的主要原因有高渗透砂岩地质导致的渗透性漏失,地层天然裂缝或人工裂缝引起的裂缝性漏失以及溶洞地质引起的溶洞性漏失。当钻井液出现漏失时,需要利用堵漏剂对地层进行封堵。渗透性地层的堵漏可以采用聚丙烯酰胺形成凝胶堵漏,对于裂缝性和溶洞性的地层漏洞,需要用膨胀型聚丙烯酰胺凝胶颗粒堵漏。当凝胶尺寸达到漏缝尺寸的1/3时,就可以通过颗粒间的桥连产生滤饼形成漏失地层封堵。在封堵时往往还加入无机材料进行混合使用,提高封堵强度。
在固井作业中,有时需要在特殊地质深度处进行固井作业(例如严重漏失层、地质坍塌层或高压油气层),保护钻井通道不受其他地层影响。在固井时,需要将水泥浆输入固井作业区域,水泥浆的输送遇到钻井液类似滤失问题,需要加入聚丙烯酰胺减少水泥浆的滤失与漏失,同时需要降低水泥浆输送的阻力并减缓水泥浆凝结固化。
钻井完毕,在完井和修井作业时,依然需要考虑完井液和修井液的滤失问题,需要增大完井液和修井液的黏度,提高黏度的稳定性。
钻井过程中,聚丙烯酰胺主要通过对黏土分散体系的稳定,以及提高黏土水化层,形成致密滤饼,并适当提高钻井液黏度,实现降低钻井液的滤失性。
3.12.2.2 在压裂中的应用
在低渗透油层中,原油的流动阻力很大,需要用酸在地层中腐蚀出裂缝,并将裂缝固定,提高岩层的空隙降低液体流动阻力。这个腐蚀的过程称为压裂,使用的液体称为压裂液。为了将更高含量的支撑剂悬浮在压裂液中,并带到目标地层,需要用聚合物对压裂液稠化,但由于聚丙烯酰胺降解,除高温油藏外,不倾向使用聚丙烯酰胺类压裂液。
在进行酸化压裂时,为使高浓度酸达到更远的地层实现压裂目的,需要减缓酸液与岩石的反应速度,作业时在酸中加入丙烯酰胺聚合物,提高酸的黏度。通常用的酸化增稠剂为丙烯酰胺与其他单体的共聚物,阴、阳离子类型聚丙烯酰胺都可以作酸化增稠用。
在酸化压裂过程中,聚丙烯酰胺的主要作用是对注入酸增稠。提供更长的酸化时间,延长酸化压裂深度。
3.12.2.3 在油井注水中的应用
(1)破乳絮凝剂 经过水驱采油后的采出液中带有大量水,尤其是采油过程中可能往地层中注入大量的表面活性剂和聚合物,使得采出液成分非常复杂。采出液经油水分离后脱出的污水含有大量固体悬浮物、少量原油和前期加入的各种化学助剂,这些成分在地层高温下形成稳定性极高的乳化液状态。但由于采油污水不能直接排放,必须进行处理后回注地下,这也对采出液污水处理提出很高的要求。
污水中最难处理的是乳化层,在地层高温下,原油吸附表面活性剂在地下形成稳定乳液。通常原油吸附的是阴离子表面活性剂,乳滴表面带有阴电性,可以通过加入阳离子聚合物的方式中和乳滴表面负电荷,并通过架桥作用使乳滴聚并、上浮,再经过沉降分离[24]。
对于这种污水通常采用有机无机复合絮凝的方式,首先加入聚合氯化铝等无机聚合物混凝剂,破坏乳液的稳定性,再加入高分子量的阴离子聚丙烯酰胺絮凝。但对于高含油量、高矿化度、高电导的污水,则需要利用阳离子有机聚合物作为破乳剂,并辅助高分子量絮凝剂,可以基本解决含表面活性剂和驱油聚合物的污水回注的难题。
(2)黏土稳定剂 采出液污水处理后回注时有可能对地层造成伤害,在回注水时需要降低注水速率,也需要在回注水中加入黏土稳定剂。实际作业中,可以使用聚丙烯酰胺衍生物,利用聚丙烯酰胺先和甲醛进行羟甲基化反应,然后与二甲胺缩合成为阳离子季铵盐,在胜利油田中应用得到良好的黏土稳定作用。
(3)堵水调剖剂 长期注水的老油井中,由于大量注水,在地层高渗透层中,存在非常明显的突进或指进,导致油井过早水淹,产油量下降,采出液80%甚至90%以上为水。此时需要在井中注入堵水调剖剂对高渗透层或者裂缝层进行封堵。封堵可以采取两种形式,一种通过注水井封堵高渗透层或裂缝,另一种是封堵油井出水层。两种方法原理基本相同,只是在作业时用量和施工方法上有区别。
现在使用最普遍的堵水调剖剂是聚丙烯酰胺类。使用时,使聚丙烯酰胺类聚合物在高渗透层或者裂缝层发生交联反应,反应后形成凝胶封堵岩石缝隙。由于聚丙烯酰胺注入时黏度较低,主要进入高渗透层,对低渗透层影响较小。堵水调剖作业后,可以提高低渗透层的采出效率。
在堵水调剖时,将聚丙烯酰胺和交联剂注入井中进入高渗透层或裂缝层,侧基上的酰胺基团可以与交联剂在高温下发生交联。交联剂可以用高价态的金属离子(例如Al3+、Cr3+、Ti4+)或醛类有机物(甲醛、二元醛或含有甲氧基的酚醛树脂)。产品在作业过程中,常使用具有高分子量的聚合物与交联剂配合,使用的聚丙烯酰胺分子量在1000万以上,在聚合物浓度极低时,由于高分子链间距较大,高分子与交联剂的反应主要发生在分子内部,不会形成连续的块状凝胶,而是形成分散凝胶颗粒,选择合适的交联度,能够调节分散凝胶颗粒的强度。在合适的凝胶强度下,凝胶具有一定的变形能力,在底层压力大时,可以通过变形透过底层,在地层压力较小时,则会堵住缝隙,迫使水进入低渗透区域,提高注水的波及系数。另一种技术采用更低交联水平的凝胶体系,使得生成的凝胶颗粒强度略微降低,凝胶在高渗透区仍具有一定的流动性,实现动态调剖效果。这种动态调剖的波及效果要远远好于固定凝胶的波及效果,更大限度地扩大波及体积。
3.12.2.4 聚丙烯酰胺在三次采油中的应用
当地下油井经过二次采油(注水驱油)后,由于水黏度低,与地下原油差异很大。水容易快速通过高渗透区直接进入油井,难以进一步提高采收率。此时需要进行三次采油,三次采油的基本原理是提高驱油剂的波及系数,这需要提高原油的流度或降低驱油剂的流度。当使用聚丙烯酰胺水溶液作为三次采油驱油剂时,聚丙烯酰胺的存在导致驱油剂的黏度提高,降低了驱油剂的流度,使得驱油剂被迫波及更大范围。目前我国三次采油中聚丙烯酰胺年消耗量已经超过10万~15万吨。
聚合物驱油是通过在注入水中加入一定量高分子量的水溶性聚丙烯酰胺聚合物,增大注入水的黏度,从而改善地下油和水的流度比。注入的聚合物溶液具有较高的黏度和通过油层后具有较高的残余阻力系数以及黏弹性,黏度和弹性越高,残余阻力系数就越大,油和驱油剂的流度比就越小,聚合物驱油剂扩大油层的宏观和微观波及系数的作用也越大,采收率提高幅度也越大。
聚丙烯酰胺在高温和碱性条件下会发生水解,水解后酰胺基团变为羧酸根基团。由于三次采油使用的聚丙烯酰胺往往是阴离子聚丙烯酰胺,水解后生成的羧酸根基团将导致聚丙烯酰胺阴离子度增加,增加的阴离子度在电解质作用下会发生卷曲,导致聚丙烯酰胺溶液表观黏度下降。尤其是在阴离子度超过40%时,在地下与Ca2+和Mg2+相遇,会发生沉淀导致黏度急剧下降,因此油田三次采油用聚合物必须保证在油田地层条件下,3个月以上聚合物分子内阴离子度小于40%,对聚合物稳定性要求很高。
合成具有耐温抗盐特性的聚丙烯酰胺有多种思路,比较流行的方式有两大类,一类是针对聚丙烯酰胺水解特性,用难水解、与Ca2+以及Mg2+弱相互作用的单体,例如AMPS、n-VP等单体替代部分丙烯酰胺。该聚合物由于丙烯酰胺链节减少,同时这类单体共聚以后产生空间位阻,也降低了丙烯酰胺中酰胺基水解的概率。使共聚物的耐水解能力有所增强。这类方法可以真正有效地提高产品的耐温抗盐特性。但由于原料价格因素难以获得有经济价值的产品,同时这类产品由于空间位阻原因,双键活性减弱,共聚能力也很弱,难以与丙烯酰胺形成均匀的高分子量聚合物。
另一类耐温抗盐聚丙烯酰胺的合成思路是通过交联的方式提高分子链之间作用力,进而提高聚合物溶液表观黏度。由于在地下难以对化学反应进行控制,在三次采油聚丙烯酰胺设计中通常使用物理交联和电交联,这两种交联在产品使用过程中是可逆的,便于现场操作。
聚丙烯酰胺的电交联是通过分子链中携带阴、阳电荷交联,合成两性聚丙烯酰胺驱油剂。两性聚丙烯酰胺在某个pH下会呈现为电中性,在该处阴、阳离子处于平衡状态,阴、阳离子官能团作用力最强,表现黏度最高,甚至出现沉淀现象。两性聚丙烯酰胺呈现电中性的pH称为等电点。在配制驱油剂时,应躲避开两性聚丙烯酰胺的等电点。在地层pH环境下,驱油剂达到等电点附近,分子链间阴、阳离子发生电荷交联,驱油剂黏度上升,起到驱油作用。但两性聚丙烯酰胺在使用过程中存在两方面问题。一方面是分子链中阳电荷与地层土壤作用力较强,容易在浅层土壤吸附。另一方面,丙烯酰胺链节在地层中逐渐水解,导致分子链阴离子度逐步增大,等电点发生漂移,导致驱油剂黏度衰减,不利于驱油。
聚丙烯酰胺也可以通过物理交联实现增黏。在聚丙烯酰胺侧基或侧链上引入疏水基团,形成诸如疏水缔合聚丙烯酰胺,或者梳状结构聚丙烯酰胺。侧链或侧基上的疏水基团在水体中容易互相吸附并形成物理交联,黏度上升;在高剪切作用下,交联网络被分子间摩擦力破坏,分子间失去物理交联,表现黏度会骤然降低。这一特性可以表现为高速注水时驱油剂黏度低,在地层中流速减慢后,分子链中憎水基团或憎水链段形成交联网络,黏度上升,完成驱油。疏水缔合和梳型聚丙烯酰胺也存在一些问题。憎水单体往往共聚性能也较差,难以得到很高分子量的产品,此外分子链间形成物理交联需要高分子浓度达到临界缔合浓度以上。当高分子浓度低于临界缔合浓度时,表现为分子内缔合,分子链严重卷曲,黏度大大降低。当疏水缔合型驱油剂使用时,聚合物被地下水稀释到临界缔合浓度以下,将迅速失去驱油效果。
3.12.3 聚丙烯酰胺在水处理工业中的应用
3.12.3.1 聚丙烯酰胺在水处理工业中的现状
我国是一个水资源短缺的国家,人均水资源占有量约为2200m3,不足世界平均水平的四分之一。近年来随着工业和城市生活用水量的激增,水环境污染日益严重,水质污染型缺水更加剧了水资源的短缺。为促进经济社会与人口、资源、环境协调发展,贯彻落实中央提出的水资源可持续利用是我国经济社会发展的战略问题,核心是提高用水效率,要把节水放在突出位置,发展循环经济,提高用水效率和效益,缓解水资源对经济发展的制约,实现水资源的可持续利用。因此节约用水、合理开发水资源、治理水污染已成为我国目前急需解决的重大课题。
节约用水、合理开发水资源、治理水污染都离不开水处理技术。水处理技术是指通过物理(机械)、化学(药剂)和生物等方法,对水质进行处理,使之能满足人民生活、工业生产和环境需要的技术。近年来,随着世界水资源的渐趋贫乏和工业用水量的增大,我国的水处理技术正在蓬勃发展。自20世纪70年代初,大批专家学者、技术人员进入水处理领域,开拓进取,填补了国内一个又一个空白。进入21世纪,随着经济的高速发展和人民生活水平的不断提高,对水资源的保护和利用更显得迫切。为此,从事水处理工作的企业迅速崛起,水处理技术得到前所未有的广泛应用和推广。新的领域不断开拓,水处理剂产品和水处理技术不断创新和诞生。
我国是发展中的国家也是水资源短缺和污染较为严重的国家之一,相对于发达国家而言,我国的水处理化学品发展比较晚。但是起步晚的我们,在不断总结经验,水处理化学品在不断发展壮大,尤其是中国的水处理化学品市场,未来我国将成为世界最大的水处理化学品市场。
2015年4月,国务院发布了《水污染防治行动计划》(以下简称“水十条”),对全面控制污染物排放、生活污水处理设施提标改造、节约保护水资源、开发非常规水源和保护水资源提出明确要求。而这些目标也刺激了水处理药剂的市场需求。工业废水和资源回收都是药剂需求重点,再生水深度处理是水处理化学品特别是中高端产品市场的重要驱动力。对于全面控制污染物排放的目标,“水十条”无论从次序、着墨还是措辞上看,都更多地剑指工业,而工业废水单位处理量需要消耗的化学品本来就比市政污水处理高出许多。所以,可以预见水处理化学品未来的增长引擎当以工业废水处理为首。值得注意的是,水处理化学品由于隶属高能耗、高污染的化工行业,所以相关规定也是一把双刃剑,特别是对于采用粗放型生产方式的生产企业来说,更是考验企业生产和管理的试金石。
“水十条”是当前和今后一个时期全国水污染防治工作的行动指南,水处理行业将正式进入发展期。主要市场在东部发达地区,东部地区水处理化学品生产企业占全国的85.92%,重点流域无磷配方的水处理药剂将在市场中更受青睐。
2010年中国水处理应用中有机高分子絮凝剂的消费量为6.79万吨,约2.228亿美元。中国2010~2015年有机高分子絮凝剂水处理消耗年均增长率约为7.9%。未来5年阳离子聚丙烯酰胺市场将以最快的速度增长。聚丙烯酰胺是中国水处理中使用最频繁的絮凝剂。与美国、西欧和日本不同,在中国非离子和阴离子聚丙烯酰胺仍然是占主导地位的絮凝剂,水处理化学品用量中近60%是有机聚合物。聚丙烯酰胺产品的有效性能依赖于水的pH值。非离子型和阴离子型聚丙烯酰胺是酸性水絮凝的首选,阳离子型聚丙烯酰胺在中性和碱性水中具有良好的絮凝性能。目前聚丙烯酰胺是快速增长的水处理化学品之一,特别是市政水处理(饮用水和污水的处理)。
阳离子型聚丙烯酰胺是水处理行业中发展的趋势,同时未来几年阴离子和非离子聚丙烯酰胺将依然是主要产品。天然有机高分子絮凝剂将在中国市场越来越受欢迎,如碳水化合物衍生物、壳聚糖及其衍生物和微生物制剂等,其原因是天然有机高分子原材料生产成本比较低,来源丰富,能更好地保护环境。
3.12.3.2 聚丙烯酰胺在水处理中的作用
污水处理有多种工艺,以往多使用聚合氯化铝、聚合硫酸铁等无机聚合物作为絮凝剂。但由于无机聚合物分子量很低,絮凝剂用量很大,处理效果也不够理想,同时无机絮凝剂酸性较强,而且大量离子进入水体系中,容易引起设备腐蚀与设备沉积物问题。聚丙烯酰胺具有超高分子量特性,容易与大多数固型悬浮物进行架桥和缠绕,形成絮团。使用聚丙烯酰胺絮凝剂,或聚丙烯酰胺絮凝剂与无机聚合物絮凝剂复合使用可以有很多优点:①在达到同等处理效果的条件下,使用聚丙烯酰胺絮凝剂可以大大减少絮凝剂使用量,同时减少污泥产量;②使用聚丙烯酰胺絮凝剂效果更佳,可以明显提高水处理效果,改善出水水质;③提高絮凝沉降速度,聚丙烯酰胺具有更高的分子量,架桥缠绕作用更强,可以形成更大的絮团,絮团沉降速度更快,缩短处理时间,有利于污泥的脱水;④使用条件更温和,聚丙烯酰胺絮凝剂使用范围接近中性范围,更适合一般污水的pH。而无机絮凝剂往往在酸性条件,在药剂制备、产品使用时,对设备材质和水质pH的限定条件较多。
水处理用聚丙烯酰胺种类很多,常见的有非离子型、阳离子型、阴离子型、阴阳离子两性型,其产品又依分子量、离子度、共聚单体以及产品结构的不同分为不同的牌号。在特定应用场合,聚丙烯酰胺的牌号选择尤为重要,选型的准确与否将直接影响到产品的使用效果。通常聚丙烯酰胺选型时主要考虑产品的分子量和离子度指标。根据悬浮物沉降的斯托克斯沉降公式:
式中,v为粒子的沉降速度;ρ和ρ0分别为球形粒子与介质的密度;r为粒子的半径;η为介质的黏度;g为重力加速度。
从公式中可知,当使用聚丙烯酰胺作为絮凝剂时,絮团沉降的速度与密度差成正比,与絮团尺寸的平方成正比,与系统的黏度成反比。对于特定水质情况,希望得到快速沉降的絮体,需要尽量增大絮团尺寸,同时控制体系黏度。在聚丙烯酰胺作为絮凝剂使用时,首先聚丙烯酰胺表面电荷与悬浮物表面电荷中和,降低颗粒物表面ξ电位,降低颗粒物静电排斥力,然后利用高分子长链结构的架桥网捕作用使颗粒物团聚,使絮团体积增大,沉降速度加快。
现场药剂选型时,应当首先考虑水质系统对电荷的要求,根据水以及固形悬浮物对电荷的需求选择适当的离子度。通常分子量越高的絮凝剂架桥能力越大,形成的絮团也越大,但在实际应用时,水处理设备对絮团情况的要求不同,对药剂分子量的需求也不同,药剂选型时需要考虑设备情况。
从上述讨论中可以看出,在絮凝剂选型中最重要的是絮凝剂的离子度与固体悬浮物的匹配程度。匹配程度越高,絮凝效果越好。但絮凝剂在使用过程中还受到其他各种因素影响。
(1)黏度 水体的黏度会影响到絮凝剂使用效果,这一点经常被忽略。首先根据斯托克斯沉降公式,黏度的上升会导致沉降速度降低。若没有足够的沉降时间,小絮团来不及形成完全沉降,容易导致上层清水浊度和COD上升。另外黏度上升后,分子间运动受阻,碰撞频率降低,各种反应速度降低。絮凝剂溶液和水体充分混合时间延长,絮凝剂和固形悬浮物之间反应变慢,若没有足够的搅拌强度,容易导致絮凝剂反应不均匀,部分悬浮物表面吸附过量絮凝剂分子,表现为加药过量的情况,悬浮物表面电荷反转,表现为分散性,难以形成良好絮体,同时絮体会发黏粘壁;而另一部分悬浮物则由于表面吸附絮凝剂量不足,无法形成大絮团。
(2)搅拌强度与反应时间 在污水与絮凝剂接触后需要一定的搅拌强度和搅拌时间。若搅拌强度不足,反应时间过短,则絮凝剂无法与固形物均匀混合,会发生类似水体黏度过高的情形。若搅拌强度过高,或搅拌时间过久,絮凝形成的絮团会在长时间搅拌情况下被搅拌打散,打散后的细小絮团在搅拌停止后难以自动重新复聚,絮凝效果降低。
(3)pH 聚丙烯酰胺主要使用的单体包括丙烯酰胺、丙烯酸(盐)和阳离子单体DAC。聚丙烯酰胺中的丙烯酰胺单体和DAC单体在水溶液中稳定性不足,在高pH和低pH条件下均会发生一定副反应,尤其是水解反应。在使用阳离子聚丙烯酰胺絮凝剂时,由于阳离子聚丙烯酰胺中含有丙烯酸酯衍生物单体DAC单元,DAC在中性条件下就开始水解,且聚合物水溶液浓度越低,水解速度越快。在使用絮凝剂时,首先需要将絮凝剂溶解成水溶液,并需要数小时时间使用完毕。多数现场使用地表水或回用水溶解聚丙烯酰胺,水质往往略偏碱性。
聚丙烯酰胺溶解后会在几小时内就发生明显水解现象。DAC上的酯基和丙烯酰胺的酰胺基水解后都生成丙烯酸根,形成阴离子中心,形成的阴离子与剩余DAC上季铵盐阳离子基团发生分子内耦合,导致分子链卷曲,黏度下降,产品使用效果也明显下降。水解严重时,还会产生分子间电荷交联,产生絮状不溶物,吸附在设备表面,造成设备堵塞,严重影响药剂使用和处理效果。图3-7表示了不同聚丙烯酰胺水溶液在不同pH条件下黏度随时间变化情况。pH在4~5范围内时,黏度几乎不随时间变化,水溶液稳定性很好;当pH到6时,就可以明显看到黏度降低,但在通常的使用时间范围内变化仅有5%;当pH超过7时,发生明显水解现象,常温1.5h,黏度便会下降10%。

图3-7 阳离子聚丙烯酰胺溶液在不同pH条件下黏度随储存时间衰减情况
(4)水温 絮凝过程是一个吸附和缠绕的过程,水温对絮凝效果有比较复杂的影响。当水温较高时,聚丙烯酰胺分子链与固体悬浮物碰撞次数增加,有利于分子在悬浮物表面的吸附。但温度过高时,一方面分子运动过于剧烈,形成的絮团不稳,另一方面聚丙烯酰胺水解速度也会加快,同时悬浮物布朗运动加剧。因此聚丙烯酰胺若要取得较好的絮凝效果,需要合适的温度范围。
3.12.3.3 聚丙烯酰胺在给水处理中的应用
给水处理是通过水处理工艺去除水中的杂质,使水质符合使用要求或相应标准。传统的给水处理包括混凝、沉淀(或者气浮)、过滤和消毒等。随着水源水质的恶化尤其是有机污染物的增加,需要预处理和深度处理。
根据水源的特点,给水处理中具有多种处理方法,分别处理水中的颗粒物、有机物以及其他有毒有害物质。处理的基本方法和基本工艺如下。
(1)基本方法
①去除颗粒物。方法有:混凝、沉淀、澄清、气浮、过滤、筛滤(格栅、筛网、微滤机、滤网滤芯过滤器等)、膜分离(微滤、超滤)、沉砂(粗大颗粒的沉淀)、离心分离(旋流沉砂)等。
②去除、调整水中溶解(无机)离子、溶解气体的处理方法。处理方法有:石灰软化、离子交换、地下水除铁除锰、氧化还原、化学沉淀、膜分离(反渗透、纳滤、电渗析、浓差渗析等方法)、水质稳定(水中溶解离子的平衡,防止结垢和腐蚀等,详见本书第5章)、除氟(高氟水的饮用水除氟)、氟化(低氟水的饮用水加氟)、吹脱(去除游离二氧化碳、硫化氢等)、曝气(充氧)、除气(锅炉水除氧等)等。
③去除有机物的处理方法。方法有:粉状炭吸附、原水曝气、生物预处理、臭氧预氧化、高锰酸钾预氧化、过氧化氢预氧化、预氯化、臭氧氧化、活性炭吸附、膜分离、大孔树脂吸附(用于工业纯水、高纯水制备中有机物的去除)等。
④消毒方法。方法有:氯消毒、二氧化氯消毒、臭氧消毒、紫外线消毒、电化学消毒、加热消毒等。
(2)基本工艺 饮用水处理的工艺分成:①饮用水常规处理工艺;②在饮用水常规处理工艺的基础上,增加预处理和(或)深度处理的饮用水处理工艺;③其他特殊处理工艺。
国内聚丙烯酰胺絮凝剂以固体颗粒形式为主,聚丙烯酰胺在使用前需要先将其溶解,配制成一定浓度的溶液,溶解装置通常为带有搅拌的溶解釜或三厢式泡药溶解釜。溶解后的药液通过分配器加入污水中,常用的投加方式有泵前投加、高位池投加或计量泵投加等。
聚丙烯酰胺有时需要用一定温度的温水进行溶解,以加快药剂溶解速度,通常水温可以控制在40~50℃,过高的水温容易加速聚丙烯酰胺的水解。溶解时需要先在反应釜内加一定量水,然后将聚丙烯酰胺颗粒缓慢投加入溶解釜内,避免形成鱼眼状不溶物。溶解时需要低速搅拌,搅拌速率在60r/min左右,药液输送时采用柱塞泵或隔膜泵。高分子量的聚丙烯酰胺分子链容易断裂,在溶解和输送时应避免高速搅拌导致的剪切力过大使分子链断裂,影响产品使用效果。
聚丙烯酰胺尤其是阳离子聚丙烯酰胺,分子中带有大量的氯离子,溶解后对设备腐蚀性很强,最好使用塑料或316L不锈钢的溶解和输送材质,避免氯离子腐蚀。腐蚀后设备表面脱落的铁离子会加速聚丙烯酰胺的水解和降解,严重影响产品使用。
聚丙烯酰胺可以通过电中和和架桥方式捕捉原水中的颗粒状悬浮物、无机物和有机物,适用于各种浊度的水质。相对于无机高分子混凝剂,聚丙烯酰胺分子量高、分子链长、电荷密度较低,更适合于捕捉较大尺寸的固体悬浮物,形成絮团大,絮团沉降速度快。但对于细小悬浮物或胶体尺寸的悬浮物,则去除能力有限。对低浊度污水,通常使用复合处理方式,可以先加入无机絮凝剂,利用无机絮凝剂电荷密度高的特点先破坏胶体结构,形成小絮团后再使用聚丙烯酰胺絮凝剂絮凝,可以得到很好的絮凝效果[25,26]。在有些应用场合,可以加入超大表面积的吸附物进行处理,例如膨润土、胶体二氧化硅等物质。膨润土或胶体二氧化硅尤其是原位生成的胶体二氧化硅具有很大的表面积,在加入膨润土和硅胶后,胶体尺寸的细小颗粒物首先吸附在膨润土或胶体二氧化硅表面,再利用高分子量的聚丙烯酰胺对膨润土或二氧化硅进行絮凝沉降,可以使沉降速度提高近10倍。
絮凝剂在使用时对人畜及水体生物的毒副作用一直受到人们关注。在常用的絮凝剂中,最常见的无机絮凝剂有聚合氯化铝、三氯化铝、聚合硫酸铁或硫酸铝铁,常用的合成有机高分子絮凝剂有聚二烯丙基二甲基氯化铵(poly-DMDAAC)和聚丙烯酰胺。无机絮凝剂的铝离子,已经证明对人体、水生生物表现出毒性,能引起人的铝性脑病和骨病等铝中毒病症,因此铝盐絮凝剂在水中残留铝量受到严格的控制。世界卫生组织限定量不超过0.2mg/L,美国为0.05mg/L。在我国,与世界卫生组织要求相同,为0.2mg/L。铁盐的副作用主要是重金属以及铁盐本身的氧化腐蚀性,铁盐絮凝剂中的铁容易形成原电池,三价态铁离子氧化其他金属,还原成二价亚铁离子后又容易被空气氧化成三价铁离子,形成循环后,三价铁作为催化剂使金属设备加速氧化腐蚀。氯离子在水体中以络合离子形式存在,作为络合剂氯离子也会加速金属设备腐蚀。而硫酸铁和硫酸铝铁中的硫酸根离子容易使硫酸盐还原菌滋生,被硫酸盐还原菌还原成S2-,形成的S2-具有很强的还原性,容易腐蚀设备,S2-遇到酸性物质后形成的硫化氢气体也具有剧毒性质。
合成有机高分子絮凝剂poly-DMDAAC和聚丙烯酰胺本身没有毒性,但阳离子聚合物的季铵盐含有大量氯离子,同样存在设备腐蚀问题。此外反应过程中残留的丙烯酰胺单体也具有相当毒性。另一方面,有机高分子絮凝剂由于分子量大,往往在水中有很强的增稠作用,聚合物溶液黏度过高会影响水生生物呼吸系统,使水生生物发生窒息。
3.12.3.4 聚丙烯酰胺在污水处理中的应用
相对于原水处理,污水具有悬浮物多、成分复杂、水源不稳定等特点。聚丙烯酰胺分子量高,在污水处理中有突出的效果。聚丙烯酰胺产品稳定性好、吸附架桥能力强、官能团多、适用范围广泛,投药量少且产生污泥量少,在近年来使用越来越广泛,近年来得到快速发展。我国水处理化学品行业产能情况见图3-8。

图3-8 我国水处理化学品行业产能情况
根据污水产生的来源,污水中含有的物质有很大区别,大致可以分为几种:市政污水、工业污水、印染污水等。不同种类污水中悬浮物特性不同,处理方式与药剂选择也有所不同。
(1)市政污水 市政污水的主要污水来源是生活污水和雨水,经市政管网汇总后到污水处理厂进行处理。市政污水的特点是水质稳定、有机质较多、易生化处理。通常市政污水处理均经过厌氧-耗氧处理,然后在沉降池需要加入聚丙烯酰胺絮凝剂处理。经过厌氧-耗氧细菌处理过后的生化污水含有较多细胞结构,生物质结构携带负电荷能力强,污水表现出明显的阳电荷需求,需要中高阳电荷的聚丙烯酰胺进行处理,也可以用有机、无机絮凝剂复合使用,先使用无机絮凝剂混凝,再加入低阴离子聚丙烯酰胺絮凝。
(2)工业污水 目前中国大规模工业企业多数已经进入集中区,尤其是化工企业,基本都在集中区内集中排污,集中处理。由于各工业企业所生产产品差异很大,导致工业污水水质变化较大。根据工业产品特点,工业污水也存在很大差异,有些污水不能用絮凝剂直接处理,有些化工污水毒性较大,还需要进行预处理,降低毒性后再进行生化处理。
含金属废水中金属含量高,且通常以水溶性盐的形式出现。例如电镀行业的含Cr6+污水,将pH调至9~11后,用硫酸亚铁处理,将Cr6+还原为Cr3+,碱性条件下,金属离子形成氢氧化物沉淀,再使用聚丙烯酰胺处理,可以使金属离子含量降低到国家标准以下。再例如含镍、铅、铜等废水,也均需要适当调节pH,或用铁还原后,在碱性条件下形成沉淀,再用聚丙烯酰胺处理,金属离子去除率都可以达到90%以上,甚至可以达到99%以上。
很多有机物对微生物有强烈的毒性,有机废水通常很难用生化方式直接处理。例如制药企业的有机废水,通常需要较为复杂的处理方式。制药废水首先需要用有机-无机复合絮凝方式进行预处理,用聚合氯化铝吸附混凝,然后用聚丙烯酰胺沉降,出水再使用芬顿氧化等高级氧化技术将有机物直接氧化或氧化成可以生化处理的物质,提高污水的可生化性。经过预处理后的污水再进入生化处理模式进行最终处理。
在餐饮行业、机械加工工业以及油田采油水中含有大量油分,COD非常高。而且含油污水中由于常常含有表面活性剂,油污则形成乳化液稳定存在,处理难度很大。处理含油污水时需要先进行破乳处理,利用无机盐(例如氯化钙)或高电荷密度的聚合物(例如poly-DMDAAC)可以破坏含油污水表面活性剂稳定性,破乳后加入聚合氯化铝处理,最后加入聚丙烯酰胺进行气浮或沉降均可以去除大部分油污,少量剩余油分可以进行普通生化处理。
化工污水的处理难度最大,化工厂通常处于化工集中区。集中区内厂家众多,每个工厂开工情况不同,污水水质变化快,有毒有害物质多,COD高,处理难度大。通常需要对有害污水进行预处理,必要时采用芬顿氧化法进行预处理。然后多股污水混合后稳定水质,再根据水质情况进行生化处理。
(3)印染污水 我国染料年产量居世界第一,主要原因在于国内外印刷、涂料、塑料、纤维等相关行业快速发展,需求不断扩大。同时,染料行业也属高能耗、高污染产业。据测算[27],我国每生产1t 染料,大约排放废水744m3。在生产和使用过程中,约有10%~20% 的染料释放到水体中[28]。据不完全统计,我国印染废水的排放量约为3×106~4×106m3/d,约占整个工业废水排放量的35%,但回用率却不到10%[29]。
印染废水存在废水量大、可生化性弱、水质pH高、还原性染料对絮凝剂影响等特点,单独使用高分子絮凝剂很难处理印染废水。此外,印染行业的生产过程常常为间歇式生产,冲击式排污也使水质波动很大[30],一直是国内外难处理的工业废水之一。由于印染废水多含有带负电荷的物质,有机阳离子絮凝剂带正电荷,可以通过电中和与吸附架桥两种作用,使废水体系中的微粒脱稳、絮凝而达到良好的处理效果。
3.12.4 聚丙烯酰胺在造纸工业中的应用
3.12.4.1 造纸工业的现状
纸和纸板是人类文化与信息的载体。现代制浆造纸工业是国民经济重要支柱产业之一,其生产消费和国民经济发展高度正相关。目前,全球造纸化学品的生产和使用主要集中在3个地区,即欧美、日本和新兴国家。到2015年6月底,全球造纸化学品消费量达到201.4万吨。中国造纸行业已进入快速发展时期,并将保持高速稳定的发展。但是我国造纸化学品目前尚处于发展初期,产量低、质量不稳定、品种少、专用性差等问题普遍存在。2014年,全国造纸化学品行业销售收入548亿元,同比增长8%。截至2015年二季度,全国造纸化学品行业销售收入331亿元。此外,我国纸种及浆种结构决定了我国造纸化学品中消耗量最大的是抄纸化学品,制浆化学品和纸加工化学品的消耗量相对较低。在国际贸易方面,国际化工企业纷纷在国内设厂生产,满足了国内造纸企业对国外品牌的需求。目前绝大多数常用的造纸化学品都已实现本土生产,国产品牌已占据市场的大半江山,部分出口其他国家。
造纸工业是以纤维为原料的化学加工工业,在制浆、漂白、打浆、抄造及成纸后加工这一工艺全过程的各个阶段,均离不开各种化学品的应用。它们有的能赋予纸张各种特殊的优越性能(如抗水性、抗油性、湿强度、平滑性、印刷适性、柔软性等等);有的能用较差的纤维原料生产出更薄、更白、更牢的纸;有的能使生产过程优化、纸机运行速度提高,而且具有大幅度减少对环境污染的优点,给造纸工业带来良好的经济效益。
现代造纸工艺主要包含上述过程,如图3-9所示,根据不同纸种生产时还会用到其他工艺,整个造纸过程中最重要的阶段包括制浆和抄造。制浆过程利用化学品和机械力使木纤维分散并分丝帚化成合适形状,纸浆之后是浆料在网部的抄造,浆料纤维在网布上形成湿纸坯,经过滤水,干燥后形成纸页。

图3-9 现代造纸工艺主要过程
在浆料中,各种成分往往含有不同的亲水基团,主要有羧基、醇羟基、酚羟基、半缩醛等,这些基团在水中容易发生电离或吸附离子(主要是阴电荷离子),使得浆料表面带有电荷。浆料表面的电荷导致纤维之间产生排斥,在湿部化学过程控制中起着重要作用。由于各纸机生产线采用的原料工艺各不相同,浆料特性也有较大差异。在实际操作时,需要考虑浆料整体的电荷情况。在浆料中加入阳离子聚丙烯酰胺作为助留助滤剂可以中和浆料的阴电荷,减少浆料纤维、填料等物质排斥力,加速滤水。按照胶体表面性质,在ξ电位为0时,各物质表面电荷为0,各物质排斥力最小,聚成絮团沉降。但实际情形中,在ξ电位未到0时,就表现出明显的沉降,说明纸浆中化学情况更加复杂,需要依据现场试验对使用效果进行验证。
3.12.4.2 聚丙烯酰胺在造纸过程中的主要用途
造纸过程是将纤维木片中木纤维进行分散并重组成纸页的过程。纸浆主要成分是木纤维,无论使用原木纤维造纸或是使用二次纤维造纸,都需要先将纤维纸浆分散。纤维分散的过程是通过蒸煮、研磨过程去除纤维中杂质,活化纤维表面。经过纸浆工艺的纤维表面活性基团主要由羧基和羟基组成。造纸化学品也是针对纤维的表面性质,依据各化学品功能进行设计开发。
随着现代纸机的发展,造纸工业向着高速、宽幅特点发展,纸机速度越开越快,文化纸生产纸机车速可以开到1500m/min以上,而新闻纸则可以开到2000~3000m/min。同时随着成本节约意识的推广,薄页纸的开发与应用也逐渐增加,纸张克重有整体降低趋势。造纸设备及工艺的变化,对造纸滤水速度提出更高要求。造纸过程中使用化学助剂已经成为提高产量、稳定生产和提高产品质量的重要手段。特别是在我国,除生活用纸以外,其他纸种绝大多数使用二次纤维造纸,造纸助剂的使用显得尤为重要。
造纸助剂主要添加在造纸湿部阶段,根据助剂作用效果的特性,常分为过程助剂和功能助剂两大类。过程助剂指为加速造纸过程、稳定纸机运转用的助剂,包括助留助滤剂、消泡剂、防腐剂、胶黏物控制剂、毛布清洗剂、废水絮凝剂等。功能助剂指提高纸张某些物理指标的助剂,例如增强剂、施胶剂、填料、染料、增白剂、柔软剂等。聚丙烯酰胺由于分子结构可变性强,在造纸过程中可以扮演不同的角色。不同种类的聚丙烯酰胺在造纸过程中用作不同助剂。
聚丙烯酰胺是丙烯酰胺单体与其他单体的共聚产物,共聚物还可以通过其他方式改性获得新功能。分子量和离子度是聚丙烯酰胺最主要的两个参数,分子量与离子度的不同,使得聚丙烯酰胺具有不同的物理特性,在纸浆中可以起到分散、增强和絮聚的作用,在造纸中可作为纤维分散剂、纸张增强剂以及助留助滤剂。对于特定分子结构,还可以作为高分子表面活性剂、作为施胶乳化剂使用。
3.12.4.3 聚丙烯酰胺作为分散剂
造纸纤维往往携带阴电荷特性,因此具有阴电荷的阴离子聚丙烯酰胺可以作为浆料分散剂使用,阴离子聚丙烯酰胺吸附在纤维上之后,可以增加纤维表面阴离子密度,提高纤维间静电排斥力,促进纤维间分散。目前在国内一些纸厂仍旧使用35%阴离子度的高分子量聚丙烯酰胺作为纤维分散剂使用。而低分子量的聚合物,尤其是具有很高阴离子度的聚合物可以作为填料分散剂使用。碳酸钙是造纸过程中使用最多的填料,使用碳酸钙,既可以降低纸张成本,还可以提高纸张白度,减少纸张透光率。碳酸钙的密度比较高,使用过程中研磨粉碎后配成分散液后容易沉降,需要加入分散剂进行稳定,高阴离子度的聚丙烯酰胺或聚丙烯酸钠可以作为研磨碳酸钙的分散剂。使用时分散剂吸附在填料表面,使填料表面带有更强负电荷,能够使粒度600目以上的超细碳酸钙在水悬浮液中长期稳定存在。在造纸过程中液体碳酸钙加入后,不会形成沉降,不容易在设备表面吸附形成沉积物。
3.12.4.4 聚丙烯酰胺作为增强剂
纸张使用后,经过重新制浆工艺可以回收纤维,回收到的纤维称为二次纤维。相比于原生的木纤维,二次纤维纤具有纤维长度短、纤维表面缺陷多、残留化学品复杂、化学活性差的特点。二次纤维的特点使得二次纤维间结合力低,使用二次纤维造纸,纸张的各项性能都比较差,纸页强度性能明显降低,因此在造纸过程中必须加入增强剂,提高纸页强度。纸的强度受纤维间结合强弱控制,纤维间结合强度与结合部分形成的氢键数量和质量有直接关系,应用纸张增强剂是加强纤维间结合的好办法。根据增强剂作用的特点分为湿强剂和干强剂,湿强剂可以增加湿纸页的强度,使纸张在湿纸坯状态下或者在成纸遇水受湿以后仍具有增强性能,而干强剂只能增加纸张干燥状态下的强度,在湿纸坯和成纸受潮后则不表现增强。增强剂通过在纤维间形成分子交联提高纤维结合力提高纸张强度。纤维间的交联通过增强剂与纤维之间的化学或物理作用实现,可以是通过官能团之间的化学反应或者是通过基团之间的氢键作用。
湿强剂分子中通常设计含有容易与羟基反应的化学键,例如低分子量聚酰胺中的环氧键(例如PAE),环氧键容易与纤维表面羟基反应形成醚键,纤维间通过湿强剂分子链上的醚键增强纤维间作用力,这种作用力在浆料湿态下就可以表现出来,明显增高纸坯强度。通过环氧键反应提高湿强度的湿强剂效果十分显著,但这种湿强剂的使用存在一定限制,环氧交联时形成的醚键键能很强,纸张生产时由于切边等工艺形成的损纸难以重新解离成纤维,对纤维回收带来影响。另一类湿强剂使用乙二醛改性聚丙烯酰胺(简称GPAM),这类聚丙烯酰胺利用乙二醛上醛基与纤维上的羟基发生羟醛缩合反应,使得湿强剂与纤维间形成交联。由于羟醛缩合反应为可逆反应,利用GPAM增加湿强度时可以增加湿强剂用量,对损纸回抄的影响较小。一些大型纸机曾经大规模使用GPAM增加湿强度,但GPAM过量使用,也会带来损纸回抄问题。湿强剂的使用提高了湿纸坯的强度,对于车速的提高起到非常有效的作用。
与湿强剂机理不同,干强剂分子链与纤维没有明显化学反应。干强剂依靠增强剂与纤维间的氢键作用提高纸页干态下强度。由于氢键严重受到水分子影响,干强剂在纸页湿态下或者受潮条件下作用迅速减退。对于纸张干强剂作用的研究从20世纪60年代就已经开始,当时已经形成多种增强机理论证[31~33],因为纤维本身的强度是由其组成的纸张强度的2倍以上,所以真正决定纸张强度的是纤维/纤维的结合强度。同时,纸张强度也受到纤维自身强度的影响,这是因为纸页中存在完整的纤维。所以当时的结论是要提高纸张强度,必须从提高纤维/纤维的结合强度着手。随着造纸工业的发展,到目前为止,造纸工艺、设备、原料已经发生很大变化,纤维经过多次磨浆后,长度缩短,纤维结合力对干强剂的依赖性很强。目前对纸张干强剂的增强机理得到大家公认的有以下三条。
①纤维间氢键结合和静电吸附是纸张具有干强度的主要原因,特别是氢键结合点多,结合力强(键能82kJ/mol),是干强度产生的主要原因。加入干强剂后能加强氢键结合。总之干强剂可以增加纤维/纤维间的结合力。
②一些含有阴离子基的干强剂可以通过Al3+等和带有负电荷的纤维形成配位键。
③干强剂往往是高效的纤维分散剂,可以提高纸张的匀度,进而提高强度。这一点对增强的贡献较小。
根据氢键的特点,最初期开发使用的干强剂是淀粉,由于淀粉的易获得性以及羟基含量高的特点,淀粉成为早期最理想的增强剂[34]。淀粉结构与纤维结构最相似,在纸页中与纤维反应充分,一直是非常理想的增强剂产品,目前在浆内以及表面增强时用量仍然很大,是造纸过程使用量最大的化学品。由于淀粉氢键含量过多,淀粉与水的作用力太强,导致淀粉在抄纸过程保留率较低,白水中淀粉含量提高,水处理难度增大。并且浆内淀粉添加量过大时,纸页脱水能力降低,脱水速度减慢,导致生产效率降低。后续淀粉做增强剂逐渐被淘汰。但目前淀粉仍然作为最广泛的表面增强助剂。
在人们发现淀粉增强的弊端后,开始开发聚丙烯酰胺类干强剂。第一代聚丙烯酰胺干强剂是阴离子聚丙烯酰胺,利用丙烯酰胺上N—H键与纤维上O—H键之间氢键作用提高纸张强度。阴离子聚丙烯酰胺起到一定增强作用,提高了纤维结合力。但由于纤维表面通常带有负电荷,与阴离子聚丙烯酰胺之间存在一定的排斥力,阴离子聚丙烯酰胺不能直接作为干强剂使用,在使用时需要同时加入大量硫酸铝。大量硫酸铝的加入对纸机生产会带来一定影响,一方面硫酸铝酸性较强,硫酸铝的加入会改变纸机系统pH;另一方面,硫酸铝电荷密度很高,有可能导致纸页匀度发生变化;此外大量硫酸根进入系统后,会溶解在白水系统中,最终硫酸根通过白水溢流进入污水处理系统。硫酸根在污水处理系统中遇到硫酸盐还原菌,将被还原成S2-,S2-在弱酸性条件下就可以形成硫化氢气体,造成生产环境空气污染,同时S2-也会造成设备腐蚀。总之,S2-的存在对造纸过程存在较大影响,生产过程中需要控制硫酸铝的加入量。
在阴离子聚丙烯酰胺之后,科学家们开发了第二代阳离子聚丙烯酰胺(CPAM)干强剂,CPAM作为干强剂可以不需要加入硫酸铝,是比较优秀的干强剂产品。但考虑到CPAM的成本及稳定性因素,使得单纯CPAM干强剂并未发展开,后续也有不少对聚丙烯酰胺进行阳离子改性并用作干强剂的研究。例如用聚丙烯酰胺与甲醛、二甲胺作用的Mannich改性方法[35],利用聚丙烯酰胺碱性条件下被次氯酸钠氧化的Hofmann降解法[36~41],使用阳离子聚丙烯酰胺作为干强剂,尽管找到了一些改性方法,但从制造过程看,也均比较繁琐。此外在纸浆原料较差时,浆料中大量的阴离子垃圾对阳离子聚丙烯酰胺也有很大影响,制约阳离子聚丙烯酰胺在干强剂应用中的发展。
第三代聚丙烯酰胺干强剂,是阴阳离子两性聚丙烯酰胺。第三代聚丙烯酰胺由日本人开发并推广使用,也是目前使用最广泛的干强剂,初步估计,国内每年两性聚丙烯酰胺干强剂消耗量在30万吨左右,国内有众多厂家生产两性聚丙烯酰胺干强剂。两性聚丙烯酰胺干强剂主要为40万~50万分子量的阴阳离子两性聚丙烯酰胺,单体成分有四类:丙烯酰胺、叔胺、阳离子单体和阴离子单体。干强剂设计中充分考虑各组分的用途和功能,丙烯酰胺链节提供基本的分子量,叔胺单体中的氮原子提供电子对形成氢键,阳离子单体提供干强剂与纤维结合的驱动力,阴离子单体则对抗浆料系统中阴离子垃圾,保护阳离子基团。两性聚丙烯酰胺作为纸张干强剂使用,具有明显的优势:①两性干强剂阴阳电荷基本平衡,那些未被留着的助剂随白水排出后再循环使用时,不会失去电荷平衡,从而可保证纸机良好的运转状态;②在中性或弱酸性抄纸中,离子电荷的平衡敏感度较大,体系较容易出现过阳离子化,造成湿部失控,而使用两性干强剂可以使体系得到控制。两性助剂比阳离子助剂更能有效地提高纸页的强度、填料留着率和纸机的滤水,从而可提高纸机车速,大大减轻白水处理负荷。当今从酸性抄纸向中性、碱性抄纸的转变,开发性能良好的两性助剂将是今后纸张增强剂开发的一个热点。
3.12.4.5 聚丙烯酰胺作为助留助滤剂
造纸过程是将木纤维分散并重新分布的过程。在纸浆抄造过程中,需要木纤维在织网上进行纤维的堆砌和水分的滤除。早期造纸使用原木纤维,纤维质量好,浆料中加入的其他物质(如填料)少,不需要过多考虑浆料保留的问题。随着造纸工业向现代化发展,原木纤维逐渐被回收纤维替代,现在造纸使用原料几乎100%为回收纤维(生活用纸和特种纸仍以原木纤维为主)。回收纤维在多次磨浆后产生大量碎片,碎片尺寸小于200目即称为细小组分。细小组分尺寸小,容易透过成型网缝隙,进入白水系统,一方面造成纤维流失,另一方面也给后续水处理环节带来很大压力。细小组分比表面积大,表面吸附离子更多,负电性很强,组分间排斥力也大,对造纸过程产生很大影响。此外,在造纸过程中为增加纸张白度,同时降低造纸成本,在纸张中添加大量碳酸钙。造纸用碳酸钙在研磨过程中需要加入分散剂,分散剂主要是丙烯酸钠共聚物,具有很强的阴电性。由于碳酸钙研磨粒径很细,粒度一般都为0.2~10μm,而纸机所用铜网网目则比较大,为40~100目,相当于150~250μm。一般在抄造过程中,填料只有50%左右的保留率,其余一半会随白水流失。填料粒度小,表面电荷密度大,本身密度又高,在造纸抄造过程中,留着更加困难。
造纸过程加入助留剂,提高细小组分的留着,可以:①增加留着在纸页中的细小纤维和填料,节约纤维用量,降低水处理负荷;②降低白水中细小组分含量,减少沉积物造成的纸机障碍;③细小组分表面积更大,对施胶剂、增白剂等其他助剂的吸附能力更强,提高细小组分留着有利于提高施胶效果和增白效果;④纸张抄造过程,由于水的单向通过,会造成纸页z方向的梯度变化,细小组分的留着可以减轻这种z方向梯度变化,减小纸页两面差异。
现代纸机车速设计很高,为实现造纸高车速生产,要求造纸抄造过程可以迅速脱水,尤其是第一步自然滤水过程,要求尽量多的水分在极短时间内快速脱除,同时还要保证纤维排布的均匀程度。常规浆料中含有的亲水性基团容易吸附水分子,自然脱水困难,无法跟上现代造纸的步伐,尤其是高速纸机和高克重纸生产过程,对滤水速度要求更高。需要加入助滤剂使细微纤维在纤维表面上絮凝,减少湿纸孔目堵塞和增加透过性作用。助滤剂的加入,可以:①降低浆料纤维表面吸附阴电荷数量,减轻纤维间排斥;②高分子量的助滤剂加入后,纤维形成絮团,表面积降低,有利于水分子快速通过;③助滤剂上阳离子与纤维阴离子中和后,纤维亲水性下降,表面接触角升高,避免水分子在纤维表面铺展形成氢键和浸润,导致纸页脱水困难。
现代造纸细小组分填料的保留以及快速脱水的困难要求在造纸过程中必须加入相应助剂,提高细小组分在纸页中的留着率,同时提高纸页脱水速率。这就必须使用提高留着和滤水能力的助留助滤剂。
助留助滤剂的品种很多,按助留助滤剂本身的结构和物性可分为无机物、有机高分子聚合物、表面活性剂,其中有机高分子聚合物的助留助滤剂有很多种类,主要是以有机胺(铵)盐的衍生物为主,还有聚氧乙烯(PEO)、淀粉等,其中以聚丙烯酰胺最具代表性。滤水作用和留着作用在促进分散组分的絮凝这一点是相通的。所以两者在性能方面有许多相似之处。助滤剂的种类主要有聚乙烯亚胺、聚丙烯酰胺、阳离子乙烯系列的聚合物等。初期使用的助滤剂为聚乙烯亚胺。之后由于聚丙烯酰胺降价以及各种改性聚丙烯酰胺的研制,渐渐以应用聚丙烯酰胺为主。
造纸行业中高分子量、低电荷密度的阳离子聚丙烯酰胺是最常用的助留助滤剂之一。因为其所带电荷与纤维所带的电荷相反,可直接与无机盐离子、纤维以及其他有机高分子发生静电桥梁作用,可以起到很好的絮凝作用[39],且不受浆料 pH值的限制。阳离子聚丙烯酰胺用在造纸助留助滤过程中,利用细小组分和填料表面的阴电性,用阳离子高分子聚电解质对其进行阳离子化,以增加细小纤维和填料颗粒与纸浆纤维吸附,从而提高填料的单程留着率,并减少白水中的纤维和填料含量,减少流失从而降低成本,还可以降低浆料上网的浓度和灰分,延长成型网的寿命。
助留助滤剂的发展经过很长时间的演变,并且随着造纸技术、造纸原料的变化也逐步发生变化,助留助滤剂结构越来越复杂,同时由单一组分的助留助滤剂逐渐发展成助留助滤系统。
(1)阳离子聚丙烯酰胺助留助滤剂 中分子量低电荷密度的阳离子聚丙烯酰胺在造纸中是最常用的助留助滤剂之一。使用阳离子聚丙烯酰胺助留助滤剂可以减少纤维和填料流失从而降低成本,还可以降低浆料上网的浓度和灰分,延长成型网的寿命,并且纸页的平滑度和不透明度可以得到改善。在很多现场条件下,单独使用阳离子聚丙烯酰胺就可以实现助留助滤的效果。同时随着使用的聚丙烯酰胺分子量提高,滤水速度会逐渐加快,架桥缠绕作用增强也会使系统保留率提升,但由于分子量提高后,浆料形成絮团尺寸过大,絮团紧密且不易分散,会导致成型网上浆团难以分布均匀,纸页中局部区域缺浆,在纸机超过一定车速后,纸页中会缺失浆料的地方在牵引力下强度不足易引起断纸,这个问题在纸机压力筛性能提高后有所改善。
造纸过程是复杂的物理化学过程,助留助滤剂加入浆料后,在短时间内发生一系列物理化学变化,纸机环境对助留助滤剂效果发挥也有很大影响,通常人们认可的助留助滤剂作用机理大致包括电荷吸引、电荷中和以及架桥机理。
①电荷吸引机理(图3-10)。由于纤维素本身带有负电荷,与阳离子型的丙烯酰胺聚合物将会发生较强的相互吸引力,这不仅仅是相反电荷吸引的作用,同时也有着分子间相互吸引力的贡献,其中,微粒在液相中具有的速度引起碰撞也使电性吸附成为可能。这种作用类似于晶格中的序列排布,少量阳电性的聚丙烯酰胺在浆料中形成晶格中心,通过阳电荷把表面带有负电荷的纤维、细小组分以及填料拉近。

图3-10 纤维间电荷吸引机理
②电荷中和机理。阳离子型的聚丙烯酰胺用于造纸湿部中,会选择性地在阴电荷表面进行吸附,这种吸附通过包括氢键、范德华力、离子键作用力等吸附于纤维和填料之上。当阳离子聚丙烯酰胺吸附在纤维和填料上后,会中和纤维上的负电荷,降低纤维与填料间ξ电位,减小纤维与填料之间排斥力,促进纤维的絮凝。
③架桥机理。聚丙烯酰胺添加在纤维悬浮液中,部分纤维会吸附在聚合物表面。在水流作用下,细小纤维并非平贴在聚合物表面上,而是处于伸展状态。在此基础上,纤维可以继续缠绕在聚合物上,在长度达到一定的情况下,便可以使两分子的聚合物相互联结,达到纤维絮凝的效果。但是,同时受到水的剪切力的影响,架起的桥链可能会断开,这一影响对絮凝作用是极为不利的。随着纸机车速提高,液体流动摩擦会导致浆料内剪切力提高,导致絮团破碎,更高分子量的聚丙烯酰胺可以形成更为密实的絮团,能够有效抵抗絮团破碎的程度,因此近些年阳离子聚丙烯酰胺也有向更高分子量发展的要求。
助留助滤剂主要依赖分子链表面的电荷以及分子链长度实现电荷吸引、电荷中和以及架桥作用。溶液中有很多因素会影响到聚丙烯酰胺的助留助滤效果。
④电荷需求。在以原木浆为主要原料的造纸环境中,浆料中杂质不多,主要为少量的木质素等,浆料中阴电荷主要来自于纤维表面。加入助留助滤剂后,纤维很容易与助留助滤剂反应,实现留着和滤水效果。随着造纸成本压力,废纸浆和填料大量应用于制浆造纸,尤其是板纸中全部使用废纸浆,甚至于有些纸种生产时添加部分浆渣。废纸在重复利用时,纸张表面颜料脱色时形成的细微颗粒、废纸中残留的胶黏物,都会带有阴电性,对造纸过程起负面效果,通常称为阴离子垃圾。再加上造纸过程中磨碎的木纤维、填料和其他添加物,多数以阴电性存在。这些物质尺寸小、表面积大,在浆料中对助留助滤剂的作用影响最大。通常在遇到系统阴离子垃圾多的机台需要额外添加硫酸铝或阴离子垃圾捕捉剂来屏蔽阴离子垃圾带来的负面作用。
(2)双元助留助滤系统 在实际生产时,浆料情况往往更加复杂,因此逐渐衍生出其他助留助滤剂体系,例如针对小尺寸细小组分的双元助留助滤系统。双元助留助滤系统主要针对系统中的细小组分干扰以及压力筛的强力分散。双元助留助滤系统已经成为现代造纸的主要方法。根据双元组分的不同,双元助留助滤系统包括多种搭配,在不同的机台有不同的使用特点。
①补丁-桥架系统。补丁-桥架系统主要针对系统中的阴离子细小组分,为避免细小组分干扰助留助滤剂正常运作,同时提高细小组分的保留,加入第二组分以适应复杂系统。补丁-桥架系统主要由中高分子量低阳离子度聚丙烯酰胺与低分子量高离子度聚合物组成。系统中先加入低分子量高阳离子度的聚合物,这类聚合物由于分子量很低(通常小于100000)。在浆料中反应活性很高、容易首先与浆料中的细小组分反应,因此也成为阴离子垃圾固定剂或定着剂。定着剂通过电荷作用吸附在细小组分表面,像补丁一样遮盖阴离子垃圾表面阴电荷,同时也促进细小组分间的微絮聚。细小组分通过微絮聚作用尺寸增大,与纤维具有相同数量级,之后在加入阳离子聚丙烯酰胺助留助滤剂时,可以有效进行絮聚,并形成大絮团实现留着。
②康波季尔系统。康波季尔系统由硅胶与阳离子淀粉组成。康波季尔系统中使用的硅胶为液体硅胶,平均胶体尺寸大约为15nm,硅胶颗粒为串行结构,平均每串包含10~20个二氧化硅颗粒。硅胶在碱性条件下能够稳定存在,在硅胶加入浆料系统后,随着系统pH变化,二氧化硅串无法稳定存在,会快速形成团聚结构,在团聚过程中大量吸附、包裹系统内细小组分。硅胶形成絮聚后加入阳离子淀粉形成最终絮聚。
康波季尔系统的优点是二氧化硅形成的微絮聚尺寸较小,使用康波季尔系统不会造成系统匀度变化。但由于胶体二氧化硅价格比较高,使用成本较大,同时强碱性原料的加入,对系统pH有一定影响。康波季尔系统在部分现场仍有一定使用,但逐渐被膨润土系统所取代。
③海德罗科尔系统。海德罗科尔系统是通过微粒絮凝作用达到理想的助留助滤效果。浆料添加阳离子聚丙烯酰胺助留助滤剂形成絮聚体,在浆料输送过程,尤其是压力筛作用下被机械力剪断,剪断后的小絮团表面由于助留助滤剂的存在带有微量阳电荷。然后再添加海德罗科尔颜料使小絮团再次凝聚,再次凝聚的絮团呈现为晶格状,可以避免过大絮团造成的纸页匀度变差。
海德罗科尔系统中使用的聚合物通常为具有中高分子量、低阳离子度的聚丙烯酰胺,海德罗科尔颜料为带有阴电荷的改性膨润土。在膨润土加入前,纸纤维的表面已经吸附了阳电荷的助留助滤剂,纤维具有阳电荷,加入膨润土后,通过其阴电荷可以解决电荷的不平衡,从而形成更牢固、更紧密的絮凝物。
海德罗科尔系统不仅适用性强,而且非常经济。在纸机运行过程中,为降低造纸成本,往往加入改性淀粉。改性淀粉不仅可以降低造纸成本,还可以提高纸张强度。海德罗科尔系统最大的优点是可以改善淀粉的留着,同时减少了溢流排放水中的有机质含量,降低COD,减轻水处理负担。
在双元助留助滤系统外,近年还开发出改进型的双元助留助滤系统,即现在所谓的三元助留助滤系统。三元助留助滤系统结合了康波季尔系统和海德罗科尔系统的做法,其组成通常包括阳离子聚丙烯酰胺、膨润土和阴离子超微粒。使用方法与以往双元系统有所区别,在压力筛前加入阳离子聚丙烯酰胺和膨润土,利用膨润土吸水润胀后的表面积吸附系统内细小组分。利用阴离子型高分子聚合物超微粒替代海德罗科尔系统中的膨润土,这种改动后,阴离子超微粒具有更高的阴离子度并且可以通过调整交联的方式调节阴离子超微粒的硬度,使得新的三元助留助滤系统具有更强的适应性。三元助留助滤系统主要用于保留比较困难的文化纸系统,以提高填料碳酸钙的保留。
(3)造纸助留助滤剂的发展趋势
①非木纤维造纸技术及助剂。现代造纸工业以木浆和回收纸浆为主要原料,我国非木材纤维原料资源丰富,草浆、秸秆原料充足,但由于干草和秸秆制浆纤维短,强度差,难以达到常规造纸要求,同时制浆过程污染较严重,导致草和秸秆难以大规模应用于造纸。这就要求开发针对非木纤维的纸浆技术,以及非木纤维浆料的增强和抄造助剂。
②适用于二次纤维回收的专用造纸助剂。为了节约木材资源,保护生态环境,再生纤维的应用、再生纸的制造已越来越受人们的重视。回用二次纤维需解决的问题有:脱墨效率、消除生产过程的障碍和强度的补偿等。因此,必须研究开发适应低水耗、低温、低化学药品消耗的高效脱墨剂,能有效脱除不同印刷方法、不同成分油墨的脱墨剂;开发能消除生产过程所产生的大量泡沫聚积、游离树脂的析出等生产障碍的助剂。二次纤维抄成的纸强度较一次纤维差,需加入增强剂加以补偿,但一次纤维所采用的增强剂若用在二次纤维上,效果往往不理想,因此,需研究开发专用于二次纤维的专用造纸助剂。
③发展能改善环境的环保及绿色造纸助剂。随着人类对生存环境及生活质量要求的不断提高,环保和绿色已成为人们关注的焦点,保护生产者和消费者的身体健康、保护生态环境免受污染的理念必须贯穿到原材料的选择、生产工艺技术及生产使用过程。因此需要开发大量“绿色新品种”,如使用全无氯漂剂,降低漂白污染,开发先进的助留助滤体系,使细小纤维和填料的流失大幅度降低,采用中性或近中性施胶使白水中硫酸铝的含量大幅度减少,从而减少白水的污染负荷。
④开发封闭循环环境的造纸助剂。随着国家对污水排放要求的提高,各造纸企业不得不将更多的处理中水回用以减少污水排放,即所谓的封闭循环。现代造纸仅少部分溢流水会排放,大多数水资源要求回用。造纸系统的封闭循环带来最大的问题就是阴离子垃圾含量升高,系统电导率上升。我国近一半造纸产能在沿海地区,尤其是山东、广东集中众多大型造纸基地,在冬季盐潮时期,系统电导率可以高达7000μS/cm,而常规阳离子型聚丙烯酰胺助留助滤剂的有效作用范围为3000μS/cm以下。阳离子聚丙烯酰胺型助留助滤剂属于聚电解质,在系统电导率高时,电离出的离子会屏蔽阳离子聚丙烯酰胺上的电荷,使助留助滤剂丧失电性导致分子链卷曲,严重影响助留助滤效果。因此需要开发针对高电导率条件的助留助滤剂。
一种思路是开发分子链刚性更强的助留助滤剂,例如用二甲基二烯丙基氯化铵替代常规使用的丙烯酰氧乙基三甲基氯化铵,利用二甲基二烯丙基氯化铵聚合后形成的六元环带来的分子刚性,使得助留助滤剂分子链在高电导率条件下不容易发生卷曲,仍然可以保留高效的助留助滤效果。结果表明,在电导率5000μS/cm 时,200万分子量的丙烯酰胺-二甲基二烯丙基氯化铵共聚物比400万分子量的丙烯酰胺-丙烯酰氧乙基三甲基氯化铵(DAC)具有更好的保留效果。同时也更能够克服阴离子垃圾的影响。
另一种思路是设计具有高度支化结构的助留助滤剂,由于众多支化链存在,使得分子链在高电导率高阴离子垃圾存在时具有不同于线型分子链的表现。超支化结构中大量支化链也增加了助留剂与填料的作用强度,在絮团经过压力筛时变得不易破碎。近几年国外开展了超支化聚合物在造纸中应用的研究。超支化聚合物具有低分子量、高阳电荷密度及高度的分支结构,使其可以用作助留剂。低分子量、高阳电荷密度使其具有凝结型助留剂的性质,高度的分支结构使其具有凝聚型助留剂的特点,而且高阳电荷密度有利于其对高阴离子化纸浆的助留作用。此外,超支化聚合物的球形或类球形的对称或准对称结构使其具有更高的抗剪切能力。
例如,Shin 等[42] 以季戊四醇三丙烯酸甲酯为核,与DAC反应,合成的三维超支化聚合物助留助滤剂对细小纤维和填料都有更优良的表现。细小纤维的留着实验表明:作为助留剂的聚合物的分子形状,支化聚合物比线型聚合物显示出更高的细小纤维留着率,表明三维支化聚合物趋向于产生更好的细小纤维留着。超支化聚丙烯酰胺在填料保留中也显示出与传统线型聚合物迥然不同的絮聚行为,通过柔性的聚合物尾端与填料粒子互相连接,由超支化聚丙烯酰胺形成的絮聚物具有紧密的结构,由超支化聚丙烯酰胺所引起的絮聚既不遵循补丁机理,也不遵循桥联机理;当处于高剪切速度下时,线型聚丙烯酰胺形成的絮聚物尺寸急剧下降,而超支化聚合物的絮聚体几乎保持不变,这说明由超支化聚丙烯酰胺所形成的絮聚物具有更好的抗剪切能力;随着聚合物浓度的增加,线型聚丙烯酰胺形成的絮聚体的尺寸不断增大,而超支化的聚丙烯酰胺形成的絮聚物尺寸则不断减小,这是超支化聚丙烯酰胺与线型聚丙烯酰胺具有不同絮聚机理的有力证据;通过添加微粒子硅胶,由超支化聚合物组成的微粒子体系形成的絮聚物的尺寸随着剪切速度的增加而进一步增加,这表明超支化聚合物在微粒子助留系统中作为助留剂具有潜在的应用;超支化聚丙烯酰胺无须强的剪切力即可破坏预先形成的絮聚物。动态滤水实验结果也表明,季戊四醇作为支化核制备的星型阳离子聚丙烯酰胺确实在保留率提高方面有不错的表现[42,43]。
3.12.4.6 聚丙烯酰胺作为絮凝剂
造纸行业是耗水大户,造纸过程中有三个阶段耗水量巨大。第一阶段是制浆阶段,在碱法制浆工艺蒸煮后产生大量废水,废水颜色呈现黑褐色,俗称造纸黑液。黑液是高浓度废液,也是制浆过程中污染物浓度最高的废液,每生产1t纸浆约需要排出10t黑液。造纸黑液含有大量的烧碱和杂质,并且含有大量木质素和半纤维素等降解产物、色素、戊糖类、残碱及其他溶出物,是一种高碱性、高COD、高木质素含量的难降解废水。造纸黑液中65%为有机物,BOD浓度在5000~40000mg/L,COD 值一般都在每升数万毫克,有的甚至高达180000mg/L,pH值在9~10。黑液中的有机物大部分由木质素构成,木质素存在于植物细胞壁内,在制浆工艺的高温、高压、高pH值的情况下溶解于水中,构成制浆废水的主要污染成分[44,45]。
第二阶段是抄造过程的网下白水,网下白水是浆料在成型网上滤出的水分,网下白水含有大量的细小纤维、填料、化学助剂与胶体物质,COD较高(1000mg/L 以上),大量排放造成生产成本浪费,大量回用又造成生产过程的干扰。第三阶段耗水是在纸页的干燥阶段,大量水分被蒸发出,以气体形式排放。
制浆造纸过程以液体状排放的水主要是制浆黑液以及造纸网下白水。制浆黑液中主要物质为有机物,难以用絮凝剂简单进行处理,用一般的微生物活性污泥法也不合适。实际情况可以采用聚合氯化铝、硫酸铝配合阴离子聚丙烯酰胺进行混凝沉降,COD可以去除约50%,同时脱去一部分颜色,然后配合膜分离技术或高级氧化技术进行深度处理。
造纸过程抄纸后排放出来的水称为网下白水。这种白水排放量大,主要成分是大量的短纤维和填料。网下白水溶解性BOD虽然很低,但悬浮物含量和溶解性胶体物质含量较高。若直接排放,既浪费水资源、污染环境,又浪费纤维。从经济效益和污染治理两方面看,网下白水的回收和循环使用都是极为重要的。网下白水可以采用机械法、沉降法、过滤法、离心分离法、生化法、化学氧化法、絮凝沉降法等方法进行处理。
为了提高效率,通常采用多种方法联合使用。常采用的综合处理方法是:①预处理,主要为物理法,如筛选、沉降、混凝、气浮,并调整pH除去部分固体物;②生化处理,主要为耗氧曝气处理,除去废水中有机质;③深度处理,此时水中COD通常已经在100mg/L以下,通过高级氧化、电化学的方式将有机质氧化分解,可以使COD降低到50mg/L以下。
一级、二级处理采用混凝法添加絮凝剂改变胶体颗粒的表面电性,使分散的胶体粒子聚集形成大颗粒并携带部分可溶性有机物沉淀聚集,这个过程无机絮凝剂主要起混凝作用,再通过高分子聚丙烯酰胺的絮凝作用加速沉降。
经过水处理后得到的上层清水通常进入制浆车间作为浆料配制使用,还有相当部分中水进入浆料稀释水使用。处理后的中水中含有少量悬浮物和未絮凝的高分子絮凝剂。因此在选择絮凝剂时需要考虑到絮凝剂的残留问题,作为浆料稀释的清水,由于需要直接与浆料混合,水中残留物质会与浆料反应。在选择高分子絮凝剂时须尽量选择不与湿部化学品干扰的絮凝剂,尤其是阴离子聚丙烯酰胺等与湿部助留助滤剂有交互作用的絮凝剂应慎重考虑,使用时兼顾清水的电荷需求等指标变化。
3.12.5 聚丙烯酰胺在矿业、纺织印染行业中的应用
3.12.5.1 矿业
聚丙烯酰胺在矿业中的应用主要涉及采矿、选矿和冶金。矿业开采和加工过程通常包括矿石开采、粉碎、浮选、溶解、冶炼等过程。在这个过程都伴随大量水的使用。我国矿石主要分布在西南缺水的地域,过程中使用的水必须经过处理并重复利用。
在矿物浮选过程中,需要将矿粉与其他杂质分离。在选矿厂(包括选煤厂)的生产过程中,脱水工序是非常重要的环节。脱水效果的好坏决定矿石利用率,直接影响经济效益。脱水一般包括沉降浓缩和过滤两段作业,在这个过程中,矿粉细度越高,沉降速度越慢,过滤过程阻力也越大。
选矿过程中,为了提高生产效率,需要加入多种化学药剂。合成聚合物则主要用于矿物加工和湿法冶金中,它们以丙烯酸、丙烯酰胺为基础。聚合物在分子结构方面是多种多样的,它们在工业上有很多用途。自20世纪60年代发现这种聚合物以来,它们的应用范围迅速扩大。
矿浆浓密通常在浓密机中进行,使矿粉颗粒从水中分离。通过加入聚丙烯酰胺可以强化浓密过程,加速矿粉颗粒沉降。这个过程中由于矿粉细度很高,需要高分子量的阴离子聚丙烯酰胺加速絮凝。这个技术在多种金属精矿中已经得到应用,通常需要25%阴离子度的高分子量聚丙烯酰胺,使用量大约在10~50g/t。聚合物的选择在这个步骤尤为重要,选型不准确或药剂加入量过大,都将导致颗粒表面阴电荷浓度增加,使沉降速度降低。
在部分矿物加工过程中,由于作业环境极端,需要一些非常特殊的聚丙烯酰胺。例如在铝矿加工时,现在90%使用拜耳法炼铝,用热的氢氧化钠溶液与铝矿石反应生成偏铝酸钠,然后使偏铝酸钠溶液与其他物质分离,由于铝矿通常伴生铁矿,使得分离后污泥为红色,称为赤泥。铝土矿中的含铁矿物主要是赤铁矿和针铁矿,经高压溶出后,含铁矿物常常以0.1到几个微米的细粒子存在,导致赤泥难以沉降。赤泥沉降过程需要加入聚丙烯酰胺加速沉降。由于分离介质具有高温、强碱性的特点,常规聚丙烯酰胺在强碱性条件下很快发生水解,无法适应赤泥沉降应用。氧肟酸(盐)类絮凝剂因其氧肟酸基团对Fe3+具有迅速而牢固的螯合作用广泛应用于赤泥沉降[32],特别是对于含针铁矿的赤泥的沉降分离,可显著降低溢流液浮游物含量,显著提高沉降速度。
在磷矿加工中,需要将磨碎的磷矿石用浓硫酸处理,获得磷酸,磷酸再与其他杂质分离。分离时其他不溶性的矿土类物质形成极细粉末,给浮选带来很大困难。浮选过程中需要加入高分子量的聚丙烯酰胺。阴离子型的聚丙烯酰胺分子链上主要有丙烯酰胺和丙烯酸钠链节,其中丙烯酸钠在溶液中电离成丙烯酸根离子,在磷酸条件下,丙烯酸根很快与氢离子中和形成丙烯酸,之后聚丙烯酰胺将失去分子链中羧酸根之间的阴电荷排斥,导致分子链卷曲,直接影响到絮凝剂的使用效果。通常在磷矿浮选时选择非离子聚丙烯酰胺,但聚丙烯酰胺在常规聚合过程中也会有大约5%的链节发生水解,即得到5%阴离子度的阴离子聚丙烯酰胺。需要使用特殊手段,合成出离子度小于1%的完全非离子聚合物才能够适应磷酸矿石浮选工艺。这也为聚丙烯酰胺合成企业提出了更高的工艺控制要求。
在煤炭行业,洗煤废水是煤炭工业的主要污染源之一。洗煤废水自然沉降非常困难,静置数月不会自动沉降,非常难处理。洗煤废水通常为弱碱性的稳定胶体体系,颗粒表面带有较强的负电荷。洗煤废水处理首先降低其ξ电位,使胶粒脱稳凝聚,同时使凝聚的颗粒絮凝。为强化废水沉降过程,可以采用混凝-絮凝沉降处理方式,先加入高电荷密度的混凝剂,破坏废水电荷结构,使胶体脱稳,再加入少量低阴离子度的高分子量聚丙烯酰胺进行絮凝沉降。
3.12.5.2 纺织印染
聚丙烯酰胺具有强的吸湿性、优良的吸附性和分散性、较好的成膜性及浆膜的光滑度、高弹性,对纤维有良好的亲和性,与各种浆料有良好的互溶性,这些特点使得聚丙烯酰胺在纺织工业中用作织物后处理剂,可以形成柔顺、防皱、防霉的保护层,因此,聚丙烯酰胺普遍用作纺纱上的浆剂和织物整理剂。用作织物后处理剂能减少断纱率;由于聚丙烯酰胺容易与织物吸附,且自身携带电荷,在印染工艺中用作印染助剂可以使产品附着牢度大、鲜艳度高,还可以用作匀染剂等纺织助剂和作为漂白的高分子稳定剂。
3.13 聚丙烯酰胺的研究及应用展望
3.13.1 分子结构设计
丙烯酰胺是非常容易聚合的单体,在均聚合和共聚合中都表现出很高的活性。聚丙烯酰胺通常用自由基聚合,聚合体系包括水溶液体系、反相乳液体系以及反相悬浮体系。在这三个聚合体系中,若不考虑体系尺寸大小因素,三个体系可以统一归结为水溶液体系。水溶液体系的自由基聚合,丙烯酰胺聚合速度很快,容易获得高分子量产品,但聚合产物结构往往难以控制,分子量分布较宽,有时还易发生交联、支化而影响聚合物的性能,难以用于制备指定结构(低分子量、窄分布、嵌段、接枝、梳型、星型等)的聚合物。
未来聚丙烯酰胺研究的方向之一便是聚合物的结构设计,通过聚合反应体系或引发体系获得具有设定结构的聚合物产品。在沉淀聚合体系中,聚合物分子量生长到一定程度,在聚合体系中变得不能溶解,将以球形颗粒从聚合体系中沉淀出来,随之聚合停止。利用该方法,丙烯酰胺在丙酮-乙醇体系中聚合可以获得一系列分子量2万~10万的产品[46~48]。利用聚丙烯酰胺在某些盐溶液中溶解度降低的原理,可以使丙烯酰胺在氯化钠或硫酸铵溶液中进行共聚合,聚合物分子量增长至500万~800万时发生沉淀,聚合物产物呈白色乳液状,俗称为水包水乳液,水包水产品在加水稀释后可以快速溶解,获得速溶性能,提供聚丙烯酰胺在某些极端速溶要求现场使用[49~51]。
活性自由基聚合方法在PMMA等单体上的研究已经很多,活性自由基聚合在聚丙烯酰胺上的应用还少有报道。已有用RAFT等活性自由基聚合应用于水溶性单体,合成出具有嵌段结构的聚合物[52,53]。以具有超支化结构的聚醚为核心,通过Br封端后,利用ATRP的方法也可以合成超支化的水溶性聚合物[54]。因聚合方法的引入可以合成出具有更复杂结构的聚丙烯酰胺,也将带来聚丙烯酰胺的应用范围扩展。
3.13.2 聚丙烯酰胺的结构与市场展望[55~60]
3.13.2.1 聚丙烯酰胺的结构
聚丙烯酰胺分子结构具有带电荷、分子链长、亲水性好的特点,根据这些特点衍生出聚丙烯酰胺产品在电中和、乳化、导电、增稠、减阻、吸水等应用方向。现有的包括作为絮凝剂、分散剂、助留助滤剂、驱油剂、减阻剂等应用方向也均是基于上述分子链特点。未来聚丙烯酰胺还会在诸如导电、吸水等特征发展应用领域,例如利用分子结构设计成导电液晶,利用吸水性能设计成吸水树脂,利用亲水的性能设计为生物材料等等[61~66]。今后聚丙烯酰胺产品在生物医药、农林土壤、电器开关等方面会有杰出发展。
3.13.2.2 聚丙烯酰胺市场展望[67~73]
第一阶段:我国聚丙烯酰胺研究开始于20世纪60年代。1962年上海天原化工厂建成我国第一套聚丙烯酰胺装置;随后,广州化学所研制的聚丙烯酰胺也开始投入生产使用;1966年兰州白银有色金属公司建成了一套聚丙烯酰胺装置。但这几个工厂的产量均很小(百吨级)。这样的状况一直持续到20世纪90年代。
第二阶段:进入20世纪90年代后,随着我国油田三次采油大量使用聚丙烯酰胺时代的到来,国内不断出现了新的聚丙烯酰胺制造商。其特点是生产规模大、生产装置的自动化程度高,配套丙烯酰胺单体的生产,生产成本大大降低。截至2016年中国聚丙烯酰胺年产量已超过110万吨,约占世界总产量的60%以上。
3.13.3 中国进口聚丙烯酰胺的状况
从20世纪80年代起,中国石油的开采方面开始大量使用三次采油技术,对聚丙烯酰胺的使用量有大幅度的增加。正如前面所介绍的那样,当时中国没有大型聚丙烯酰胺工厂,甚至连中型的都没有。因此需要大量从国外进口聚丙烯酰胺。主要的国外进口商有日本三井化学、三菱化学、法国SNF公司、瑞士汽巴公司、美国的氰特公司。进口的聚丙烯酰胺产品主要是三次采油用的阴离子产品,以及用于水处理的阳离子产品。在这一阶段丙烯酰胺和聚丙烯酰胺产品以进口为主,特别是聚丙烯酰胺,价格奇高,每吨高达40000元。
进入到20世纪90年代之后,随着国内聚丙烯酰胺工厂不断建成。到2016年为止,除了高端的阳离子聚丙烯酰胺产品外,阴离子和非离子产品的进口基本已经看不到了。
从某种意义上讲,中国三次采油技术在各大油田的普及推广,造就了中国聚丙烯酰胺行业在世界上的地位,我国已成为世界聚丙烯酰胺第一生产大国和第一使用大国。目前中国丙烯酰胺、聚丙烯酰胺的年产量占据世界总产量的60%~50%。基本上把国外进口产品赶了出去。聚丙烯酰胺的年进口量1万吨左右,与110万吨的年产量相比已微不足道。
图3-11为2006~2014年进口数据。

图3-11 2006~2014年中国进口聚丙烯酰胺的数据
3.13.4 中国聚丙烯酰胺和丙烯酰胺的出口市场
1999年之前,中国聚丙烯酰胺的出口,无从查证,即使是有其数量也小到了以吨为单位。
1992年北京恒聚公司开始研制生产聚丙烯酰胺,随后又生产丙烯酰胺单体,建成了国内第一条万吨级聚丙烯酰胺生产线。1999年又建成4万吨级聚丙烯酰胺和3万吨级丙烯酰胺生产线,随后又扩至10万吨。这是国内第一家能达到万吨级别聚丙烯酰胺生产规模的企业。
从2000年起,北京恒聚开始进军国际市场。当初聚丙烯酰胺产品还没有海关税则编码,只好采用丙烯酰胺的出口海关税则编码。到2004年,海关派人到企业进行核查,这才补充聚丙烯酰胺产品的一个单独的税则编码,见证了聚丙烯酰胺大量出口的历史。从2000年起到2008年,北京恒聚公司的年出口量均占据国内同行业的榜首。最高的年份能占到国内聚丙烯酰胺出口量的90%以上。2008年之后,各个聚丙烯酰胺厂家的生产规模不断扩大,各企业开始出口本企业的产品,形成了几大出口企业。主要企业如下:法国SNF,该企业在中国的生产工厂投产后,依靠跨国公司的实力和世界广布的销售渠道,出口量目前占据榜首,而目前国内能与之抗衡的企业不多。中资企业中,北京恒聚、安徽天润、山东诺尔、山东宝莫、河南正力、安徽巨成是出口量最大的几家企业,出口国别达到73个,最高出口量近10万吨/年。
3.13.5 出口产品类别
我国聚丙烯酰胺产品主要应用于油田方面,因此我国大部分厂家的出口均以阴离子产品为主,占到出口量的80%以上。其次为非离子产品。而阳离子产品出口量则不大,主要原因是国内企业不能生产阳离子单体或者是生产出的阳离子产品质量还不过关。国外市场与中国市场不同之处在于:国外市场是以用于水处理和造纸的阳离子产品为主的市场,这方面是我国生产企业的短板,也是我国聚丙烯酰胺产品出口的一个瓶颈。不过随着国内几家阳离子单体厂的相继建成投产,这一局面在今后的一段时间将会得到改善。
国际市场分析:根据相在数据材料,2013年全球聚丙烯酰胺市场份额及销量见表3-5。
表3-5 2013年全球聚丙烯酰胺市场销量预测

截至2015年,全球约计在150万吨。
从分布看,来自北美、亚洲、欧洲的需求约占85%的份额,其市场开发潜力巨大。
3.13.6 海关出口量分析
2004年以前聚丙烯酰胺没有税则号查不到有关数据,2000~2005年的出口量主要是北京恒聚出口的。
从图3-12可以看出:

图3-12 海关出口量
①2006~2016年10年间,中国聚丙烯酰胺出口量增长了近3倍。年平均增长率接近30%,是一个快速增长的出口产品,其年平均增长率是我国其他外贸产品平均出口增长率的好几倍。
②从2010年达到7.6万吨以后,出口量在2014年达到顶点(9.22万吨)。然而2016年出口量仅为7.57万吨,低于2010年的出口量。主要原因是我国出口的聚丙烯酰胺主要为阴离子产品,与国外主要使用阳离子产品的产品结构不吻合。要想扩大出口,就必须注重扩大阳离子产品出口。
③2016年度据统计出口聚丙烯酰胺产品6.888万吨、进口聚丙烯酰胺1.575万吨、一般贸易量聚丙烯酰胺7.549万吨、国内海关出口聚丙烯酰胺7.569万吨、不同产销国出口聚丙酰胺7.4605万吨。同时,世界经济不景气也是最近5~6年来我国聚丙烯酰胺出口量一直徘徊不前的原因之一。
④据不完全统计截至2016年国内生产聚丙烯酰胺产品的厂家有上千家,具有一定规模,年产能达到了111.7万吨,总销量达到78.421万吨/年。其中油田使用35.408万吨/年,占比31.7%;水处理使用16.4087万吨/年,占比14.7%;造纸使用5.858万吨/年,占比0.052%;采矿使用4.2753万吨/年,占比0.038%;其他使用1.37823万吨/年,占比0.012%;出口10.1314万吨/年,占比0.091%。另外阴离子聚合物34.2678万吨/年,占比30.68%;阳离子聚合物14.2710万吨/年,占比12.78%;非离子聚合物3.8652万吨/年,占比0.035%;两性离子聚合物0.165万吨/年,占比0.0015%。其他用于建筑胶水、涂料、印染、纺织等均未统计在内。
3.13.7 扩大出口的方法
①扩大阳离子单体生产规模,满足阳离子产品的出口竞争。
②提供产品的技术服务、成套设备、工程设计全套服务。
③在聚丙烯酰胺的重要使用国建立销售分公司。
④大力发展用于水处理、造纸方面的阳离子产品才能扩大出口量。
参考文献
[1]付建伟.反相微乳液聚合的研究进展[J].河南化工,2003,15(6):4-7.
[2]马希晨,邰玉蕾.5-DMDAAC-AM强阳离子型天然高分子絮凝剂的合成[J].精细石油化工,2002,19(2):13-16.
[3]曾文江,曹游,陈瑞南.国外聚丙烯酰胺生产的历史和现状.广州化工,1995,23(2):67-72.
[4]严瑞瑄.国外聚丙烯酰胺的国内外市场发展状况[C]//中国精细化工协会全国功能高分子行业委员会年会,2006.
[5]Walter M Thomas.Acrylamide Polymers//Encyclopedia of Polymer Science and Engineering.2nd.New York:John Wiley&Sons,Inc.,1987.169-204.
[6]方道斌等.丙烯酰胺聚合物.北京:化学工业出版社,2006:58-59.
[7]严瑞瑄等.水溶性高分子.第2版.北京:化学工业出版社,2010.
[8]刘建平,王雪芳,杨小敏.高分子量聚丙烯酰胺的合成与应用进展[J].化学工程师,2010,41(8):26-28.
[9]崔小明.聚丙烯酰胺的生产应用及市场前景[J].四川化工与腐蚀控制,2000,3(4):30-37.
[10]杨开吉,苏文强,沈静.低分子质量非离子型聚丙烯酰胺合成工艺探讨[J].当代化工,2006,35(8):14-17.
[11]牛太同,胡凯,涂惠民.聚丙烯酰胺(PAM)的合成与应用[J].江西化工,1996,12(4):11-15.
[12]Dianal Martin,Elena Matelasse,Gabriela Cranium.Polymeric flocculants processing by accelerated electron beams and microwave heating[J].Radiation Physics and Chemistry,2002(64):423-428.
[13]刘彭城.聚丙烯酰胺生产技术现状及发展[J].造纸化学品,2011,18(2):1-18.
[14]王少会,徐初阳.聚丙烯酰胺的工艺设计与应用研究[D].淮南:安徽理工大学,2005.
[15]李大刚,李云龙,张青海.聚丙烯酰胺类絮凝剂聚合工艺研究进展[J].黎明职业大学学报,2011,23(1):31-35.
[16]方道斌,郭睿威,哈润华.丙烯酰胺聚合物北京[M].北京:化学工业出版社,2006:26-27.
[17]张达生,朱圣贤.聚丙烯酰胺的生产现状[J].油气田地面工程,2004,23(8):60-61.
[18]Bekturov E A,Khamzamulina R E.JMS Rev Macromol Chem Phys,1987,C27:253.
[19]Gromov V F,Gaoperina N L,Osmanov T O,et al.Eur Polymer J,1980,16:529.
[20]Thomoson R A M.Chemistry and technology of water-soluble polymers.New York:Poonam Press,1983.
[21]夏俭英.钻井液有机处理剂.青岛:中国石油大学出版社,1991:77.
[22]王中华.油田化学品.北京:中国石化出版社,2001:56.
[23]张麒麟.钻井液与完井液,2000,17(5):31.
[24]Kenneth L B.Completion and Workover Fluids.Texas:Doherty Memorial Fund of AIME Society of Petroleum Engineers Inc,2000:5-10.
[25]赵福麟.油田化学.青岛:中国石油大学出版社,2000:2.
[26]孙一平,陈宝华.西南给排水,1993,(4):34.
[27]陈立丰.水处理技术,1995,21(1):46.
[28]Yang Qing xiang,Jia Zhen jie,Yang Min.Microbiology,2006,(4):144-148.
[29]Wang Yi zhong,Chen Mei xue,Hu Chun.A study of dye degradation in the combination process of photocatalytic oxidation with biochemical oxidation[J].Acta Scientiae Circumstance,2000,(6):772-775.
[30]张挺,唐佳玙,高冲.印染废水深度处理及回用技术研究进展.工业水处理,2013,33(9):6-9.
[31]朱虹,孙杰,李剑超.印染废水处理.北京:中国纺织出版社,2004:16-17.
[32]Davison R W.Theory of Dry Strength Deveopment.Dry Strength Additives.TAPPI,1980.
[33]Davison R W.The Weak Link in Paper Dry Strength.TAPPI,1972,55(4).
[34]Page D H.A Theory for Tensile Strength of Paper.TAPPI,1969,52(4).
[35]王恩碧.江苏造纸,1998,(4):26-30.
[36]许振举,张爱华.齐鲁石油化工,1997,(4):273-275.
[37]US,5039757.
[38]US,5239041.
[39]US,529282.
[40]Wang F,Kitaoka T.Tappi Journal,2003,2(12):21-26.
[41]Koper G J M,et al .Journal of Pulp and Paper Science.1999,25(3):81.
[42]Shin J H,Han S H,Sohn C,et al .TAPPI,1997,80(11):179.
[43]赵颜凤,傅英娟.中华纸业,2010,31,(241):66-69.
[44]傅英娟,石淑兰.中国造纸,2007,26,(4):19-23.
[45]肖翔,齐宇勃,章广德.环境科学与管理,2008,(2):102-104.
[46]Bremmell K E,Scales P J,et al.Colloid Surface A,2004,247:19-25.
[47]王久芬,蔡开勇,李德水.华北工学院学报,2002,21(4):312-314.
[48]王春燕,吴宗华.福建师范大学学报:自然科学版,2002,18(4):61-63.
[49]US,4929655.
[50]CN,1231650A.
[51]CN,135006A.
[52]Chatterjee,Jewrajka,Mandal.Polymer,2005,46:10699-10708.
[53]Jewrajka,Chatterjee.J Polym Sci A:Polym Chem,2006,44:1841-1854.
[54]高超.高分子学报,2004,6:877-883.
[55]赵克.国内聚丙烯酰胺的市场状况及发展前景.集团经济研究,2006,(8):93-95.
[56]鲁飞虎.聚丙烯酰胺产业现状及发展趋势探讨.化工管理,2016,(21).
[57]袁春.浅析聚丙烯酰胺产业现状及发展趋势.化工管理,2016,(35).
[58]鞠耐霜.我国聚丙烯酰胺(PAM)的现状与发展//中国造纸化学品发展论坛,2006.
[59]严瑞瑄.聚丙烯酰胺国内外市场发展状况//全国油田化学品发展研讨会,2006.
[60]曹游.丙烯酰胺、聚丙烯酰胺生产、科研应用现状和发展展望//全国工业表面活性剂发展研讨会,2001.
[61]张贞裕,张凤莲,王晖.超高分子量聚丙烯酰胺的合成研究[J].化学工程师,1995,6(51):4-6.
[62]盛平亚,宁廷伟.双液法调剖堵水剂SJD-1[J].油田化学,1998,15(3):243-247.
[63]郑健,张光焰,王海英.适用于海上油田新型调剖剂的研究与应用[J].石油钻采工艺,2007,29(4):68-70.
[64]栗敏,杨汝男,狄宏伟.阳离子聚丙烯酰胺对漂白苇浆助留助滤作用的研究[J].黑龙江造纸,2006,(4):6-7.
[65]曹孟君.一种医用聚丙烯酰胺水凝胶的制备方法[P].CN,1450118A.2003-10-22.
[66]刘咚,屈撑囤.含聚丙烯酰胺类采出水中聚合物降解的研究现状及发展[J].石油化工应用,2015,(04):92.
[67]李风亭,张冰如.我国丙烯酰胺类有机高分子阳离子絮凝剂的状况[C]//全国混凝剂行业发展战略研讨会,2000.
[68]严瑞瑄.聚丙烯酰胺发展现状[J].精细与专用化学品,2009,(17):30-33.
[69]刘志军,肖勇,李志芳.聚丙烯酰胺的现状及发展的思考[J].江西化工,2003,(2):44-45.
[70]刘彭城.聚丙烯酰胺生产技术现状及发展[J].造纸化学品,2011,(2).
[71]朱文远,赵传山.两性聚丙烯酰胺增强剂的现状及发展[C]//中国造纸化学品在造纸及纸张表面应用国际经济技术研讨会,2004.
[72]张桐郡,张明恂,娄轶辉.聚丙烯酰胺产业现状及发展趋势[J].化学工业,2009,(06):26-33.
[73]于涛.抗盐聚丙烯酰胺的分类及发展现状[J].化工技术与开发,2012,(7).